どんな風に安全を確保するか?
悩ましいこと_
それは、機械の安全性についてです。

実は、どんな風に〝安全性〟を確保していくのか? って、結構難しいんですよね…
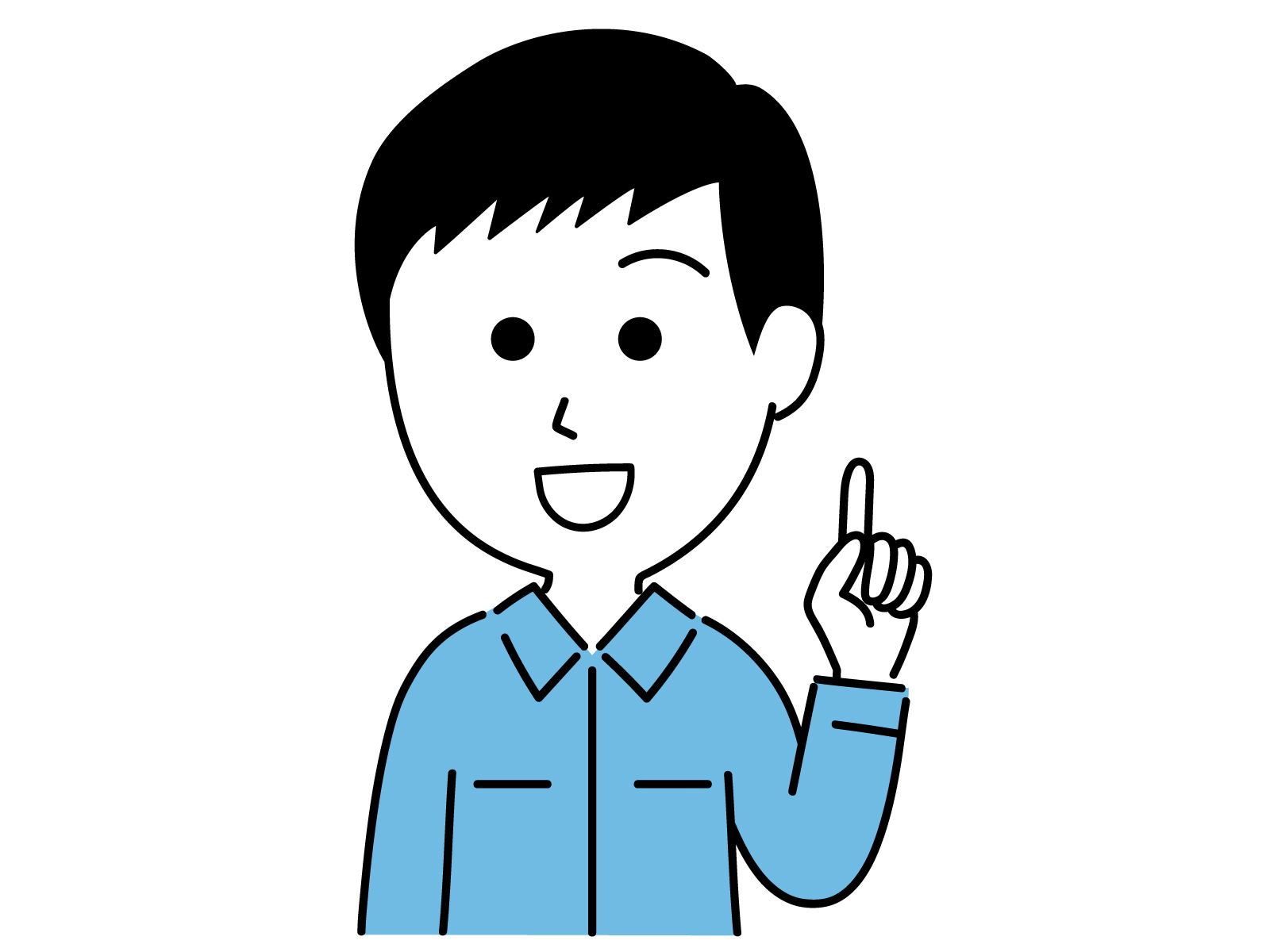
そんなのカバーしとけばいいじゃん!
