グリップコンベアって、ご存知ですか? 実は、選び方を間違えると〝大損〟してしまうんです。
めざせ、100人! ってことで、Youtube やっているのですが、なんと! お陰様で100人突破しました! これもひとえに、皆さまのお陰です。 次は1000人目指してコツコツ。 できればチャンネル登録お願いします!
さて、今日のテーマは…
底面印字やコンベア間の乗り継ぎ用途で。
恐らく、大多数の方がグリップコンベアを知らないと思うので、まず、説明しますね。
実は、この話題、ずいぶん前のアメブロにも書いてるのですけど、そこからのリライトです。
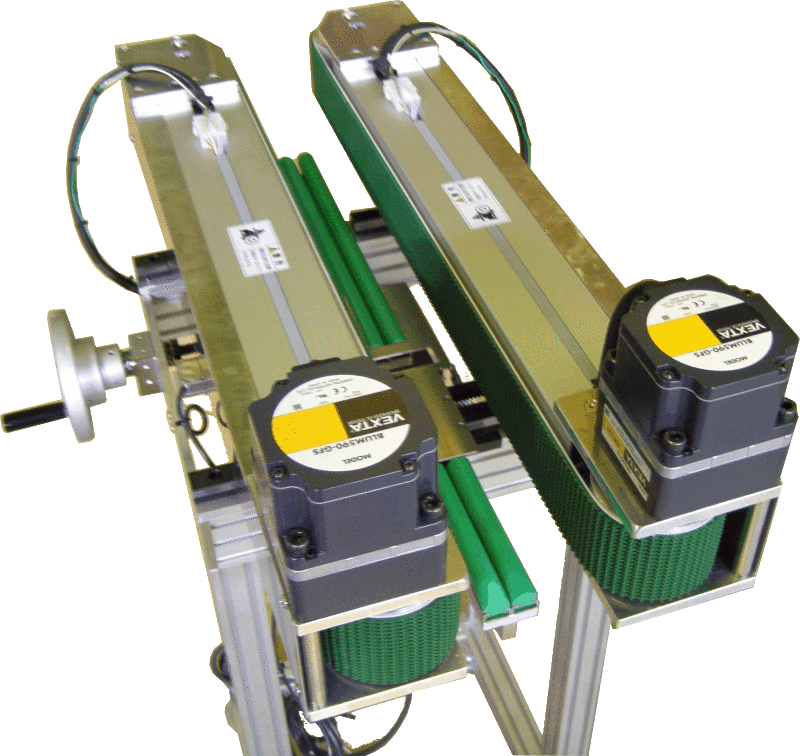
現在、アメブロは放置状態です。w ちなみに、ボクのブログ歴は実は長いんです。笑
さて、本題です。
グリップコンベアって、なに?
一般的に、ベルトコンベアはベルトの〝上に〟ものを置いて運ぶような構造をしています。 こんなイメージ。
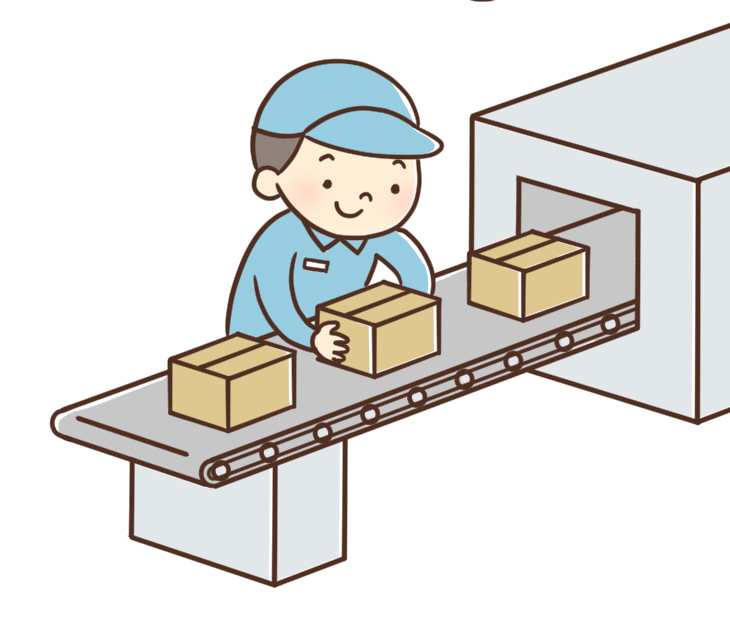
でも、グリップコンベアは違っていて、その名の通り、『モノを挟んで』運ぶという構造をしています。 どうやって挟んで運ぶかというと、簡単に言えば、ベルトを垂直に立てた状態のコンベアを並列に配置して、その間にモノを挟んで(グリップして)運ぶんです。 ちなみに、抱き込みコンベアと言う方もおられるようです。
用途としては、産業用インクジェットプリンタなどを使ってボトルなどの容器の底面に印字を行う場合や、コンベアAからBへの乗り継ぎが不安定になる場合の橋渡しといった用途などに使われています。
乗り継ぎについてをもう少し具体的に言うと、例えば、下の図のような場合を想定したとき、瓶類などのような品物の場合では乗り継ぎ時に傾倒してしまう可能性があります。 こと、ガラス製の瓶などの場合は倒れてしまうと割れてしまうことがありますので取扱いには注意が必要です。
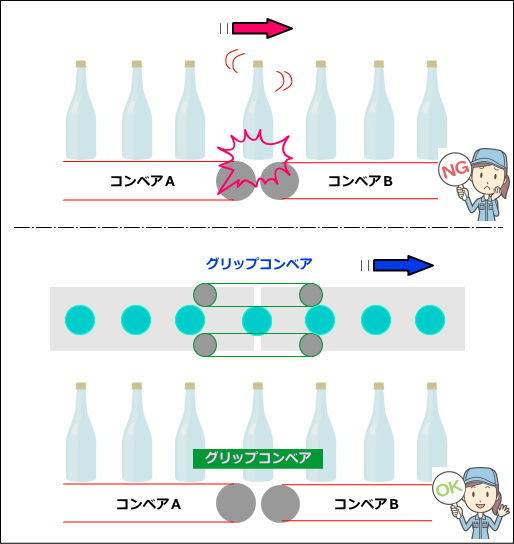
グリップコンベアを使えば〝ホールド〟して搬送させることができるので、倒れてしまうリスクを抑えた安定したラインを構築することができます。
実物。
