印字したい対象の範囲が大きい場合。
広い範囲に対応したインクジェットを使う、あるいは、数台のインクジェットを組みあわせて使えば、広い範囲への対応は可能です。 でも、インクジェットの場合ではインクや溶剤などのランニングコストの問題が生じます。
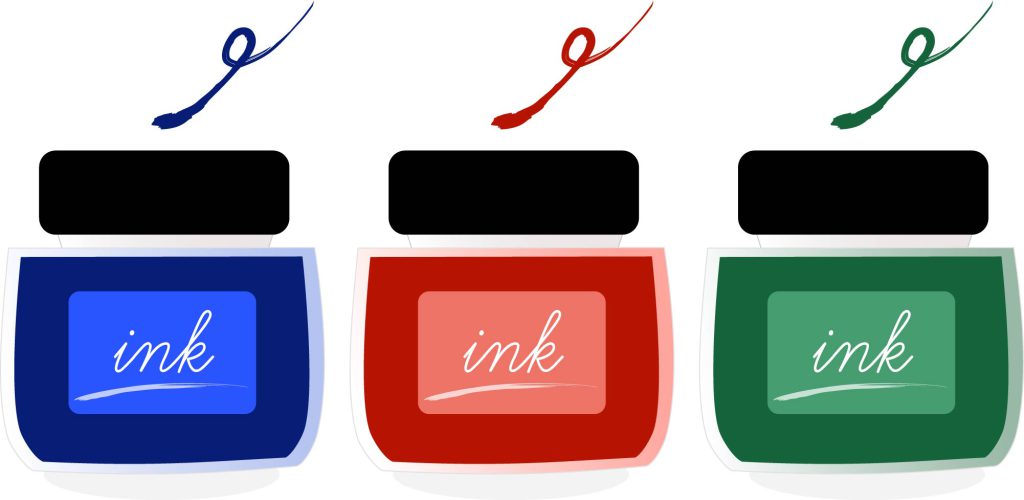
こと、広い範囲への印字ともなればインクの使用量も多くなるため、ランニングコストの問題は顕著になることが予想されます。 また、インクを使用するためインク飛散による周囲への汚れなども気になる要素となります。
そんな時に一考したいのが、〝レーザーマーカー〟を用いた印字です。
ワイドエリア対応レーザーマーカー
最近では、300x300mm以上の範囲が扱えるレーザーマーカーがリリースされています。 なので、そういった機器を利用すれば広範囲な印字に対応できます。
レーザーマーカーでの最大のメリットは、〝消耗品がいらない〟という点です。
産業用インクジェットでの場合、インクや溶剤などの消耗品が発生します。 印字する面積が広くなるとインクや溶剤の消耗も激しくなり、その分コストが嵩んできます。 それに加えて、インクジェットの場合では、ヘッドの洗浄作業といった日常的なメンテナンスが必要になります。
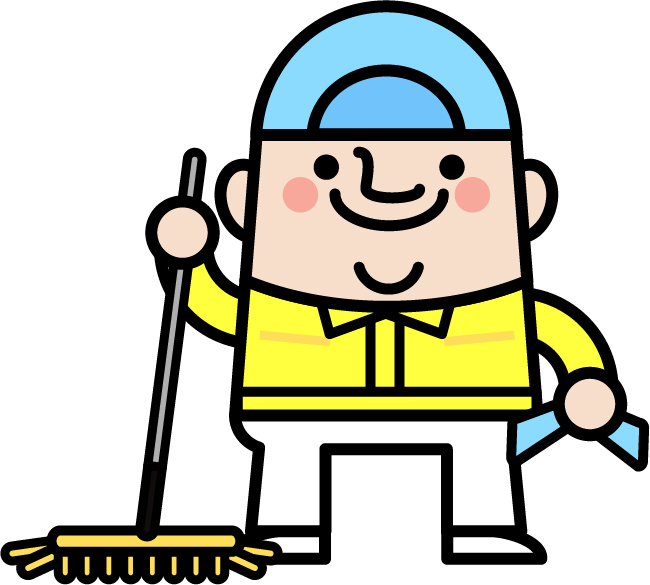
一方、レーザーマーカーの場合では、強いて消耗品として挙げるならレーザー照射時の煙を吸引する集塵機用のフィルターくらいで日常的な消耗品がありません。 メンテナンスの面でもレンズ面の清掃くらいでほぼフリーです。
また、バーコードやQRコードへの印字を考えた時、産業用インクジェットではインクの滲みや汚れで、読み取りエラーへの懸念が免れません。 しかし、レーザーマーカーでは鮮明に対応できるためそういった点でも有利です。
