DX化って?
近頃は、さる方面では 「DX」 っていう言葉が盛んに叫ばれてますよね。
DXとは、デジタルトランスフォーメーションのことで、こんな感じ。 以下、生成AIによる要約です。
DX(デジタルトランスフォーメーション)とは、企業がデジタル技術を活用して業務プロセスやビジネスモデルを根本から変革する取り組みです。 DXの主な特徴は次のとおりです。
- 企業全体をデジタル化し、組織やビジネスモデルまで変革する
- 顧客視点で新しい価値を創出する
- 競争上の優位性を確立する
DXは、IT化と異なり、主に社外に向けた視点でビジネスを変革することが特徴です。IT化は情報技術(IT)を活用して業務プロセスなどを効率化することが目的で、視点は主に社内に向けられています。
DXの略語である「DX」は、英語の「Digital Transformation」の頭文字を取ったもので、「Transformation」の「Trans」が交差するという意味があるため、「X」が用いられています。頭文字をとった「DT」ではプログラミング用語とかぶってしまうため、「DX」という略語になりました。
要は、デジタル技術を駆使して、業務効率とか生産性を高めていこう! という取り組みのことです。
生産工場では?
デジタル技術をうまく使えば、業務の効率化が図れる… これはすごく頷けるポイントですよね。

生産工場のDX化っていうのは、例えば、生産における工程管理であったり、機械についてのダウンタイムの把握だったり、また、製品自体の物流管理だったり、工場全体の管理だったり… 要は、デジタルデータを使って生産管理や品質管理などを行っていくこと… なのですけど。
で、生産工場での実際のところではどうなんだろう? … なんて思うわけです。
生産工場の皆さん、DX化、進んでますか?
昔の体験。
DXという名前がこれほどまで浸透していなかった時代。 ボクが前職時代にやってきたことは、たぶん、今のDX化というのに近しいのかなって思ってます。 というか、そのまんまだったりなのかも。
システムエンジニアをしていた頃の話し。
前職、ボクは半導体工場でシステムエンジニアとして働いておりました。

ご存じの方もおられると思いますが、半導体を製造するに当たっては、その製造プロセスが多岐に渡っていて、かつ、様々な処理装置を使うわけです。 むろん、半導体製造装置というのは、メーカーも違っていて処理の仕方も違います。
要は、たくさん処理(プロセス)装置を行き来するように処理が行われて、〝半導体〟が出来上がるというわけです。 ちなみに、ボクがいた会社は半導体チップになる前のウェハでの半導体製造メーカーでした。

で、ボクが何をしてきたか? というと、半導体製造に係る業界標準の規格(SEMI規格)を使って、半導体製造装置をオンラインで制御し、装置から得られるデータをホストコンピュータへ効率的に集積させるという仕組みつくりをしていました。
オンラインでの運用を行う意義として、装置からの処理データを取得することもそうなのですけど、それ以前に大きくは、オペレータ作業の負荷軽減というのがありました。 オペレータの視点から言えば、色んな種類の装置があるため各装置の操作方法を覚える必要があります。
処理内容(レシピ)の設定を誤れば、目も当てられない損害を会社に与えてしまう可能性があるため、各装置を通じてレシピの設定方法や装置操作そのものを簡素化して、初心者なオペレータでも簡単に設定・操作できるような仕組みにするということでオンラインシステムを構築するという仕事をしていました。
オンライン運用の浸透により、例えば、製造装置のステータスを監視したり、また、処理データを使って次回の処理内容(レシピ)を効率よく設定させたり、装置の異常データを取得してメンテナンスに役立てたり… といった派生したシステムに繋げていくということもしていました。
製造現場へオンラインシステムを浸透させていく… それがなかなかたいへんで。(^_^;)
当初は、なかなかその意義を理解してもらえず、

