あなたの工場では段ボール箱やカートンケースを使っていますか?
めざせ、100人! ってことで、Youtube やっているのですが、なんと! お陰様で100人突破しました! これもひとえに、皆さまのお陰です。 次は1000人目指してコツコツ。 できればチャンネル登録お願いします!
さて、今日のテーマは
段ボールのコストダウン。
冒頭の件、もし使われているのなら、普段、どれくらいの量を使っていますか?
ご周知のことだと思いますが、生産工場では、段ボールやカートンケースのことを〝(包装の)副資材〟と呼んでいます。
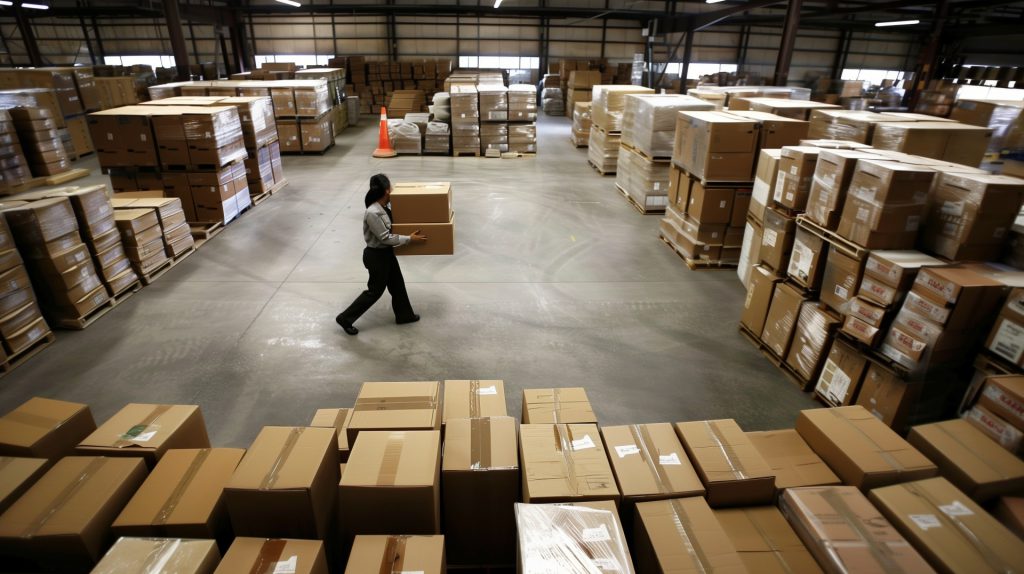
副資材は、概ね、商品を円滑に流通させる手段として使用され、販売に直接作用するような位置づけではありません。 一般的に段ボールは輸送時の外箱用途で用いられ、カートンケースは製品の小分け用途で外箱に対する内箱として用いられています。
言い換えると、商品が店頭に並ぶ前までの〝つなぎ〟的な位置づけであって、少し乱暴な言い方になるかもしれませんが捨てられる要素がつよい資材であるとも言えます。 そういった副資材に対してでさえ〝意匠的なこだわり〟がある場合は別なのですが、特にないのであれば簡単にコストダウンを図ることができます。
もっとも、『コストダウン』と言えば、資材メーカーに納入単価を無理やり下げさせるようなイメージを持たれる方も多いかもしれません。 でも、違います!