ただ、初期導入費用の面を考えるとレーザーマーカーは産業用インクジェットよりもハイコストになります。 ただ、消耗品や日常作業でのコストを鑑みれば、有益な投資であると言えます。
ランニングコストを抑え、且つ、広範囲に鮮明な印字を行いたいなら、絶対的にレーザーマーカーをお奨めします。
両面対応の印字装置。
本件でご依頼を受けたクライエント様からの要求は、
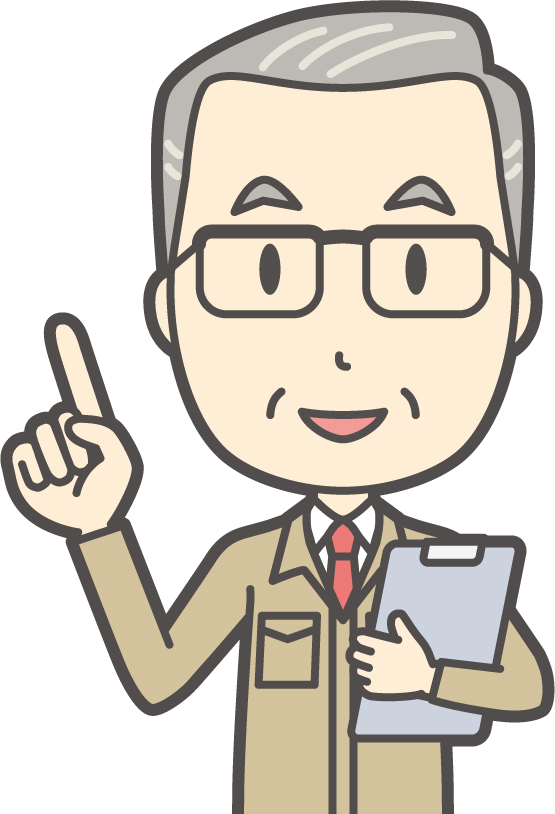
・カートンの表面に内容物の明細を記載したい。
・片面ではなく両面に印字したい。
という内容でした。
自動車やバイクのパーツを製作されている会社さんで、そのパーツを箱詰めする際にパーツの明細をカートンの表面に記載しているとのこと。 それまでは、特注した専用の印刷機械で対応されていたのが、その機械も老朽化し、また、製作したメーカーもなくなっていて、修理することもままならないとのことでの依頼でした。
それまでは、印刷のたびに〝判〟を作成し、その判で印刷するような専用の印刷機で対応していたそうです。 が、その印刷機も老朽化し、修理もままならないので、時代に応じた方法で刷新したいとのことでした。
設計における前提条件。
装置を設計するにあたって大きな制約がありました。 それは、設置場所が2階の作業場であるということです。
2階への搬入を行うにあたって、搬入用の巨大なエレベーターなり、2階部分で搬入用のハッチ(搬入口)があれば特に問題にはならなかったのですが、ここでは一切なし。
2階の窓から搬入するという方法を考えてみるも、建屋の2階部分の外側には庇(ひさし)があり、窓もそれほど大きくないため搬入口としては不向きでした。 また、仮にそこから搬入ができたとしても、ユニックを使うなど運送手段が大掛かりになり、コストがものすごく掛かってしまうことが予想されたため断念しました。