たしかに、それも有効な手段で大切なんですけど…
カバーだけじゃ不十分な時もあるんですよ。 それに、カバーをつけることが『不安全』になってしまうというケースもあったりして。 (^_^;)
なのでただ、「安直・やみくも」に『カバー』という対策が安全性確保につながる… というわけではないんです。 これについては後述しますが_。
機械への『安全への取り決め』
そもそも、あなたの工場(会社)では設備や機械についての〝安全に対する取り決め〟って、ありますか?


安全に対して敏感な会社さんでは、工場内外での安全対策はもちろん、保有する全ての設備・機器に対して細かくルール付がされているところもあります。
生産活動で使用する機械の安全性は、労働環境そのものの安全にもつながってくるので、工場を運営されているところからすれば死活問題になります。 こと、重大・重篤な事故… 例えば、一番起こったらアカンことなのだけど死亡事故とか、障がいが残るような事故などが起きてしまうと工場の操業停止に陥ってしまうためです。
恐らく、重工業と言われる工場ほど、この辺りのことは厳格に決められているのだと思います。 重工業の場合では機械の一瞬の操作ミスが、甚大な災害に繋がってしまう大きなリスクがあります。 事実、安全靴やヘルメットを装着して入るような工場へお邪魔した時がそんな感じでした。
どんな業種であれ、どんな工場の規模であれ、もしものことを考えると、どんな風に安全性を確保していくか、工場としてのルールを決めておくことが大切ですよね。
__とはいうものの、工場としてのルールを設備や機械に〝個別〟に落とし込めるか? という面がもっとも 肝 になるところなのだと思います。
大前提としてのルールやガイドラインを設定したとしても、各機械にそれを適用する場合には、機械仕様的に〝無理〟が生じる場合がありますよね。 なので、臨機応変に対応… いや、〝対応する〟というか、『対応できる体制にしておく』というのが大事です。
メカ部分と制御部分。
機械を創ってる立場で、大前提のところで〝設計思想〟な面での安全性の考え方や捉え方、また、機械が構成される大前提としての設計時の〝メカ〟の部分への考え方が非常に大切だと思っていて、また、それと同時に、その考え方をどんな風に制御部分に盛り込むか? ということも大事なことだと思っています。
特に、最近の機械の状況を鑑みれば、電機制御の占める割合が多くなってきているのもあって、電機制御の部分での考え方が安全性を左右する… といっても過言ではないと思えるのです。
〝意思統一〟を図らねば…。
うちの場合での話しをすると…
実は、電機制御部分はアウトソースです。 だからこそ、安全性に関する意思統一が重要だと思っています。 ぶっちゃけ、制御に携われてきた業種(得意とされる分野)やその経験で、安全面に対する制御の考え方もずいぶん違うんですよね…
これは、私見ですけど_
機械制御ではない制御を得意とされている方は、機械制御への対応はできるものの安全への捉え方が、こちらとは若干ずれる傾向にある。 また、機械制御は得意であったとしても、分野によっては考え方がこちらと違う… と言う感じです。
また、こちらが〝当たり前〟だと思っている安全への考え方も、人によってはそうでもないという場合があったりします。 というか、実際ありました。 概ね、異常が起こった時にそれが発覚するんですよね… (涙)
〝え? なんで停まらないの?〟 とか、『そこは、その動きで停めたらアカンやん。』とかとか。 それがプログラムミス的なことならやむを得ないとは思うんですけど、考え方や捉え方が根本的に違う時には、制御設計の本質の部分にも関わってくる場合があるので要注意なのです。 本質的に違う場合には、全体を通じて動作を見た時に、異常時へのつじつまが合わなくなるという…
だからこそ、事前の確認、もしくはテスト段階で逐次確認がいるというわけなんで、すごく痛感してます。
〝停まる〟の考え方。
制御を考える上では、『異常時にどうするか(どう振る舞うか)』が もっとも重要なことなのだと思っています。
なんでか? というと、正常な動作は、誰しも普通に考えられてまとめることができるからです。
でも、むしろ重要になるのは、異常が起きた時にどのような振る舞いで制御するか? ということで、逆を言えば、どれくらい異常の種類が想定できるか? ということなんです。


異常状態には、『作業スタッフにこうされたらどうする?』とか、『ここでこうなったら、どうする?』とか、人手が起因する場合や、扱うワークに起因する場合とか、様々な状況が考えられますよね?