実物は、こんな感じです。
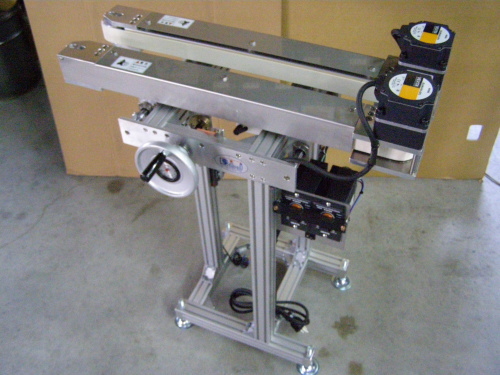
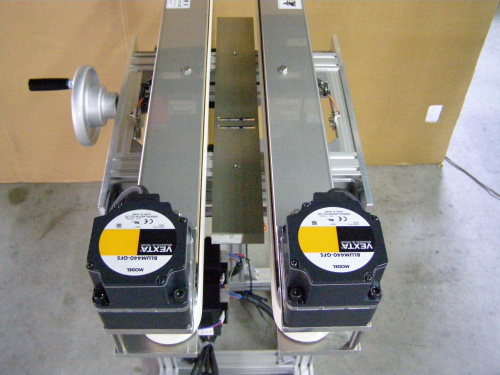
構造的なこと。
グリップコンベアを扱う上で一番気にすべきことは、『2本のベルトの同期性』です。
どういうことか? というと、ベルトとベルトで挟んでモノを運ぶため、〝2本のベルトスピードを同じに保つ必要がある〟ということなのです。 ベルトのスピードを同じにすることで、安定した搬送が可能になります。
ではなぜ、同じスピードにする必要があるのか?
というと、それぞれのベルトのスピードが合わない場合、例えば、円筒形のワークなどではベルトのスピードの差でワーク自体が回転してしまうのです。 産業用インクジェットでの印字を考えた場合、この現象は文字が歪んでしまうなどの問題を招いてしまい、致命的になりえます。
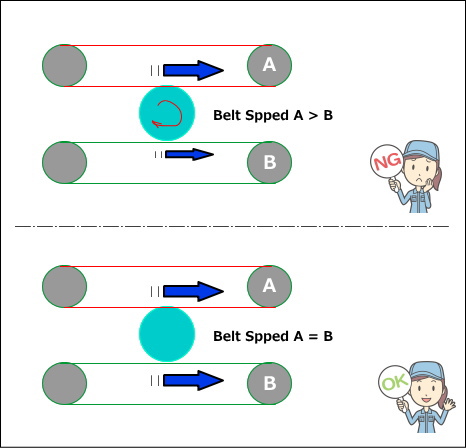
過去の苦い体験。
実は… 過去に、ベルトのスピードが揃わないという問題に直面したことがあります。(汗)
初めて製作したグリップコンベアでその問題は起きました。 正直なことを言うと、その当時はコンベアに対する知識があまりなく、深く考えずに設計してしまったのです。 予算との兼ね合いもあって、その時は『廉価な』インダクションモータ(いわゆる、汎用のモーター)を使って、グリップコンベアを作りました。
構造的な〝みかけ〟は大丈夫そう… だったのですが、いざ起動してみると…
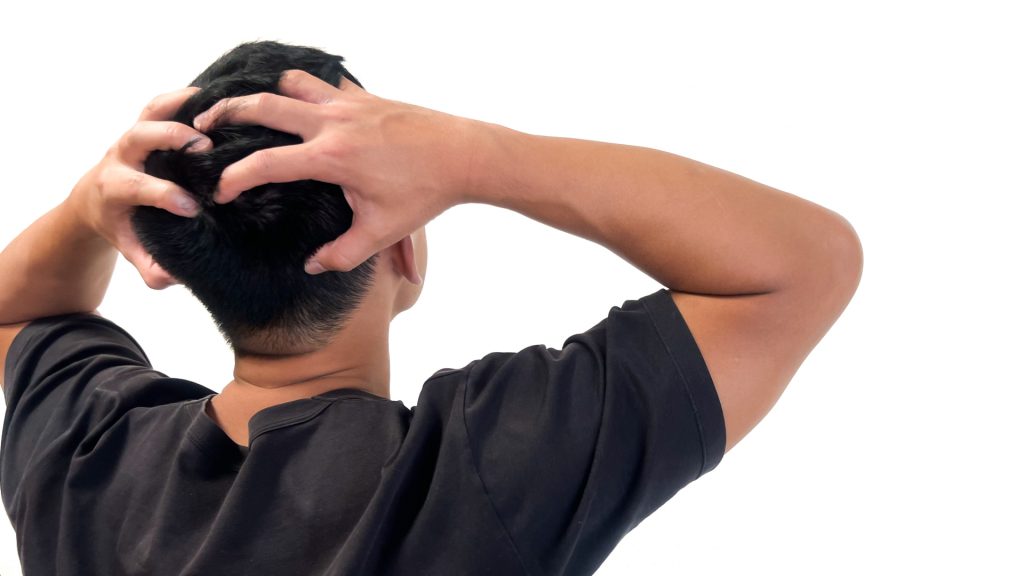
〝あっ!!!〟
・・たいへんな事態が発生…
モーターのスピコン(スピードコントローラ)で2台のモーターのスピードを合わせるも、合わないのです。
スピコンをちょっといじるだけでスピードがすぐにズレて、『揃った!』と思っても、徐々に合わなくなってきたり… モーターってスピードが揃うものだと思ってただけに、すごくショックでした。 どうしよう… って、頭が真っ白になりましたよ。 まぁ、なんとかスピードを揃えることができ、客先へ納めることはできましたけど…
スピード問題を克服して、ばっちり!