メーカーを叩いて単価を下げさせるのは最悪で卑劣な方法です。 実は、資材メーカーに強要することなく納入単価を下げてもらう方法があるんです。
単価を下げるアプローチ。
まず、副資材にはどんなコストが係っているのか? その種類を知っておけば削減も行いやすくなります。 というわけで、整理してみましょう。 ユーザー(使用者)側の目線で考えると、副資材には下記のようなコストが係っています。
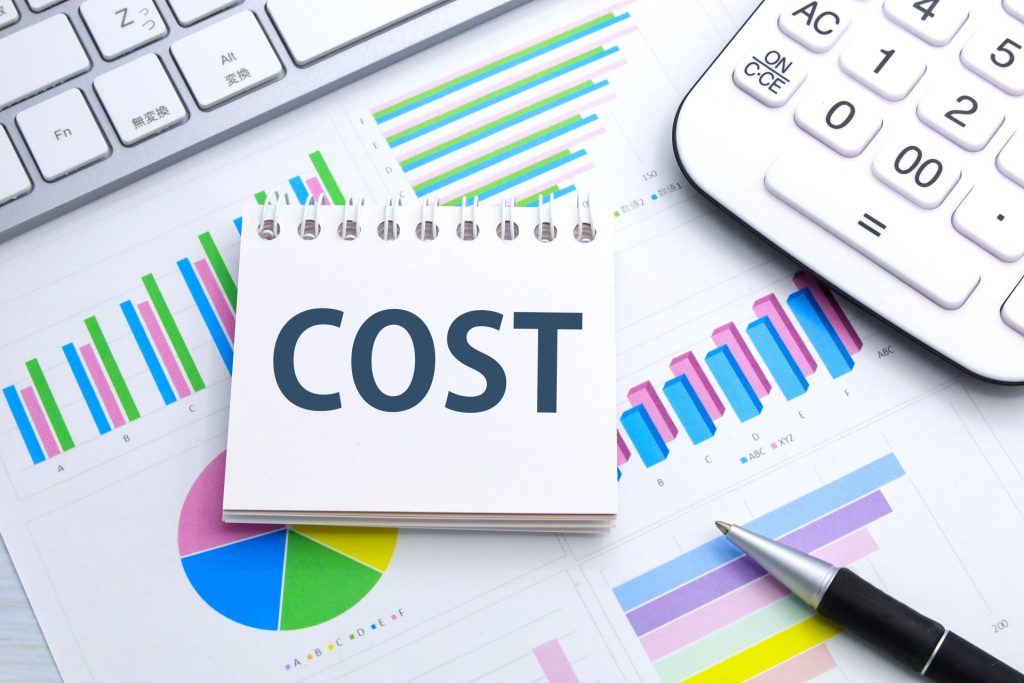
資材そのもののコスト(仕入れ)
副資材の仕入れに係るコストです。 ナンボ(幾ら)で購入しているか? ということで一番目に留まりやすいコストですよね。
ちなみに、資材メーカー側で捉えると、副資材を制作する際の材料費、デザイン・設計や実際に制作する際のコスト、管理や流通にかかる諸経費、作業スタッフの人件費、利益マージンなどを加味した価格がユーザーへの売価になります。
仕入れ後の管理コスト
仕入れし、工場へ入荷した後、サイズや品種に応じた区分で工場内で維持・管理しておくためのコストです。 区分が多ければ多いほど、管理場所が広く必要になり管理コストにも影響を及ぼします。 また、副資材と言えども、野ざらしに置いておくわけにはいかないので、空調等それなりの空間が必要になるため、電気代なども加味すべき要素になります。
作業に係るコスト
例えば、管理場所から実作業に渡すための時間や、資材そのものの扱いやすさなど、副資材を取り扱う上での作業全般に係るコストです。
なにを削減するか?
コストの種類がわかった上で、では、なにを削減すればいいのか?
先にお伝えしたように仕入れコストについては削減すべきではありません。 削減すべきでないというと御幣が生じるかもしませんが、ここで言いたいのは、高圧的にさげるべきではないということです。
もっとも、取引先の資材メーカーと信頼関係があり、多少の価格交渉ができるのであればやってみる価値はあるのかもしれません。 が、仕入れコストでのアプローチでは別の問題を誘発してしまう可能性があります。 これは例えば、副資材を制作する際の材料グレードの低下や制作工程の省略といった副資材そのものの品質が危ぶまれる可能性があるということです。
前述で考えれば、〝管理コスト〟についてが一番目に見えないコスト、つまり、『支払っているという実感がわきにくいコスト』であると言えます。 また、それは〝作業コスト〟についても同じくです。