オンライン?
オフラインの方が早いやんけ!
なんで、オンライン使わなあかんねん!
などというスタッフが続出してて… 確かに、リリース当初は不具合も多くて決して使い勝手がいいというものでもなくて… そんな風に言われるのも致し方なかったという面もあったんですが…
しかし、オンラインでの運用が部署命令、強いては会社命令でもあったので同じ部署のオンライン担当グループの連中とともに啓蒙活動を続けたんです。
懸命な普及活動の結果、しばらくすると装置管理や処理(プロセス)の分野ではオンラインによる制御が必要不可欠な状態になっていました。 データが簡単に取集できるので管理業務が捗るのとプロセスの分野では、レシピの改良などに役立てたり、また、装置管理の分野で言えばメンテナンスのスケジューリングや次回のメンテナンス作業の管理とかといったことに使えるので好評でした。
また、オペレータに対しても同じく、装置の複雑な操作方法を覚える必要がなくなるので重宝してもらえるようになったのでした。
… などということを思い返すと、そういったことが DX の走りだったのかなと。
今の仕事を始めてから…
今の仕事に就いてから、そのギャップに驚いたのを覚えています。 まぁ、ギャップは今も変わらずあるんですけども…
何か? っていうと、昔からの得意先に包装機の見積もりを出す時のこと。 打ち合わせの段で、ボクはこんなことをお伝えしたんです。
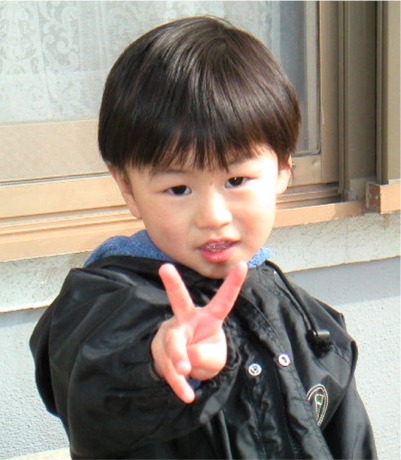
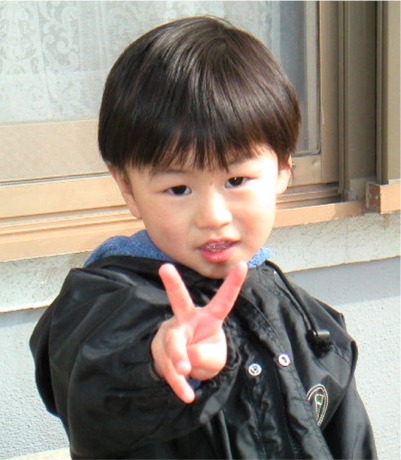
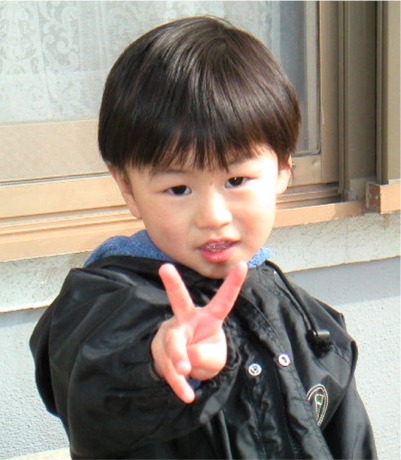
装置の異常(アラーム)履歴などをとれるようにできます。
そうしておけば、保全とかに便利ですよ!
生産数とかの管理もできますし。
すると、先方の担当者さん曰く、少々、不機嫌な口調で、