概ね、「こんなのあり得ね~」とか、『まさか!』という状況が起こった時への〝制御の抜け〟があるかないかで、制御の良し悪しが決まってくると思います。
だからこそ、どこまでそれを想定するか? という想像力が必要になってくるんです。 という意味では、機械的な制御への色んな場数を踏んだ方の方が長けているのかなと思えます。 例えば、停まり方、停め方がそれです。
異常が発生した場合、どのように機械を停めるのか?
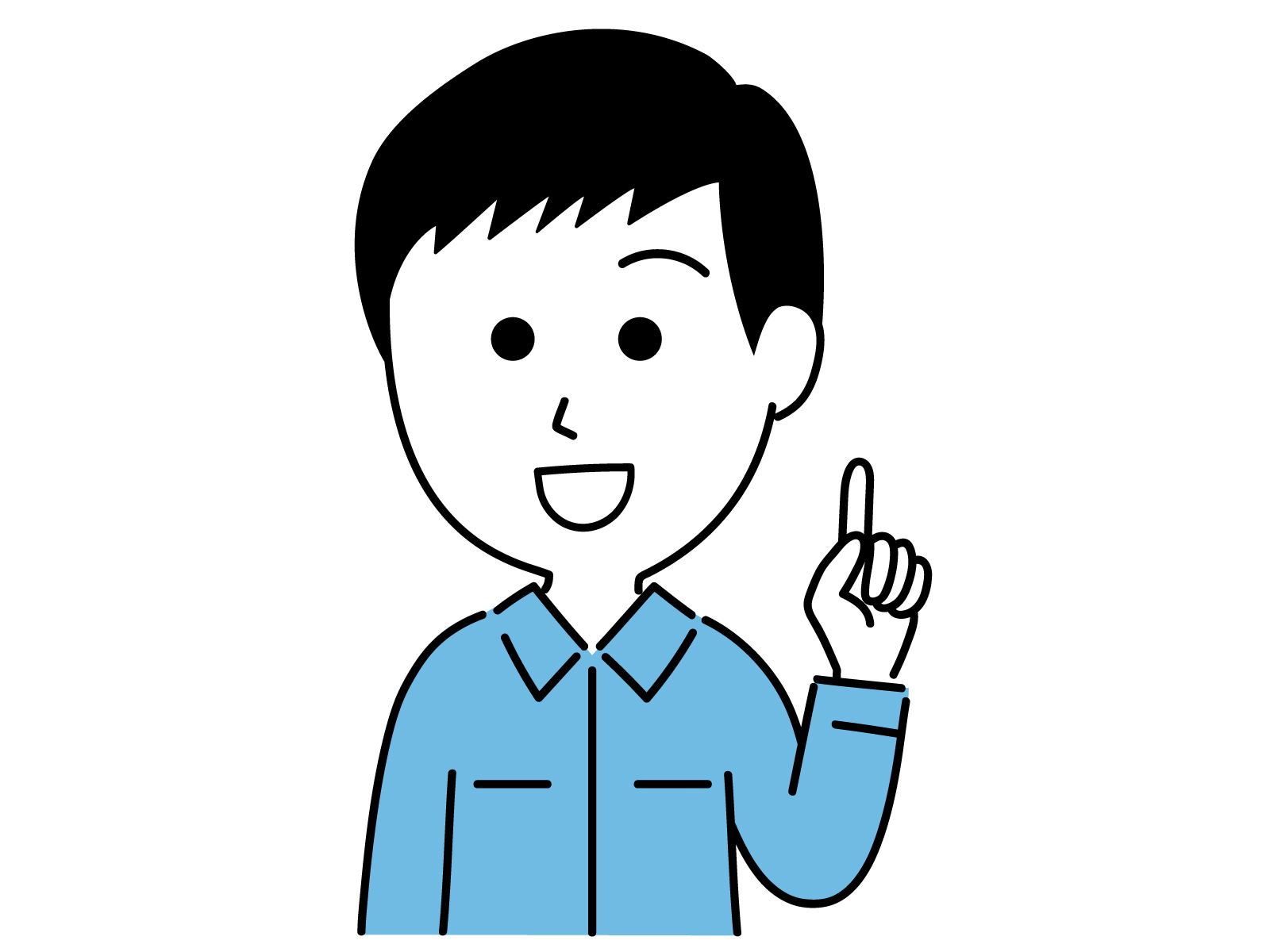