調べて見ると、そもそも、インダクションモーターは『単体』での使用向けに作られていて、スピード等には個体差があるとのこと。 機械の中で独立した機構や用途で用いる場合には支障はないのだけど、同期・同調をとるような動きには向いていない… って…。 この体験で、ものすごく勉強させてもらいました。
価格的なリーズナブルさの面を思うと、インダクションモーターは魅力があるのですけど、使い勝手な面でいうと全くリーズナブルさを感じれないのがわかりました。 なので、この教訓からグリップコンベアへのインダクションモーターの採用は却下。
以降は、〝ブラシレスDCモーター〟という性能の良いモーターを採用してます。 このモータは、2台並べた際のスピードの同期性の他に、トルク性能にも優れているという優れものです。 しかも、インダクションモータに比べると、効率もよく、使用電力も低くて、ECO!なのです。
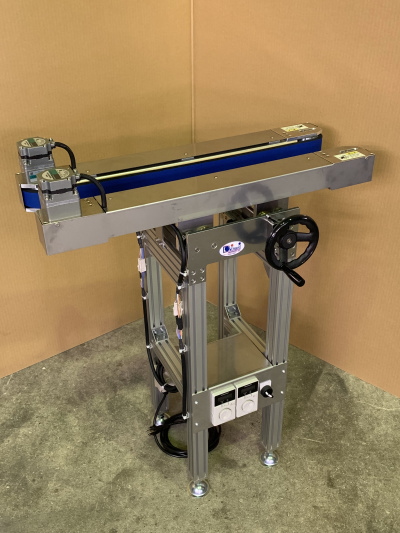
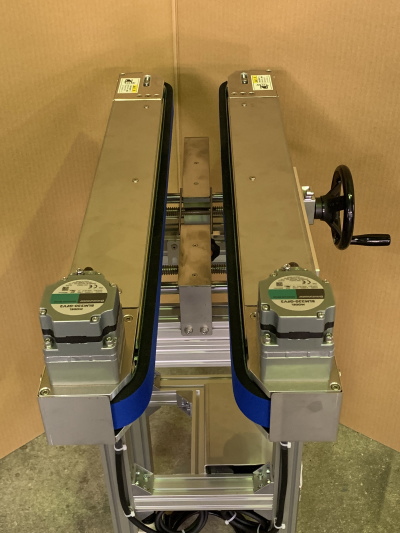
そうそう、言い忘れていましたが… インダクションモーターはトルクに脈動が起きる場合があるのです。 一般的なベルトコンベアなどの用途では特に問題はなく、また、搬送距離が短い場合にはそれほど問題にはならないのですけど、搬送にシビアさがいる場合には注意が必要であるということです。
他所さんのことを言うつもりはないのですが、製作コストを抑えるために未だにインダクションモーター(汎用モーター)で製作されているところもあるようです。 もしも、それを選んでしまった場合には、注意しながら使ってくださいね。
特筆すべき、その外のこと。
ベルトスピードを合わせるということの他に、注意すべきポイントがあります。 そのポイントとは、〝ベルトの脱落〟についてのことです。 これは、場合によっては、ものすごく重要でかつ、重大な事柄になりえます。
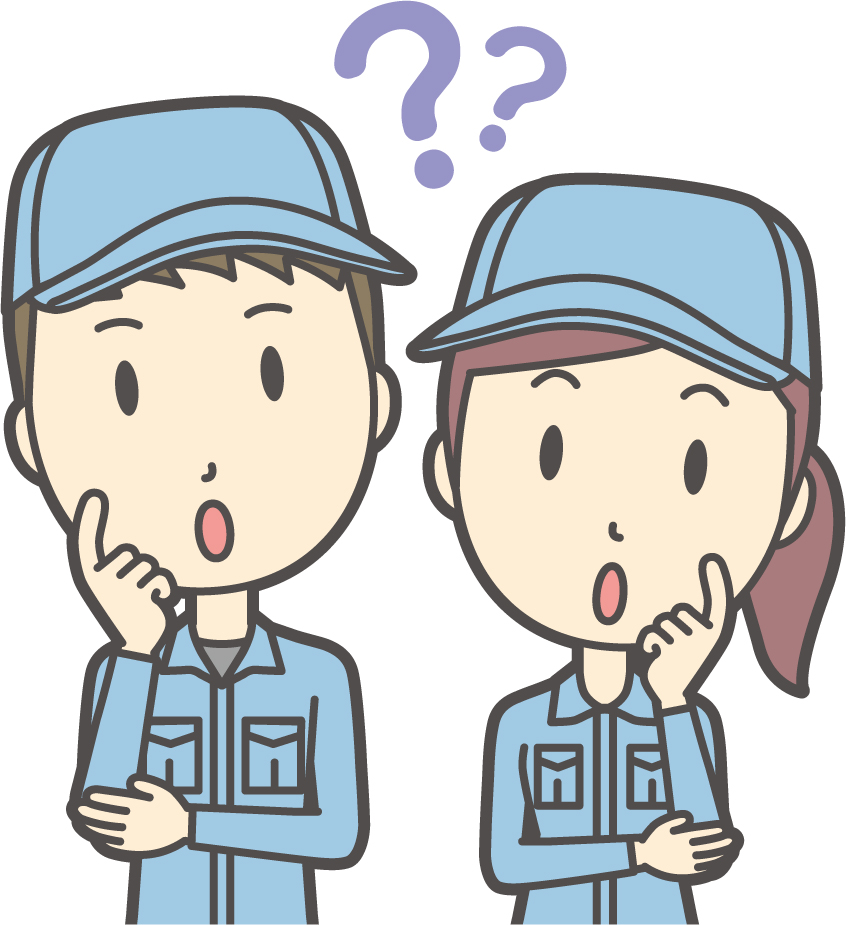
ベルトの脱落??