両者については、それに対して、直接、お金を支払っているわけではなく〝間接的に支払っている〟という状態であり、間接的だから、そこにコストが係っているという実感(認識)がわいてこないのです。
仕入れた資材を『何気なく』保管し、その保管場所から『何気なく』運び出し、作業する。 実は、この一連の行為にこそ、コストダウンへの糸口があります。 この〝何気なく〟の部分にアプローチすることで副資材のコストを大きく下げることができます。
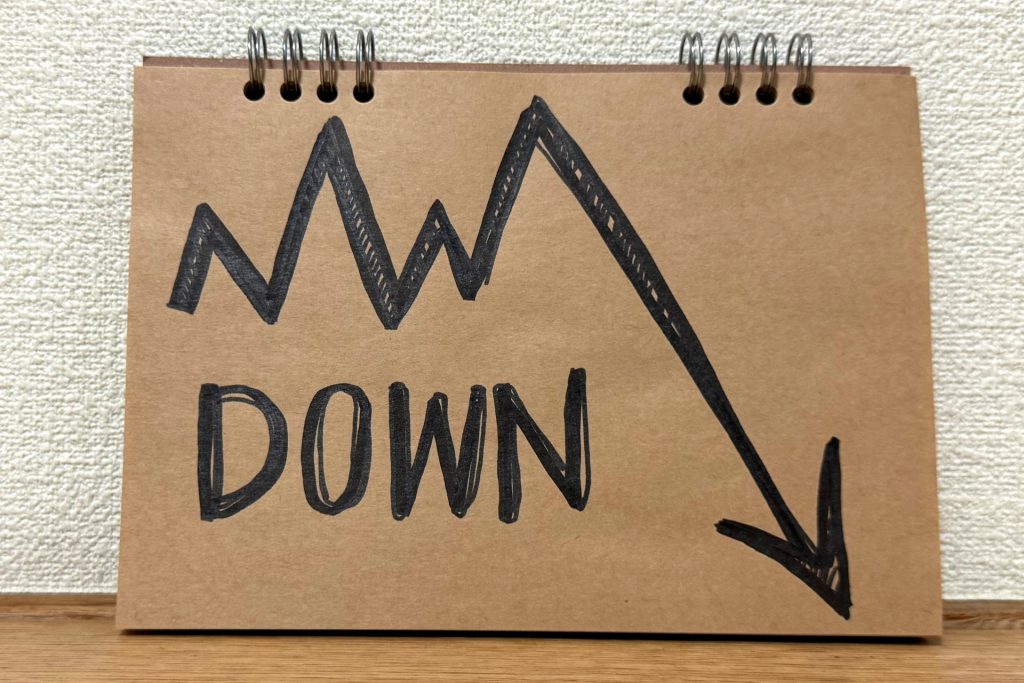
現状の資材に着目。
まず、最初にお伝えした『資材メーカーに強要することなく納入単価を下げてもらう』ということを考えてみます。
注目すべきは、資材メーカーでも、ユーザー側と同じように管理コストや作業コストが係っているという点です。 ではなぜ、これが資材メーカー側でも発生するのか? と言うと、その起因がユーザー側にあるからです。
ユーザー側でオーダーした〝品種〟や〝サイズ〟は、当然、資材メーカー側での管理対象となります。 オーダー通りに〝品種〟〝サイズ〟を制作し、それぞれが混じらないように区分けして管理していく… それが〝資材単価〟へ反映されるというわけです。 また、品種やサイズの区分が多くなれば、その分、制作にも影響が生じます。
品種への対応に関して言えば、印刷の工程が大きく関係します。
印刷工程では、その品種に応じた〝判〟が必要になります。 この時、当然、判に対する品種毎の保管はもちろん、使用時の付け替え、使用後の洗浄作業などといった〝判への管理作業〟が発生します。 それらの管理作業もまた、制作時の諸経費として計上されるのです。 なお、これらの作業は制作するサイズが同じであったとしても、品種が変れば必ず発生します。
コスト削減への対応策。
結局のところ、資材メーカー側での管理や作業に係るコストが削減できれば、制作単価のダウンにつながる可能性があるということなので、結論から言えば、〝品種〟や〝サイズ〟に分けてオーダーするという方法を止めてしまえばいい… ということになります。
コストダウンを図る上でのキーポイントを考えてみると、資材メーカーでの品種への対応を鑑みれば、印刷工程での〝判〟への手間の削減がその対象になると言えます。
〝プレ印刷〟を改める。
ユーザー側が指示した内容を資材メーカー側で予め印刷することを〝プレ印刷〟と呼んでいます。
