レーザーマーカーによる印字の特性をご存知ですか?
めざせ、100人! ってことで、Youtube やっているのですが、なんと! お陰様で100人突破しました! これもひとえに、皆さまのお陰です。 次は1000人目指してコツコツ。 できればチャンネル登録お願いします!
さて、今日のテーマは…
レーザーマーカーの印字特性。
レーザーマーカーの印字の特性って、ご存知でしたか?
その最大の特性は、
不 滅
であること。 不滅とは『消せない』ということです。 つまりこれは、〝改ざんされにくい〟ということを意味しています。 この点、改ざんの危険性が想定される箇所への印字にはレーザーマーカーによる印字が有効であるということです。
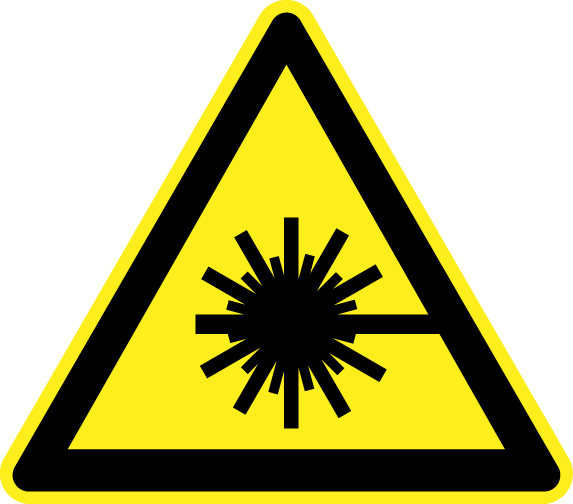
そして、もうひとつの特性が印字の鮮明さです。
インクを用いる産業用インクジェットでは、インクのにじみやカスレなどで印字時の不鮮明さが問題になることがあります。 また、インクジェットの種類によってはインクのドット(粒)により印字を行うため、ドットの欠けにより誤読を誘発しやすいという問題も抱えています。 例えば、『8』が『B』に見えたり『1』が『7』に見えたりするなどといった状態がそれです。
一方、レーザーマーカーによる印字では〝ライン〟による印字になるため、インクジェットに比べてより鮮明に行うことができます。 不滅で鮮明な印字ができる性能を考えると、レーザーマーカーは製薬業界に向いていると言えます。
なぜかと言えば、製薬業界では誤読されてしまう状況は許されず、また、印字情報を改ざんされないことが条件であるためです。
ワンタッチカートンを自動供給してレーザーマーキングする装置。
かなり前の事例になりますが…