もう一つの手段として、2階の作業場へ資材を上げる際に使われている〝1m角程度〟のゴンドラがついた自社製のホイストがありました。 結局、装置を2階へ上げるには、このホイストを使う以外に手段がなく、〝ゴンドラに載せれるサイズ〟が設計条件になったのでした。
両面印字への考察。
要求事項である〝両面印字への対応〟を考えた場合、表面に印字した後、裏返して印字するという方法が考えられます。 しかし、この方法では反転させる機構が必要になり、機体が大掛かりになってしまう可能性がありました。
搬入経路の問題から〝ゴンドラに載せることができるサイズ〟であることが大前提であるため、その条件をクリアしつつ、両面対応できる方法を考える必要がありました。
そこで思いついたのが、〝カートンを立てて搬送させる〟という方法です。 〝立てる〟ことで、同時に両面への印字が可能になります。 ただ、問題は、どうやって立たせるか? ということ。
シリンダなどを駆使すれば立てることはできるのでしょうけど、そうなると機械的に複雑になってしまい、装置サイズにも影響が生じます。 できる限り、シンプルな機構で立たせることができないだろうか…
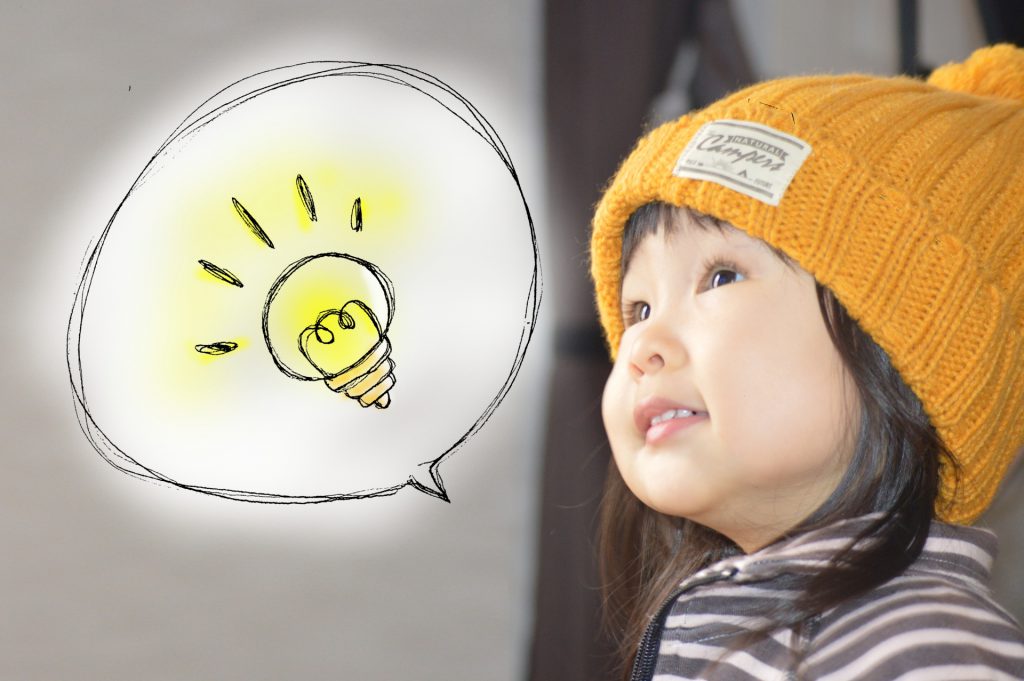
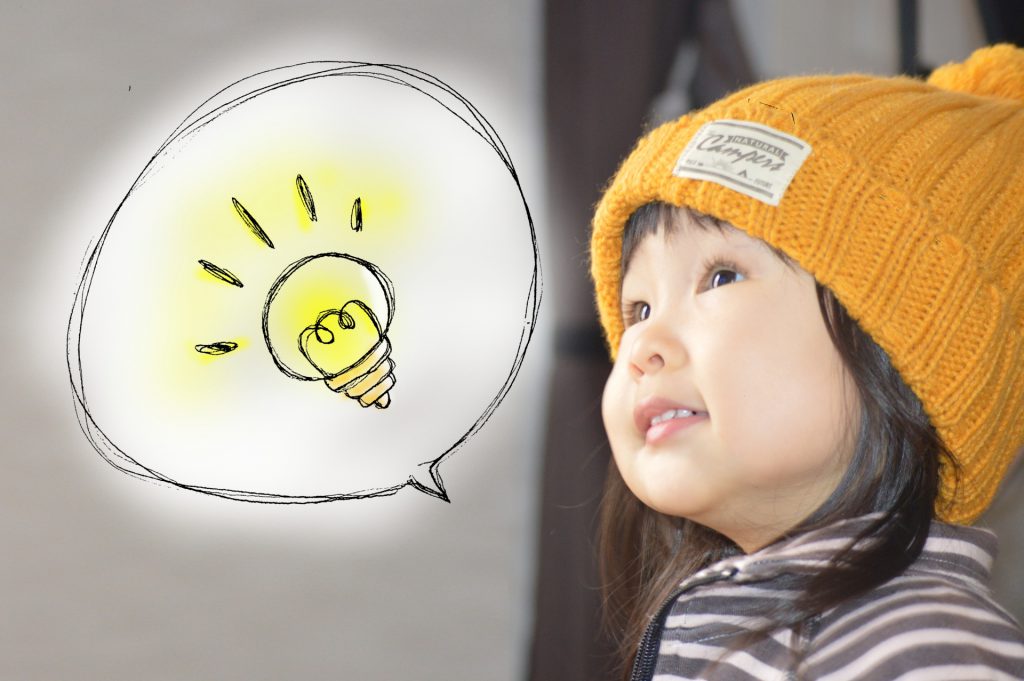
と、ようやくできたのがこちらの装置です。 装置もコンパクトに設計することができ、無事に搬入ができました。
カートンへの両面印字を行う装置。
分割できる設計で、ゴンドラへの対策としました。
カートンを自動供給することで、作業効率を上げる設計にしています。 また、カートンの供給部には〝スペア〟を搭載し、補充時のタイムロスの軽減を図っています。