って、ピンっ とこないかもしれませんが、ベルトの脱落とは、プーリー(ローラの方がわかりやすい?)からベルトが外れてしまうことを言います。 グリップコンベアでは、その構造上、ベルトの脱落が起きる可能性があります。
グリップコンベアでは、ベルトを縦向きで使います。 この時、ベルトはプーリー間のテンション(張力)によって、一定の位置に保たれ、支えられています。 しかし、そもそも、縦向きに使うということ自体、プーリーから外れやすい体勢であるということは否めないのです。
ベルト脱落のメカニズム。
コンベアのベルトは、常に一定の『位置』で走行しているわけではありません。 少なからず、揺らぎながら(蛇行)しながら走行しています。 一定に見えるのは、常に安定する方向への復元力が働いているためです。 この時、ベルトに負荷がかからず、ただ走行しているだけなら特に問題は生じません。 しかし、コンベアとはモノを運ぶためにあります。
グリップコンベアでは、ワークをグリップした瞬間にベルトには負荷がかかり『安定状態がなくなる』という状態が生まれます。 脱落が起きてしまうという現象が起きるのは、この時なのです。
負荷がかかったとしても、ベルトが復元できる範囲であれば脱落は起きません。 しかし、その範囲を超えてしまうと、ベルトの脱落というトラブルが発生してしまうのです。
ベルトの脱落を防ぐ。
ベルトの脱落が発生してしまうと、当然、グリップコンベアとして使用できなくなります。 仮に、グリップコンベアが生産ラインの中で使用されているのであれば、ラインがストップするという事態が発生し、当然、生産に支障がでてしまいます。
最悪の場合では、搬送しているモノへ損傷を与えてしまうといった結果を招いてしまいます。 加えて、その復旧のためには相応の時間を要することなるため、作業時間に対するロスも免れなくなってしまいます。 毎回、脱落のトラブルが発生してしまうともなれば、被害は甚大です。