例えば、ある製品ラインナップ〝A、B、C〟を考えたとき、予め、A、B、Cを箱に印刷しておくということが『プレ印刷』です。 コストダウンを図る方法の一つとして、こういった【プレ印刷をやめる】ことを挙げます。
具体的に言えば、品種による個別での情報の扱いをやめ、自社名などの品種を通じて共通化できる情報のみをプレ印刷で実施するという方法です。
プレ印刷する内容がサイズを通じて共通化できれば、資材メーカー側では、必然的に共通の判が使えるようになるためコストダウンが図れるようになります。 また、ユーザー側ではサイズごとの管理で済むようになり、保管場所の削減やそれに係る作業の簡略化につなげることができます。
つまり、ユーザー側では、納入単価はもちろんのこと、管理や作業コストなどを含め、全体のコストダウンに繋げることができるというわけです。 ただし、外箱・内箱に関わらず〝意匠的なこだわり〟があるのであれば、残念ながら、このアプローチは成立しません。 何か別の方法を考える必要があります。
プレ印刷しない箇所への対策。
プレ印刷しない項目については、社内で対応するということになります。
最近では、段ボール箱などの外箱用途への大文字対応のインクジェットが各社からリリースされています。 そういった器材を用いて、プレ印刷しない項目へ対応します。
インクジェットを使って印字を行う際には、2つのパターンが考えられます。 1つは、製品など内容物を入れ『箱の状態』にしてから印字を行う方法。 もう一つが、箱の状態にする前の〝シート状〟の状態の時に印字を行うという方法です。
組み立てられた『箱の状態』に印字を行う場合、印字面には下の図のような制約が発生します。
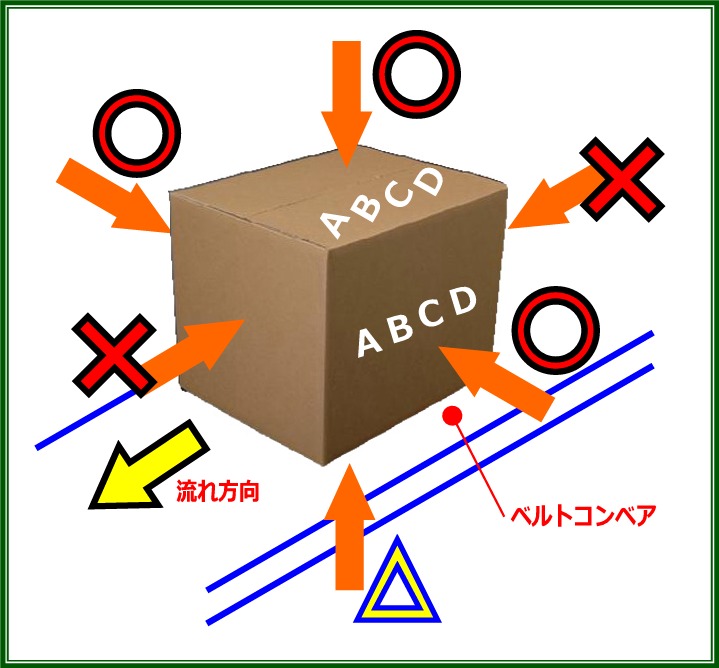
スムーズに直角反転させるコンベア
搬送方向に対して垂直になる面(上図でxの面)に印字が必要な場合は、何かしらの工夫が必要になります。 が! その場合には便利なコンベアがありますので、安心してください!
シート状態での対応。
箱の周囲に印字を行うのであれば、箱の状態にする前に印字を行うのがベストです。 段ボールを箱に組み立てる前のシート状の状態なら、任意の面へ簡単に印字を行うことができます。(下の図参照)
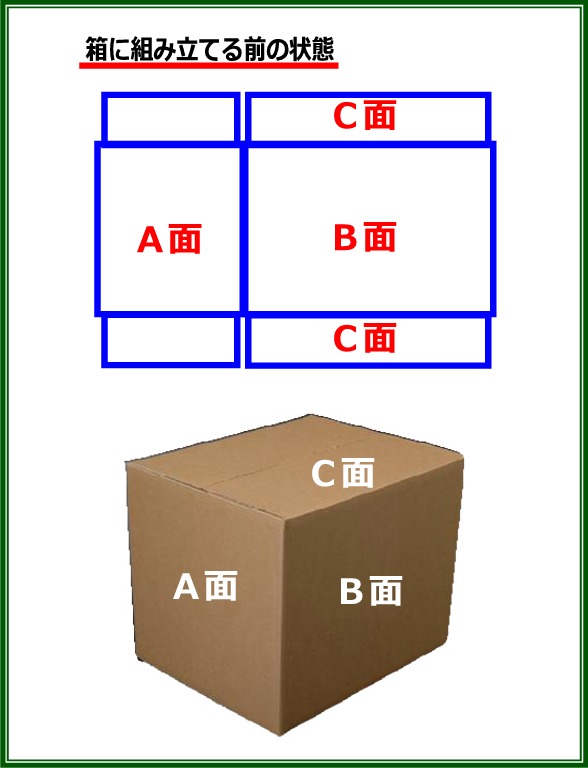
シート状態での対応に適した器材があります。
ご相談、お問合せはお気軽にどうぞ。