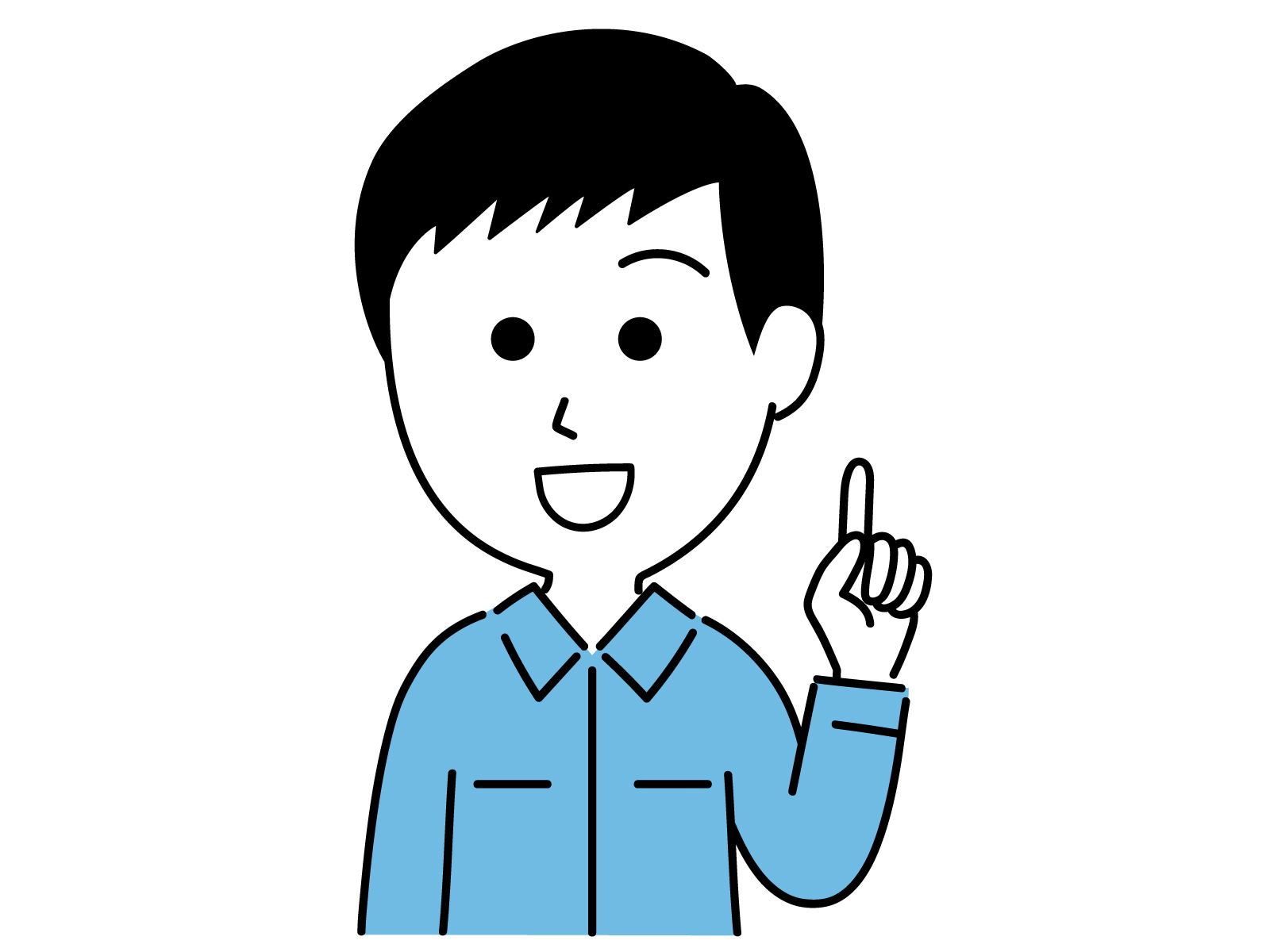
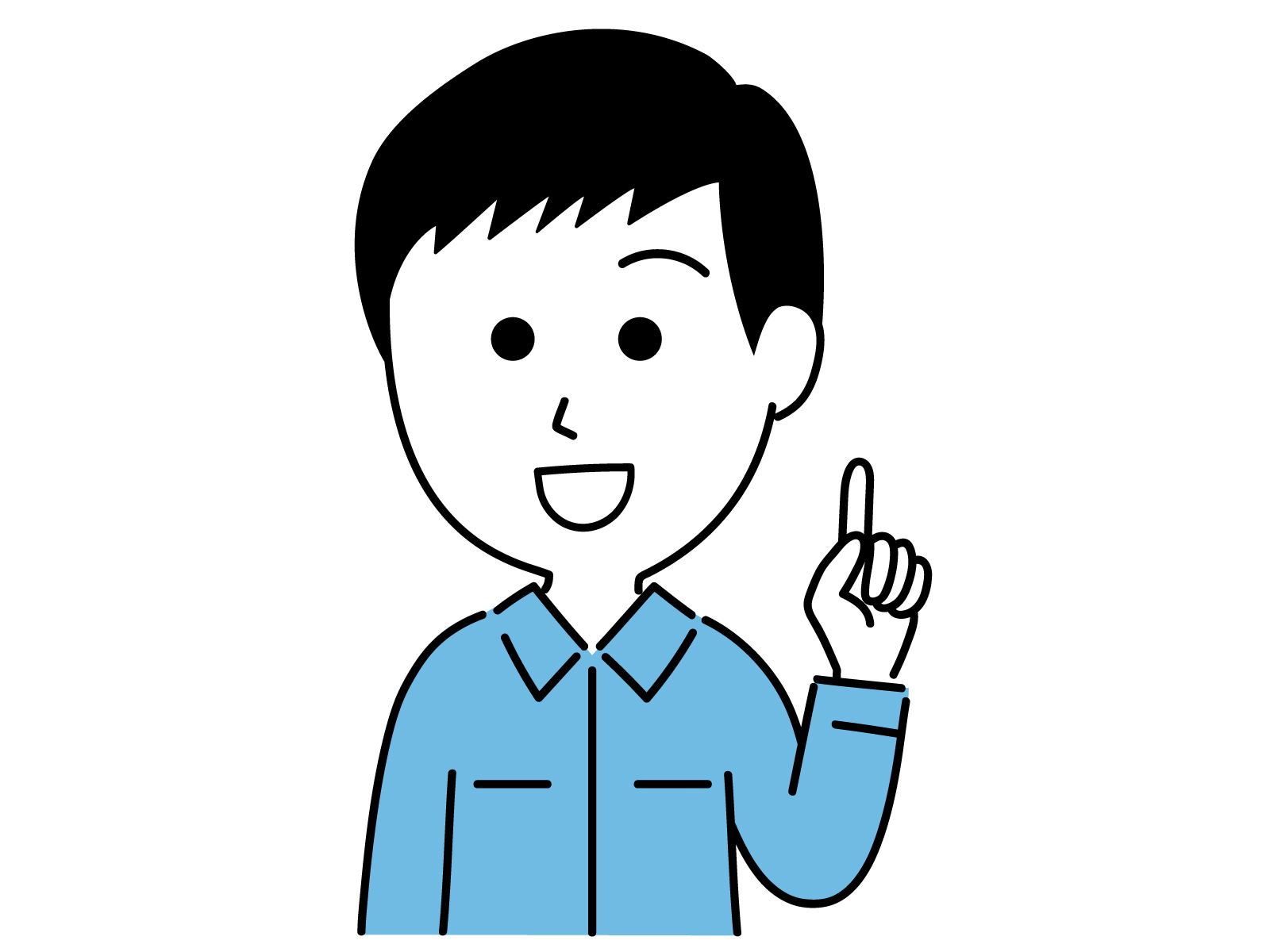
単に停めたらええんちゃうん?
