けたろーです。
九月になったとは言え、まだまだ残暑が厳しいですね。 今日は、雲行きが怪しいようで、ひと雨きそう。 雨が降ってくれたら、暑さも和らいでいい感じになるね。
さて。
ただ生産するだけじゃなくて…
ここのところ、生産現場の在り方が変わってきているように感じています。 在り方っていうと大袈裟かもだけど、簡単にいうと、生産現場の運用の仕方ですかね。
なにが変わってきたか? というと、以前までは、ただ単純に〝作る〟ことに特化して、その工程を中心に生産がおこなわれていたという感じ。 でも、最近は〝ただ作る〟だけの工程だけではダメで、作りだす以上は、その検査も含めた工程を考えなければならないというように変わっています。
もっとも、工程内での検品や最終的な検査は昔から行われていたのだけど、その様相がかわってきたというわけです。
製造者の責任。
〝物を作っていく以上、その製造者には責任がある。〟 この点に関しては、過去も今も同じです。
しかしそれが現在はもっとそれが厳格になってきていて、例えば、製造に対する履歴があって、ロットや個体の追跡調査ができるだとか、きちんとした『証明』が必要になってきたというわけです。 むろん、実際にどんな検査をしているのか? という点も注視されるべき事がらになっています。
つまり、ただモノを作るだけではなく、正当な検査を含めた上で、そのモノをリリースすることが製造者の責任になっているというわけです。
目視による検査や、官能試験などの主観的な検査は以前から工程に組み入れられているとは思いますが、それに加えて機械的な検査も必要になってきているという点は否めないですよね。
例えば、バーコード。
機械的な検査が必要だというのはどういうことか? 例えば、バーコードがそれに当たります。
今やバーコードを使ったPOSレジは当たり前の世界です。 バーコードがあるお陰で、レジでの商品価格の手打ちがなくなり、また、手打ちによる入力ミスや手打ちの手間がなくなるという利便性を生み出しました。
ボクが小さい頃は、商品をレジに持っていくとレジの人が値札を見て、レジスターに手打ちで入力してました。 商品点数が増えるとそれそれはたいへん。 レジ前には長蛇の列が… というのもザラにありましたよ。 入力ミスが起こってしまうと最悪。 (^_^;) それを考えると、今は、ピッピッで済むし、ミスもほとんどないんですから、便利になったもんです。
それに加えて、バーコードを使うことで商品の在庫管理や仕入れに関わる受発注などの効率化にもつながってますよね。
でも、ちょっと考えてほしいのですが、こういった便利な状況っていうのは、貼付されているバーコードが正常にリーダーで正常に読めるというのが前提でのこと…ですよね?
バーコードが貼付されているものの、リーダーで読めなければどうでしょうか? 市場で大混乱を招くはずです。 たまに、バーコードが読み取れず、コードを手入力で入力されるような状況に遭遇したりしますが、そういう状況が全商品で発生したとしたらどうでしょう? レジ担当のストレスは半端ないということは想像に難くないです。
市場に出す前の確認が大切。
バーコードが物理的に あるか? ないか? は目視でも確認は可能です。 しかし、重要なことは、それがきちんと読めるか、読めないか? です。
その確認には、やはり、生産現場内で事前に検査を行っておくことが必要です。 バーコードリーダにて、実際にコードを読み取り、エラーがでないことを確認するという検査をしておけば、安心ですよね。
少なくとも、前もって確認しておけば、出荷前の工場では読み取りがOKだったという証明ができるわけですから、仕向け先の問題なのかどうかといった切り分けが容易にできます。
目視検査による危険性。
目視検査などの人による〝主観的〟な検査方法は、細かなキズや汚れ、製品としての何かしらの違和感などを検知でき、また、製品の品種が変ったとしても柔軟に対応することができるため、生産現場ではごく一般的に採用されています。
しかし、一般的に人間の集中力は15分~60分くらいと言われていて、その持続性の問題により【見落とし】という人為的なミスが発生してしまうこともあります。
検査項目は増加傾向?
スーパーマーケットやドラッグストアなど、市場でいろんな商品を見ていると、最近では商品のパッケージに、POP(販促)ラベルだったり、その他、消費行動を促すためのマーケティング的な様々な仕掛けが施されています。 それらはまた、商品をより強力に販売していく上で必要不可欠なファクターになっているとも言えます。
商品を購入する客側からすれば、キャッチーなPOPが貼ってあったり、例えば、〝おまけ付き!〟などといったラベルが貼ってあったりすると、購買意欲がそそられるのもありますよね。
でも、逆に、そういった商品を生産する側からみた場合はどうでしょうか?
生産現場では、そういった〝アイテム〟が増えるに伴って、POPラベルなどの〝仕掛け〟がきちんと規定の場所に貼られているのかどうか? などの検査作業が発生し、作業の負荷が増えているという事態に陥っています。
万が一、検査ミスが発生し、それが市場に出回ってしまったとするなら…
と考えると、生産現場の責任は重大ですよね。 では、そういった不測の事態を未然に防ぐためにどうすればいいか?
実は、便利な装置を創りました! それがこれです!
一気に同時に両面検査ができる!
表と裏の両面の検査が同時にできるという〝優れもの〟の検査装置です。
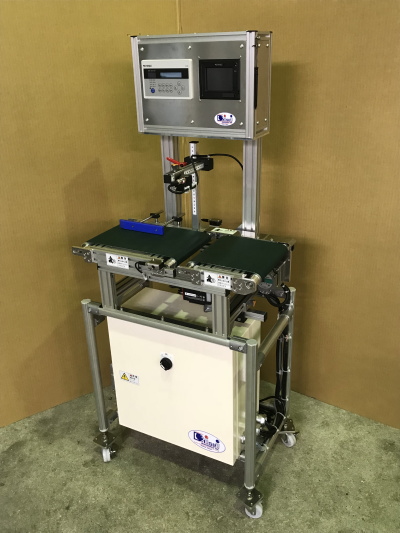
ラベルの有無やデザインの違いといった画像による検査とバーコードの読み取り検査ができ、それを同時に行います。 予め、マスターになる画像やバーコードを登録することによって、品種が異なる場合でも簡単に検査ができます。
片面づつの検査の場合、画像検査装置やバーコードチェックの装置と2台の装置を使って、それぞれに対する作業が必要でした。 また、2台の機器を接続したとしても、機器の種類によっては裏返すという手間があるのですが、この装置を使えば、両面を一気に同時に検査することができるので、作業効率が格段にあがります。 また、検査時の作業ミスも格段に減らすことが可能です。
製品をコンベアに手投入で投入すればすぐに検査が行えるため、新人の作業スタッフさんでも簡単に扱うことができます。 もちろん、ラベル貼付などの前工程からコンベアを接続してという方法でも対応可能です。
判定結果で異常がでればブザーでお知らせし、搬送を停止するというシンプルな構成です。 ご要望に応じて、NG品を分別するような機能を追加することも可能です。 多品種小ロットを扱われている場合に超オススメです!
本機の対応は、受注生産で承っております。
お取扱いの製品や、検査対象としたい項目に応じて、カスタマイズが可能です。 もちろん、既設生産ライン等への組み込みを目指した機体も製作可能です。 詳しくは、お問合せ下さい。
ご相談、お問合せはお気軽にどうぞ。