某製薬会社からの依頼でリリースしたワンタッチカートンに対応した装置の事例です。 ワンタッチカートンを自動供給して、レーザーマーカーにて印字を行う装置です。 印字後は、文字検査を行っています。
ワンタッチカートンは非常に扱いづらく、か・な・り 苦労しました。
取扱いに難あり。
ワンタッチカートンとは、糊りやテープを用いることなく簡単に底面が形成できるカートンのことです。 〝ワンタッチ〟で組み立て可能なので、〝ワンタッチカートン〟と呼ばれていて、最近はこの利便性より広く用いられています。 (下に参考画像を貼っておきます。)
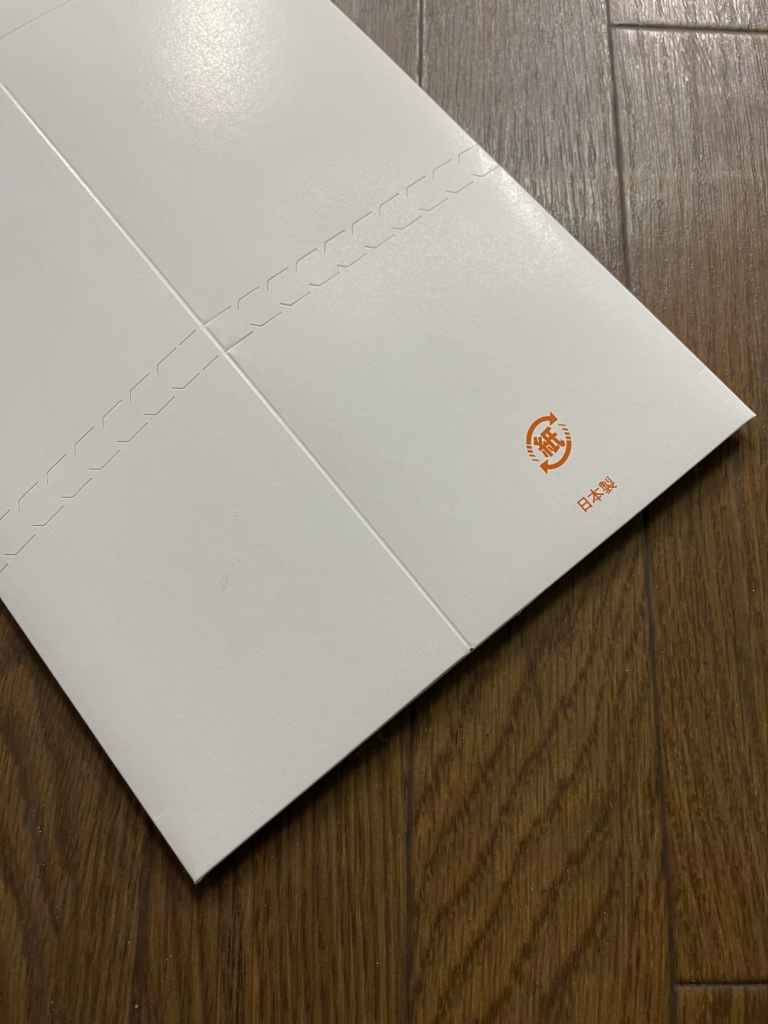
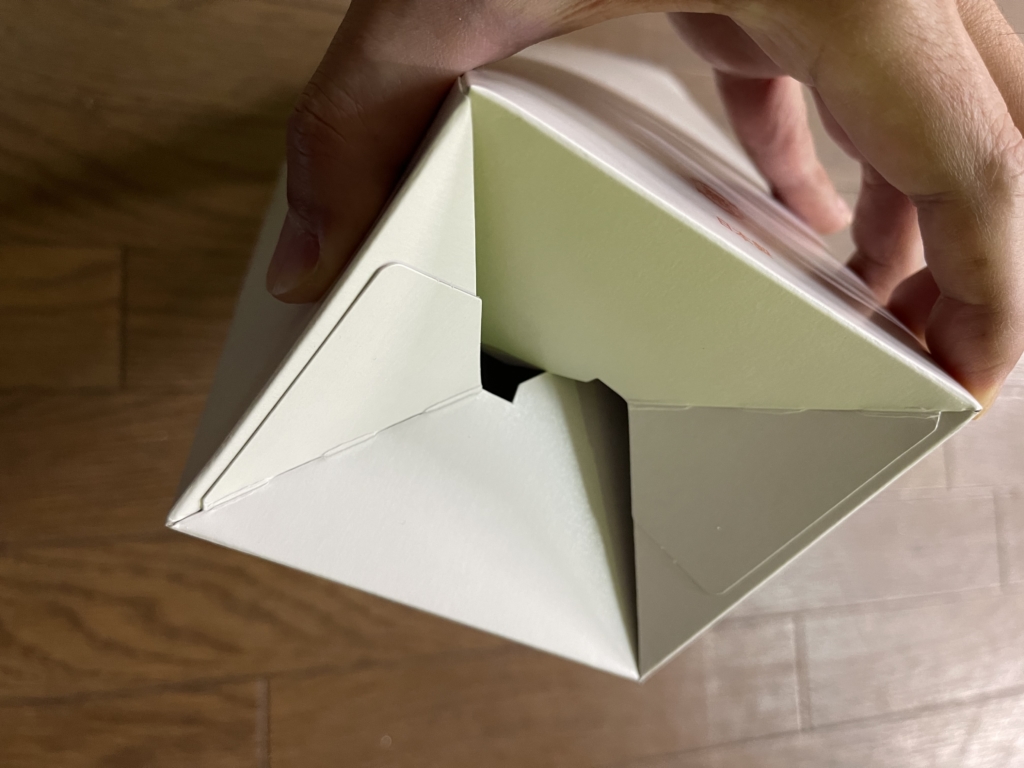
ワンタッチカートンでは、ワンタッチでの箱の組み立てを実現するために底の部分が他の部分に比べてかなり分厚くなっています。 この厚みは、1、2枚積み重ねただけでは特に目立たず、あまり問題がないように思えるのですが、枚数を積み重ねると顕著に現われてきます。
打ち合わせ当初、ワンタッチカートンのサンプルを1~2枚預かり、それで設計を開始しました。
2枚程度だと綺麗に積み重なるので、『簡単に積める!』という判断をしました。 ところが… カートンの束を預かり、それらを積み重ねてみて初めて認識の甘さに気づかされたのです。(滝汗)
底部分の厚みが累積して、綺麗に積み重ねることができないということが判明しました。
機械化を考える場合、積み重ねたときの〝姿勢〟が問題になります。 平たい板を立てて並べた時と同じように〝行儀よく〟重ねられると思っていたため、不測の事態に陥りました。 マガジンにセットした際に姿勢が全く安定しないのです。
製作も終盤になりつつある中で発覚したので、急きょ設計変更を加えながら、なんとか仕上げました。 この件では、お陰様でものすごく勉強させてもらいました。 ノウハウと経験と教訓を積んだので、ばっちりです!