なんて風に、単純に思われるかもですが実はそうでもないんですよね。 〝停める〟って基本的なことであって、且つ、非常に重要なことなんです。 単に停めるだけだと、ヤバイ状態になってしまう場合があるので、そこも経験値や状況に対する想像力が必要になってきます。
『安全の側』を考える。
うちの場合、包装機を創ってる関係でヒーターを使った挟み込みの〝プレス〟のような機構をよく使うのですけど、異常が起きた場合、そのまま停めてしまうとその状況によっては重大な事故につながる可能性があります。
もし、そこに『体の一部』が挟まるという状況があったとして、挟んだ状態で停止してしまうとどうでしょうか? 挟まれる状態に加えて、高温化にさらされてしまうという状況が発生してしまいます。
なので、挟まる危険がある場合などには、その場で停止させるのではなく、それを回避する方向へ移動させて停止するというのが鉄則です。
これは以前に聞いた話なのですけど、ある機械でメンテナンスの作業中だったかにプレス部で腕(指?)の噛みこみがあって、非常停止ボタンは押されたものの『プレス状態で停止』したままになって、えらいこっちゃに陥った… という。
状況はご想像にお任せしますが、その状況、目も当てられませんよね…


ぶっちゃけ、昔の機械には安全性への配慮という概念がなくて… 滝汗
むき出しというのが主流だったりします。 ある意味、むき出しの方が怖さを知れるというのもありますけどね。 あと、真空を使った吸着動作の部分についてもそれなりのリスクを考える必要があります。 うちでは、停止時に吸着状態を開放するという制御はやめてくれと伝えています。 なんでか?
不用意に吸着を切ってしまうと、吸着している物体が落下して災害が起きる可能性があるためです。 また、移動動作中の場合では、吸着している物体が飛んで行ってしまう可能性もありますよね。
いずれにしても、どれが『安全の側』なのかを考えて停止するということが重要です。 作業者の安全を第一に考えながら、機械(処理)へのダメージも最小限抑えるという制御がいるということです。
電動化で楽になった?