では、それをどうやって防ぐか?
そのポイントが『ベルトの裏側の構造』です。 これは一つの方法なのですが、うちの場合では、ベルトの裏側に必ず〝桟〟をつけて、脱落防止としています。 桟をつけることで、桟が障壁となって脱落しにくくなるという考えです。
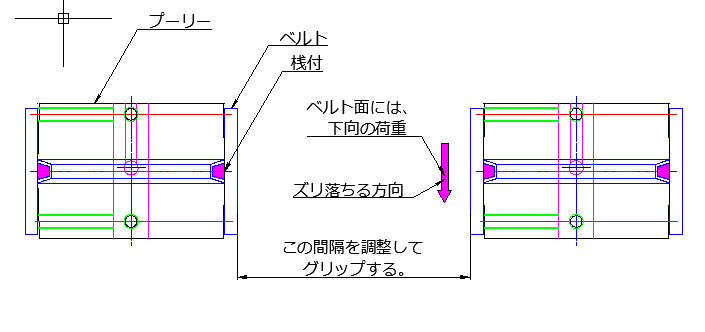
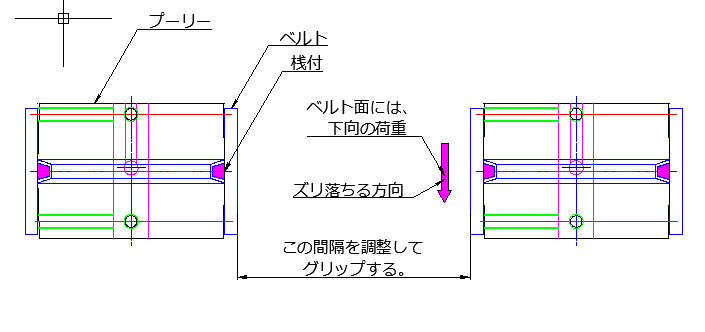
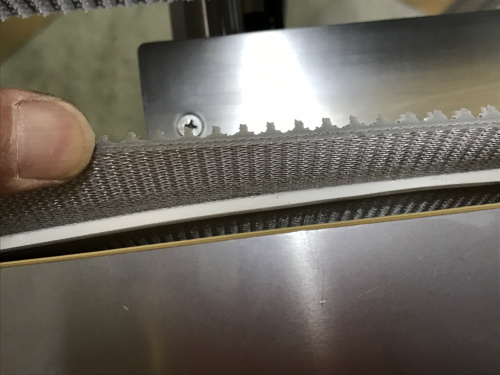
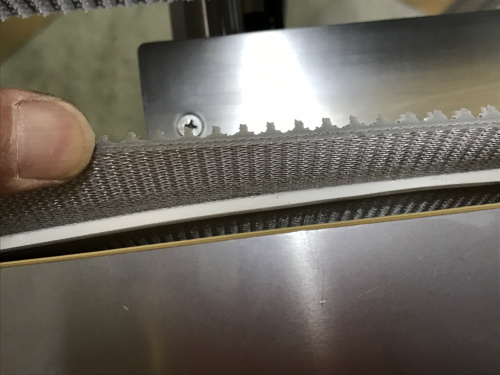
ベルトの脱落対策はあまり加味されていない模様…
とはいうものの… ボクが知る限り、ベルトの脱落についての対策はあまりされていないようです。
対策が加味されない理由は、コストに関わるからと思われます。
当然のことながら、裏桟をつけない方が製作コストは安く抑えることができます。 ベルトに裏桟をつける場合、プーリーやフレームに桟を逃がすための構造が必要になり、部品代や製作コストそのものが上がってしまうのです。 結局、それは売価にも影響してきます。 製作費を抑えるために、そういった対応を除外しているというわけです。
グリップコンベアは、概ね、容器の底面への印字で使われる場合が多く、また、その対応はインクジェットメーカーからの提案でもたらされることがほとんどです。 一部の営業マンの中には 『安くしないと採用してもらえない』 という考え方が(根強く)あり、こういった対応を施すことでコンベア自体の価格が上がってしまう懸念から、未対応で安価なグリップコmンベアを推し進めることもあるようです。
グリップコンベアを導入するユーザー側の知識や認識が甘いと、運用を開始してから思わぬトラブルに巻き込まれてしまうという事態に繋がりかねません。 実際、ベルトの脱落によることでのトラブルも何度か聞いたことがあります。