出来上がった装置。
印字対象となる箱のサイズは、巾100mm~300mmぐらいの範囲で、且つ、その巾寸法に応じて高さも変わってくるため、対応するには か・な・り 苦労しました…
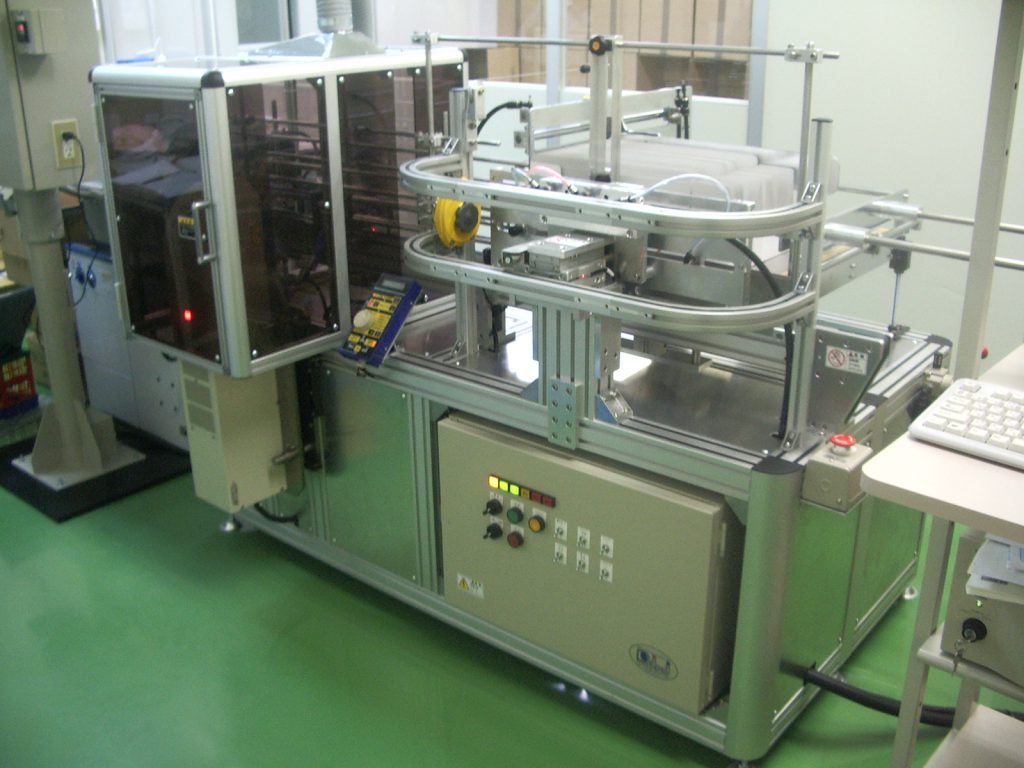
動画で。
余談:バリデーションについて。
医薬・医療系の分野に装置等の設備を納入する場合、「バリデーション」という作業が必要になってきます。 バリデーションとは、簡単に言えば、納入した機械設備に対して検査・試験・評価を行って、その一連の工程が信頼すべきものかどうかを検証する作業です。
結局、めちゃくちゃ簡単にいうと、『こんな評価確認をしたので、これで大丈夫です』という結果を書面としてまとめるいうことです。
この装置でもバリデーションが必要だったのですが、その対応は本案件の元請けで文字検査部分の担当であった会社さんでの実施となりました。
うちでも、バリデーションへの対応は可能です。 が、バリデーションには相応の労力が必要になるため、別途見積もりによる対応とさせて頂いております。
ご相談、お問合せはお気軽にどうぞ。