制御に関して言えば、電動化することで制御がやりやすくなって安全対策も行いやすくなったという面があります。 もっとも、前述の通り『設計思想的』な意思統一がベースにはなりますが…
やりやすくなったとはどういうことかと言えば、これはエアー機器との比較にはなるんですけど_
エアーシリンダの場合、電磁弁の操作が入るとエアーが解放され、エアーシリンダは動作を開始します。 この時、一旦動作が始まると途中で停めれないんです。
もっとも、使用する電磁弁である程度の制御はできるのですけど、もし、電磁弁の選択をミスっていた場合、エアーシリンダの場合だと行ったっきりになってしまうため、安全面での支障が生じます。
こと、ロッドレスシリンダなどの場合で、且つ、ストロークが長くて、ある程度のスピードで設定されている場合、甚大な事故になってしまう可能性は否めないです。
これは聞いた話しなのですけど、ストロークが長めのロッドレスシリンダを使っている装置で、その経路で噛みこみが発生して、ステージが動かなくなったそうです。 それで、その障害を取り除いたところ、ステージが急に動き出して、作業していた人の顔を直撃… などという。 電磁弁のスイッチが入ってしまうと、エアーを抜かない限り走ってしまうので、その辺りの配慮が必要になってきます。
反面、電動の場合では電機が遮断されると、途中で停まる、あるいは停めることができるので安全性は確保できます。
カバーの考え方。
安全性を確保する基本は、危険個所への侵入を許さないよう『カバーをつける』ことです。


機械動作時に、不用意に指や身体を入れてしまいかねない場所に関してはカバーをつけるのが有効です。
でも、やみくもにカバーをつけてしまうと、かえって、危険な状態になってしまう場合もあります。 なので、注意したいのがカバーのサイズや、そのつけ方です。
カバーの周辺に隙間がある場合には、その隙間から手や指をいれてしまうという可能性は否めないのです。 また、もしもの際に、カバーの所為で〝逃げづらく〟なって怪我になってしまうとかも。
カバーで覆ってしまうより、見えている方が安全だという考え方もあります。 そういう場合には、エリアセンサーなどのセンサーを用いるのが効果的です。
そもそも、カバーがある時点で作業スタッフ側が気をつけなければならないのですけど、そこには、人間のクセなどが関係してくる場合があるので注意が必要です。
人の特性(クセ)を知る
機械の安全性を考える時、まず、人間って、『なんか知らんけど…』 という動作をする生き物だという理解がいります。
要は、 『まさか、こんなことはしないだろう。』 とか、 『こんなことするやつおらんで。』 ってことをするのが人間だというわけなのです。 (^_^;)


魔がさす。
これについては… 〝ふと、魔がさす〟っていうこと、ご存じですか?
何の考えもなく、何気なく、ふっと… 手や指を入れてしまうとか、身体をいれてしまうとか… ってあるんですよね。 なんて言ってるボクも、実は経験者だったりします。 苦笑
それをやったらどうなるか? なんて、『常識的に』考えればすぐに理解できるのだけど、そういう時って、そこの部分が飛んでしまって、ふらっと吸い込まれるようにやってしまうんですよね。 これがその時のです。


ボクの場合、フライス盤を使って銅パイプに穴開け加工してるときにやらかしました。 ホルソーっていうノコギリの刃を円筒にした様な刃物があるんですけど、何を思ったか、穴あけしてる最中に手をだしてしまったんですよ。
繰り返し、何本も穴あけ作業している中で、『こうやってみたら~』なんていうことがふとよぎって、回転を止めずに思わず手を。 軍手してたので、軍手の毛羽が刃に巻き込まれてしまって… 『あ』も、『う』も言う間もなく、一瞬でした。 もう少し深ければ、腱までいってしまってるところでやばかったです。 __ 余談ですけど。(汗)
生産工場の中で言えば、例えば、機械上で、ワークが異常な状態になってしまった_
なんていう場合、わが身の安全を考えれば、ほっとけばいいものを、思わず… 手をいれて直そうとして、気が付いたときには事故発生…。 あるいは、指や腕をいれて、あっ!と思って、指や腕を引っ込める際にカバーにひっかけて事故を起こす… とか。 ちなみに、機械へのカバーリングを考える際にはそういう諸々の事態を想定して考える必要があるんです。