初期導入費用を抑え安価に導入できたとして、その後の作業に支障を来すのであれば、もっとコストアップになってしまいます。
グリップ時の衝撃に備える。
あと、グリップコンベアを製作していく中で気が付いたことがあります。 それは、グリップ時の衝撃です。
ベルトの間隔の調整は、対象となるワークをベルトの間に挟めて手動ハンドルを使って行います。 実際に搬送させて、その具合を確かめながら、グリップの力加減を調整するという感じになります。 グリップが緩すぎると搬送時にワークが落ちてしまう、また、強すぎるとワークにダメージを与えてしまうようになってしまうので、感覚的な要素が強いのです。
ともあれ、ワークを挟み込む際には、瞬間的にコンベアのフレームに力が加わります。
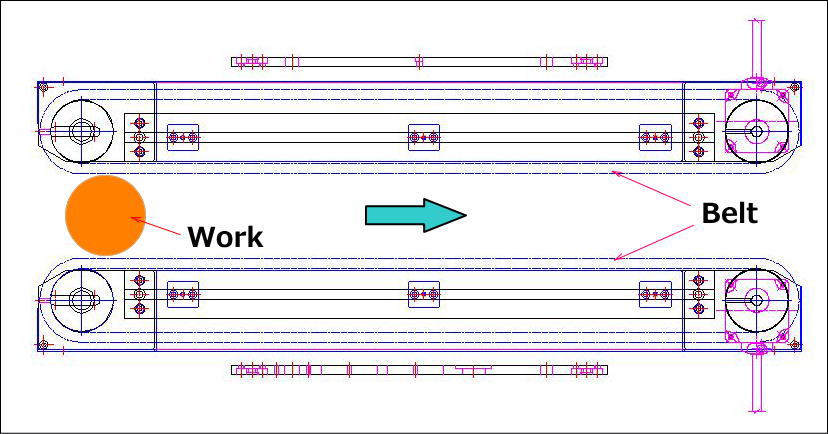
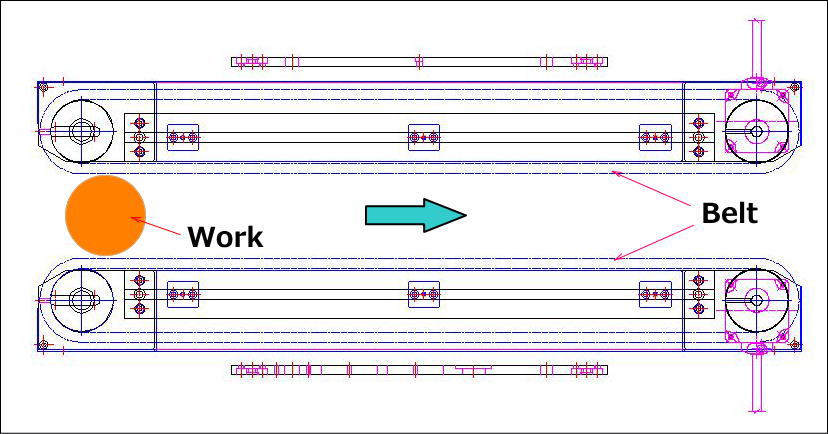
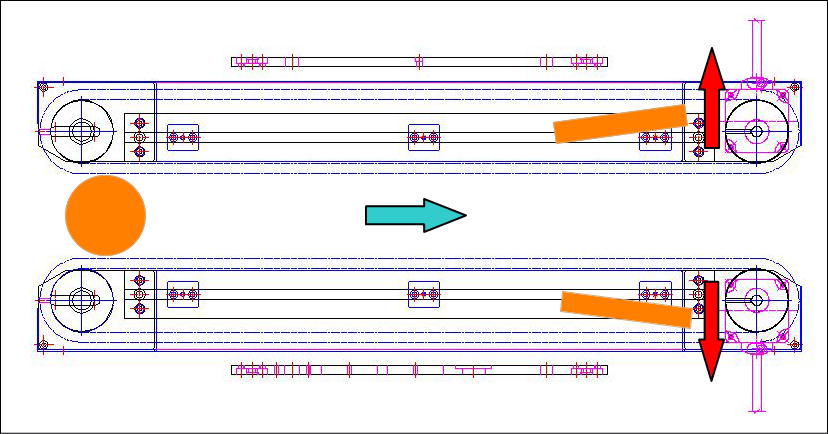
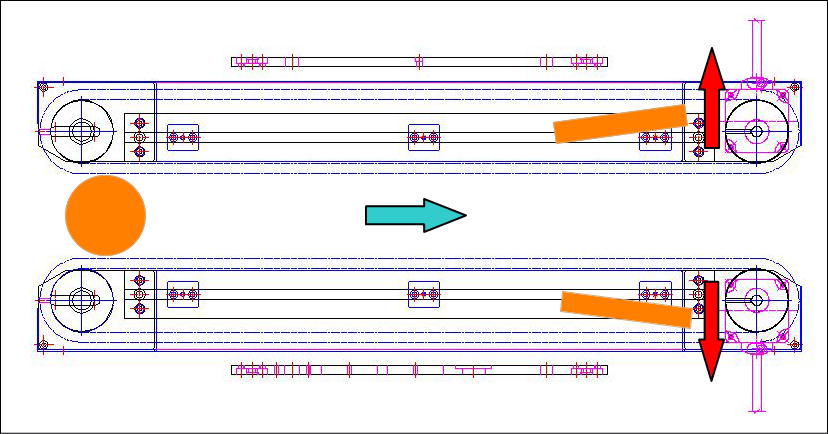
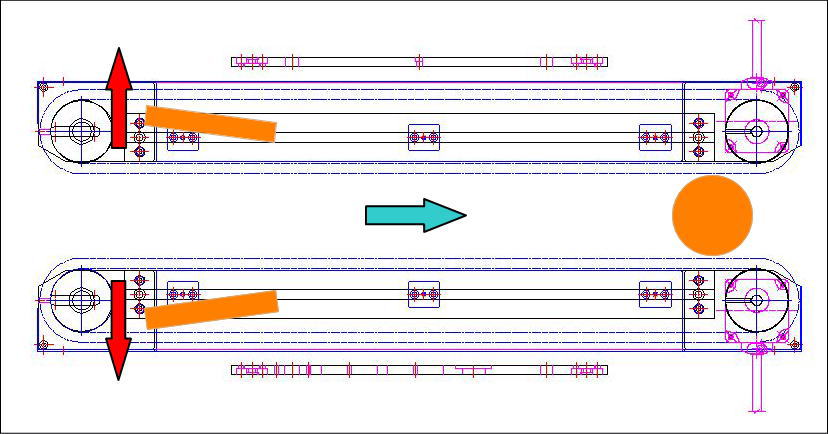
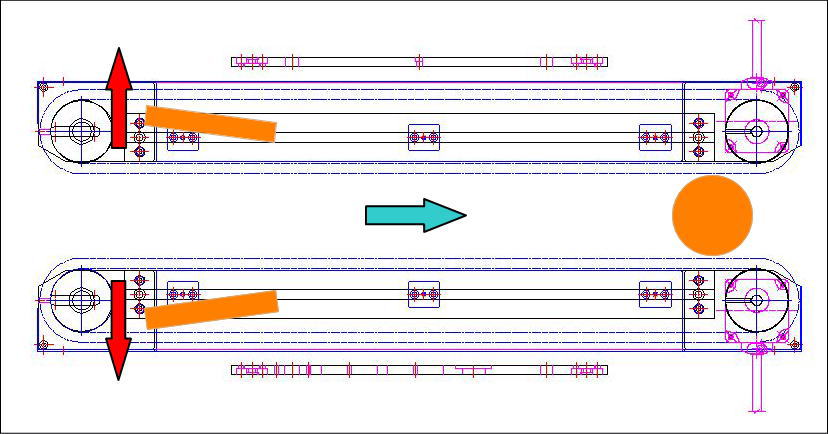
挟み込んだ瞬間に、下流側のフレームが開く格好になり、通り過ぎる瞬間に元に戻るような作用が生まれる… という感じです。(図参照)
それが原因となって搬送に影響を及ぼす場合があるということがわかりました。 印字用途で用いる場合、印字に影響が生じる可能性があると判断して、うちではそれなりの対策を講じています。
価格だけで決めるのは危険!