あんな! そんなもん要らんねん!
機械はちゃんと動いて、作業できたらそんでええねん。
そんなんつけて、高なるくらいやったらいらん。
それよりも、安く作ってくれたらええねん。
そんな言葉を聞いて、〝あ~、話しにならんな… 全然世界が違うわ。〟 なんてことを思ったのでした。 ちなみに、その会社さんは、業界でも、一般でも知名度が高いメーカーさんの製造部門。
まぁ、それは2000年初頭だったし、まだ、製造業でインターネットとかWebとかがあんまり浸透してない時期だったので、仕方がなかったのかもしれません。 が!
でも、Webが浸透して、DXが叫ばれるような今、現在であっても、そこはあんまりそういうことに関しては無関心みたいです。(^_^;)
生産装置・製造装置だからこそ。
概ね、「機械・装置」に対する DX って、あんまりピンと来られてないところ(人)が多い気がします。 さしずめ、根底にあるのは、
機械(装置)は、ただ処理さえしてくれればいい。 生産できたらそれでいい。
という考え方が根強くあるからなのだと思います。 語弊がでるのかもしれませんが… このことは、中小規模な工場に至ってはその傾向が強い感じです。 加えて… 穿った見方をすれば… の話しなのだけど、そういう機能を盛り込むことで、機械代金が高くなるんだったら、別にいらないんじゃないの? っていうのがあるような気もし(て)ます。
そりゃ、大手さんになれば、それなりの資金力もあるだろうし、デジタルネイティブなスタッフも大勢抱えられていることでしょうから、DXなどは率先して行われているのだと思います。 それに、大手だからこそ、DX化してないと他へのメンツが立たないという世間体の問題もあるのかも。w
けど.. 余程のプラント的な設備は別にして、いわゆる一般的な装置に関して言えば、まだまだかなと。 もっとも、ボクは半導体の世界を見てきているので、どうしてもそこと比べてしまうクセがあって。 (^_^;)
それにしても、最低限、装置異常(アラーム)のロギングとか処理数のログ機能はあって然りだと思うんですけどね。 使い方は会社さん次第にはなるんですけど、データを残すか残さないかで将来がかなり変わってくるのは間違いないんです。
ネットワークへの懸念。
DXを検討するにあたっては、ネットワークの扱いをどうするか? というのがキーになるのかもしれません。
要は、機械・装置(以下、設備)を導入した場合、それらを社内ネットワークに接続するか否か? ということ。 社内ネットワーク上に展開できれば、社内スタッフは容易に設備の状況を把握することができます。 現状で考えれば、外出先でもスマホ等で把握できるようになるというわけです。


担当者としてのトラブルの対応はもちろん、処理データなどを閲覧して、次の処理への指示をするといったことが簡単にできるようになります。
ネットワークに接続する大きな利点は、データ収集です。 特に、複数の設備を運用している場合、ネットワークを活用すればデータ集積が容易になります。 加えて、設備ごとの蓄積データを加工することで生産管理や工程管理といった管理業務も効果的に行なえるようになり、予測的な判断にも活用できます。
その一方で、ネットワークへの接続に関しては〝安全性〟に対するリスクや懸念もあります。 会社からすれば〝第三者がつくった「ワケの分からないモノ」〟をネットワークにぶら下げることになるので、安全性に関する懸念を持たれるのもうなづけます。
なので、設備はネットワークには組み入れず〝スタンドアローン(独立)〟で運用して、データはその都度、設備上にあるロギングユニット(記憶媒体)から抽出… というのが、ネットワークのセキュアを考えれば妥当なのかもしれません。 メンドクサイのですけど。(^_^;)
結局のところ…
DX、DX、DX… なんていう言葉だけが先行するかのように、独り歩きしてる感は否めないなって思ってるボクなんですけど、結局のところ、やっぱりというか、当然というか…
それを会社、もしくは工場内で推し進めるのであれば、それなりの知識をもった人材が一人以上は必要だーー と思うわけです。
一番の理想は、部署があるということ。 情報系統を扱える部署があるというのが一番の形だと思います。 部署が無理なら、グループ、もしくは、よく理解している担当がいるという環境。
選択肢として、社外に丸投げ… というのもなくはないのでしょうけど、ボクが思うにその選択は、業者からみたら〝絶好の鴨〟になるか、もしくは、それに伴って〝ある種のリスクを抱え込むか〟のどちらか、あるいは両方になってしまうのでは? とむしろ、そっちを危惧します。
ある種のリスク… というのは、例え、そこに守秘義務などの契約があるにせよ、社内の内情を外部に見せてしまうことには変わりないので、その辺りのリスクをどう考えるか? ということです。
少なくとも社内にそれなりの知識をもった担当がいないというのは、外に任せるにしても〝まっとうな〟話しができないので相手側の言いなりになってしまうという懸念がありますよね。
いずれにせよ、DX化を進めるのであれば、世間や皆がやってるからという〝流行り〟にのって進めるのではなくて、DX化をして、
どんなゴールにするか? 社内的にどう在りたいか?
といったことを、社内全体で十分に話しあって決めることが重要なのです。 生半可にやってしまうと、結局、〝使えない仕組み〟になってしまう。 (この世界のあるあるだと思います。苦笑)
そこのところ要注意ということで。
ご相談、お問合せはお気軽にどうぞ。