その一方でメンテナンス性も考える必要があります。 ガチガチにカバーリングしてしまって、メンテナンスに支障がでてしまうのであれば、それはそれで困ります。 また、カバーじゃなくエリアセンサーなどでの対応も同じくです。
エリアセンサーなどの場合、センサーがあることに気が付かずに、不用意に機械を停止させてしまう… ということがあります。 安全面では良好でも、それが頻発するようなら生産を考える上ではマイナスですよね。
もうひとつは、カバーの開閉を知らせるセンサー(スイッチ)などをつける際、容易にセンサーを殺す(オフにする)ことができてしまうと安全面ではよくないですよね。 カバーを付けていても『めんどくさいから』という理由で外して運用する… という事がらも人間の特性のひとつです。
人の特性を活かしたスイッチの採用
人の特性と言う面で言えば、人間って、危険な状態(緊張状態)に陥ると硬直状態になるといいます。 無意識に強張ってしまうんだそうです。
例えば、グリップ式のスイッチなどの場合、グリップを離せばスイッチが切れるので「安全だ!」と思われがちなんだけど、むしろ逆で、危険な状態に陥ってる場合にはグリップを離さず、ギュッと握りしめてしまう。 ということは、スイッチは切れずに入りっぱなし。
実は、そういう人間の反射的な特性を利用したスイッチがでています。 3ポジションなスイッチで、強く握りこむとスイッチが切れるという代物です。 (詳しくは、IDECのスイッチを参照してくださいね。)
そうそう、最近多いの自動車のアクセルに関係する事故で、パニックを起こしてブレーキを踏んでるつもりがアクセルを踏んでたっていうのも、もしかすると、人間の反射によるものなのかも。
アクセルペダルを離すとブレーキがかかるというのはあるけど、逆に、フルアクセルでエンジンが停止、もしくは減速するような構造になれば事故は起こりにくくなるのかもね。
余談: 状態表示灯の考え方
ちょっとした余談になるのですけど。
機械の状態を知らせるために、状態表示灯… つまり、シグナルタワーを設置する場合があります。 その際にも、注意が必要になんですよね。 注意というよりも、むしろ、『色』の意味合い(ルール)に対する工場側への確認です。


うちの場合では、赤、黄、緑 の3色灯を使う場合が多くて、その意味合いはこんな感じで使っています。
赤点灯(点滅): 異常(非常)停止中。
黄点灯(点滅): 資材不足などのワ―ニング(警告)。
緑点灯:正常運転中
緑点滅:自動運転可能(原点復帰完了)。
概ね、「赤」が異常とか停止の場合という認識が多いのだと思います。 が、ところによっては、赤と緑の意味合いが逆になっていることがあるので事前の確認が必要なのです。
『赤』点灯で 〝動作中〟。
ある会社さんでのルールがこれでした。
うちは、うちの普段通りに〝緑〟を正常運転中に設定していたのですけど、機械動作の確認時に、



うちは、赤が正常運転の意味なので
変更よろしくです!
って言われました。 思わず、『え!』ってなったのを覚えています。 恐らくなのですけど、その解釈として、機械側から見て「(オレは)正常運転中だから、手などを近づけると危ないぞ!」だから、気を付けて! という赤。 一方のボクらの場合では、人間側から見て、『機械は機嫌よく良好に動いてる!』という意味で、緑。
捉え方の違いですよね。
でも、こういうことって根本的な部分になってくるので、まっさきに擦り合わせておかないと混乱を招くことになります。 ホント、大事なことです。
結局。
機械の安全を考えていく上で大事なことは、そのベースな部分では機械の設計や製作時に、もろもろのことを考え、対応しておくこと… なのですけど、重要なことは、どのように〝運用〟していくか? ということも言えると思います。
考えられる最上級の策を採りいれたとしていても、機械だからこそ『万全・万能・完璧』はあり得ないんです。
機械だからこそ、それを製作した側に100%を求めたい気持ちもわからなくはないです。 でも、人間が使っていく以上のことだからこそ、どのように使っていくかという居りあいの部分が非常に大事なのだと思います。
どちらか一方の責任に頼るよりも、事故や不安全を起こさないような工夫が双方にいると思うのです。 機械側も、それを使う人側も、安全に且つ生産性を高め合うことができるのであればこの上ないですよね。
ご相談、お問合せはお気軽にどうぞ。