グリップコンベアを選ぶ際に、もうひとつ注意すべきことがあります。 それは価格での判断です。 端的に言えば、『価格だけで決めるな』ということなのです。
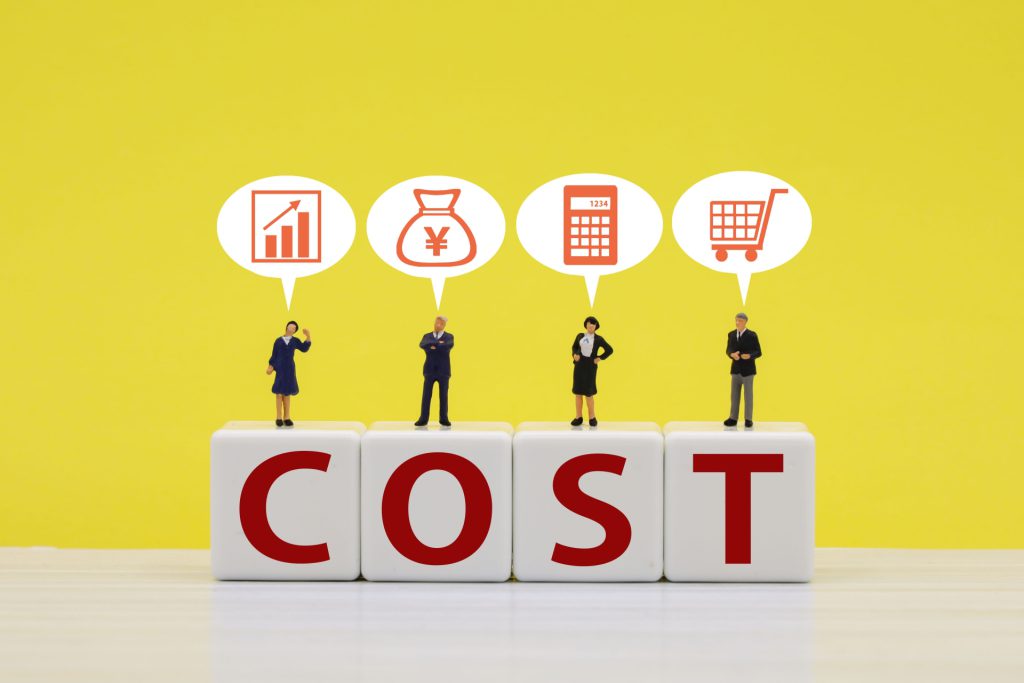
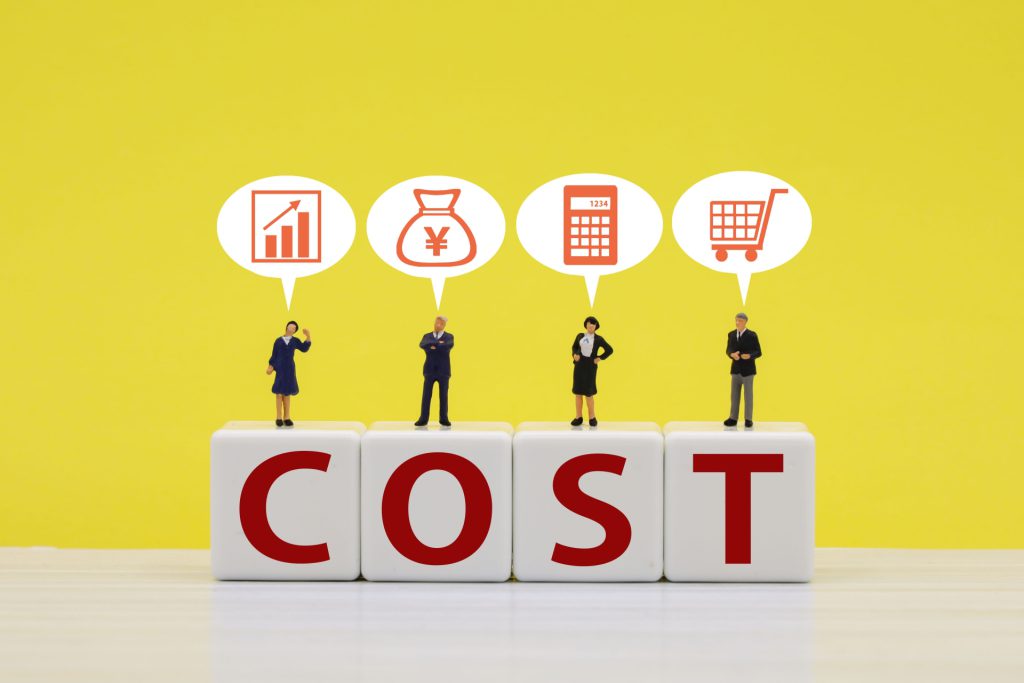
上記に挙げたモーターやベルトの脱落といった内容は、グリップコンベアの製作コストに影響を与える要素です。 なので、現物を見て購入することができるのであれば、そういった点を確認することでトラブルへの回避は可能です。
でも、実は、価格面に影響を与える〝見落とされがちな〟要素がもうひとつあるんです。 それは、グリップコンベアの搬送能力です。
気にしたい、搬送能力!
搬送能力とは、
搬送区間(機長)内で搬送できる総重量のこと。
です。 どういうことかというと、
例えば、グリップコンベアの機長が800mmで『搬送能力:1kg』とした場合、800mmの中で運べる総重量が1kgということになります。 注意したいのは、あくまで総重量だということです。
もう少し具体的に言うと… 1本300gのボトルを搬送させることを考えた場合、3本なら『3本x300g=総重量:900g』。 1kg以下になるので許容範囲OK。 しかし、4本となれば、総重量は1.2kgとなり、1kgを越えることになるのでNGとなる… というわけです。
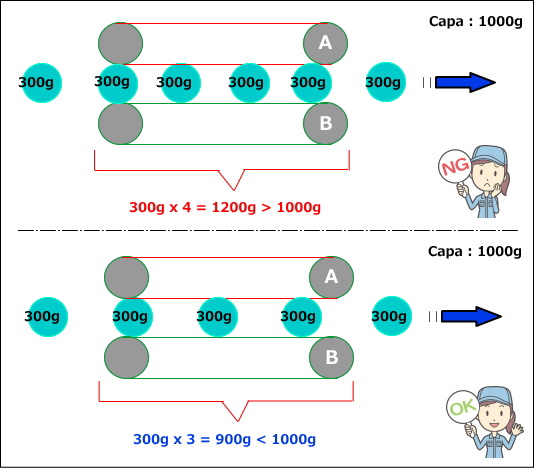
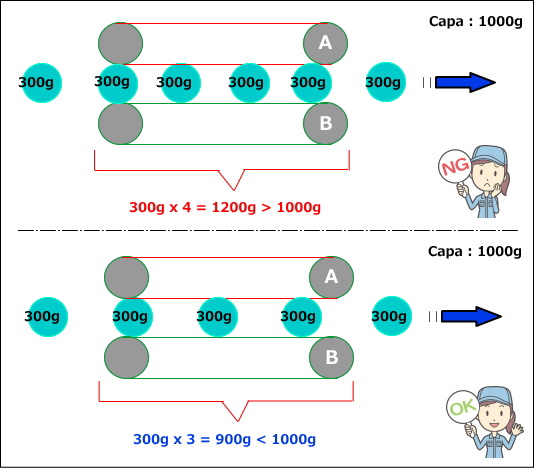
1本1kgの商品だとすれば、その1本が流れ切るまで、次の物が投入できないということです。
ボクの知る限り、グリップコンベアに関するトラブルの多くは『性能への過小見積もり』である場合が多いのかなと思っています。 搬送能力が低いなら、その分、モーターの容量(スペック)も低くで済みます。 つまり、安くできるというわけです。