印字内容の登録はレーザーマーカー側のコントローラで行います。 本装置での操作は枚数のセットだけです。 起動ボタンを押せば、カートンの自動供給が始まり、設定された内容の印字が行われます。 セットした枚数に達すると、処理が終了します。
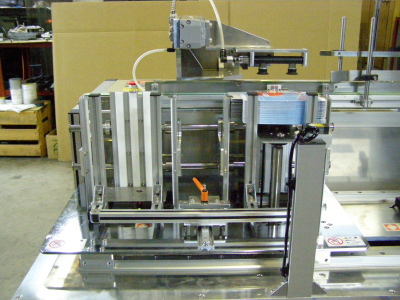
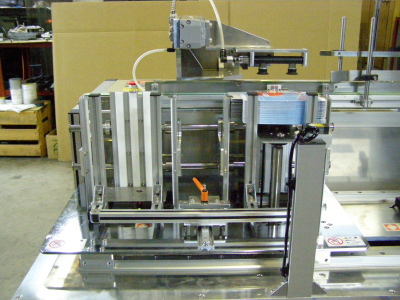
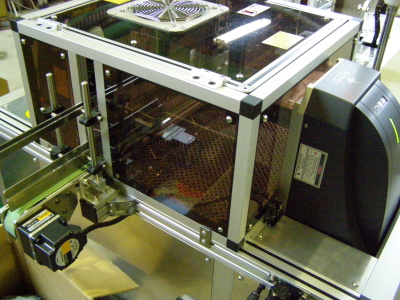
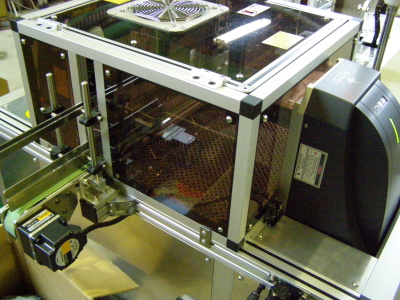
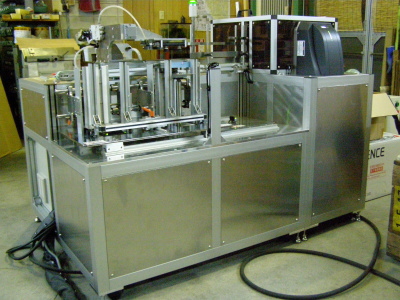
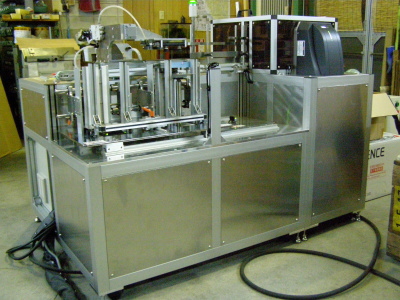
動画で。
動作を動画でご覧ください。
レーザーマーカー使用時の注意事項。
レーザーマーカーで印字を行う際の注意点は、『換気』です。
レーザーでの印字は、対象物表面のインクをレーザー光線で焼き飛ばすことで実現しています。 このため、インクが焼かれる臭いと粉じんが発生します。
こと、インクが焼かれる際には、レーザーの照射熱とインク上の化学物質が反応してガスが発生する場合があります。 臭いに関しては独特の臭いになるため、それに過敏なスタッフがいる場合には、注意と配慮が必要です。
それが酷い場合には、じん肺などへの影響も免れないので、集塵機を設置するなど、環境への対策を十分に考えられるのがベターです。 また、集塵機のフィルターはこまめに清掃するよう心がけてくださいね。
ご相談、お問合せはお気軽にどうぞ。
※ 自社専門サイト〝マーキングコトはじめ〟より転載・リライト。