それに加えて、使用時への申し伝えが曖昧であるという点です。 きちんと伝えていれば、問題は起きないはずなのですが、しっかり伝えてしまうと〝価格〟に影響が生じてしまうので、曖昧にしてしまう…
なので、安易に価格だけで判断してしまうと期待していたような運用ができない… という事態を招いてしまうのです。
参考:動画でどうぞ。
グリップコンベアの動画です。 ご参考に。
まとめ。
〝安価なグリップコンベアを購入して対応することが悪い〟と言ってるのではありません。 気を付けてほしいのは、
安さには、それなりの理由がある
ということなのです。
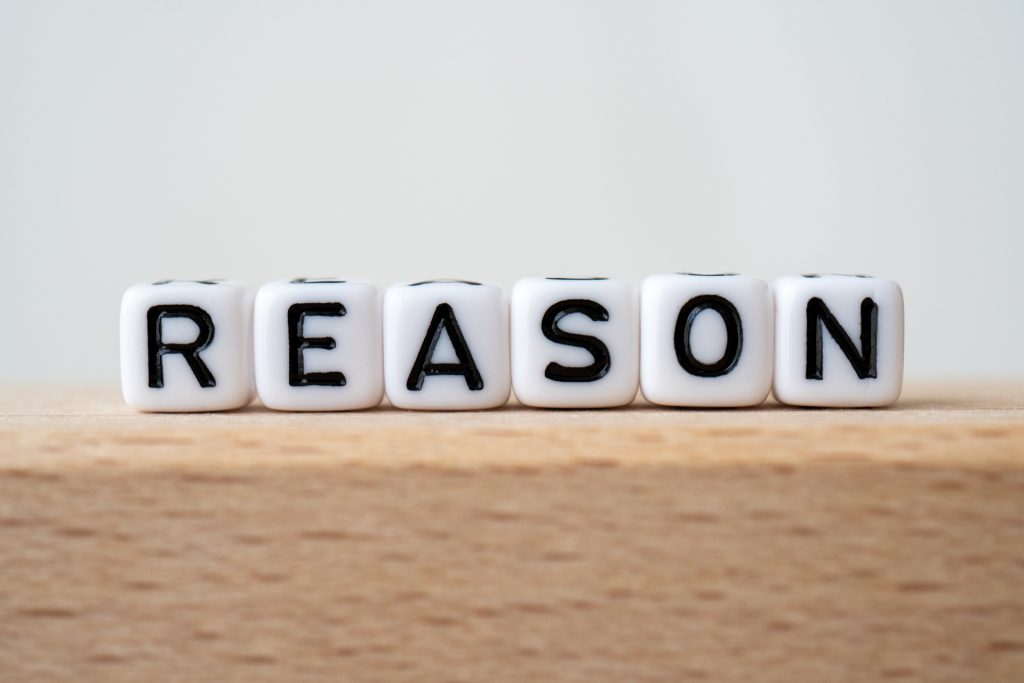
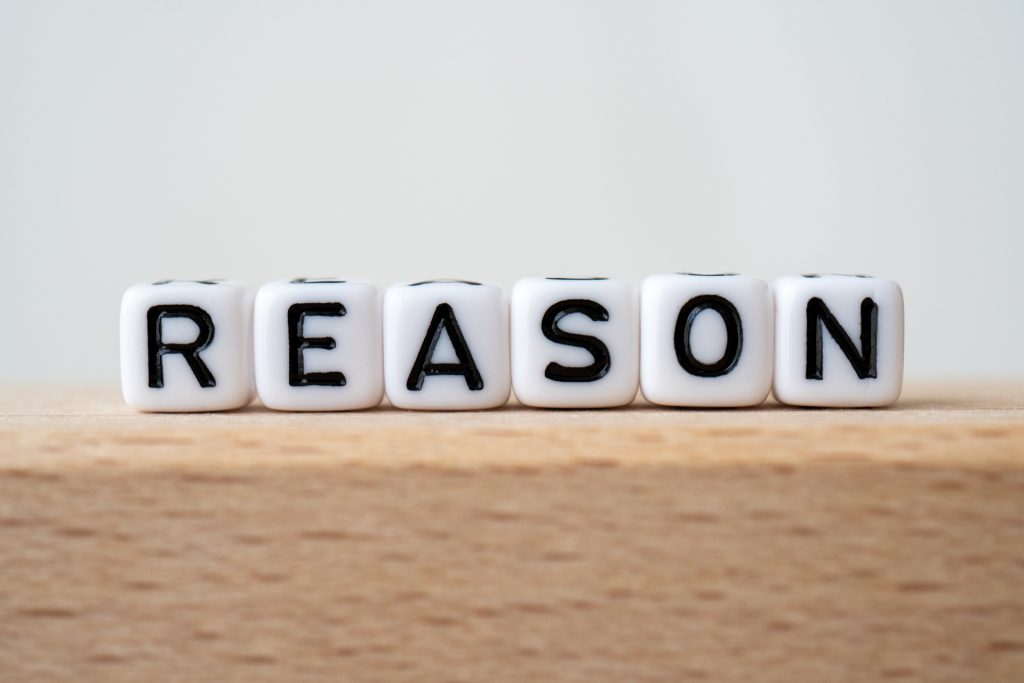
どれだけ安価であっても、自分たちの使用環境に見合うスペックや自分たちが満足する作業性や使用感が得られるなら、特に問題はないでしょう。 企業方針として〝コストを優先〟するのであれば、それはそれで構わないと思います。
それに、そもそも〝安価〟という定義が、何を持って「安価」というのか… それが各社各様であることを考えると安価ということでの線引きは、いささかナンセンスなのかもしれませんね。 ある会社は〝30万〟を高い! といい、別の会社では、「100万」を安い! と言うのであれば、比べようがないですもんね。苦笑
ともあれ、少なくとも 『買わされた』 などと遺恨を残してしまうような買い方はさけるべきです。 いずれにしても、グリップコンベアを使っていくのは作業現場のスタッフさんです。 どうせなら、ストレスなく作業ができ、作業現場が楽になって、作るモノが品質よく綺麗にできるようになることが第一だと思います。
くれぐれも、買った後の〝後悔〟をしないように気を付けてくださいね。
ご相談、お問合せはお気軽にどうぞ。