産業用インクジェットなどを使った印字を行っていく作業で、時に、厄介な問題が発生することがあります。
めざせ、100人! ってことで、Youtube やっているのですが、なんと! お陰様で100人突破しました! これもひとえに、皆さまのお陰です。 次は1000人目指してコツコツ。 できればチャンネル登録お願いします!
さて、今日のテーマは…
印字作業は、時に厄介な問題をはらむ。
産業用インクジェットなどの印字装置を使えば印字作業は楽にできます。 なので、印字作業そのものについては、そういった機器が、『勝手に的確に』やってくれるものだと信じて、恐らく、それほど深く考えずに作業されている場合が多いのかなと思います。
でも… ちょっと待ってください。 安直に考えていると、そこにちょっとした「落とし穴」があるかもなのです。
もしかしたら取り返しのつかない事態に陥ってしまう… 可能性があります。
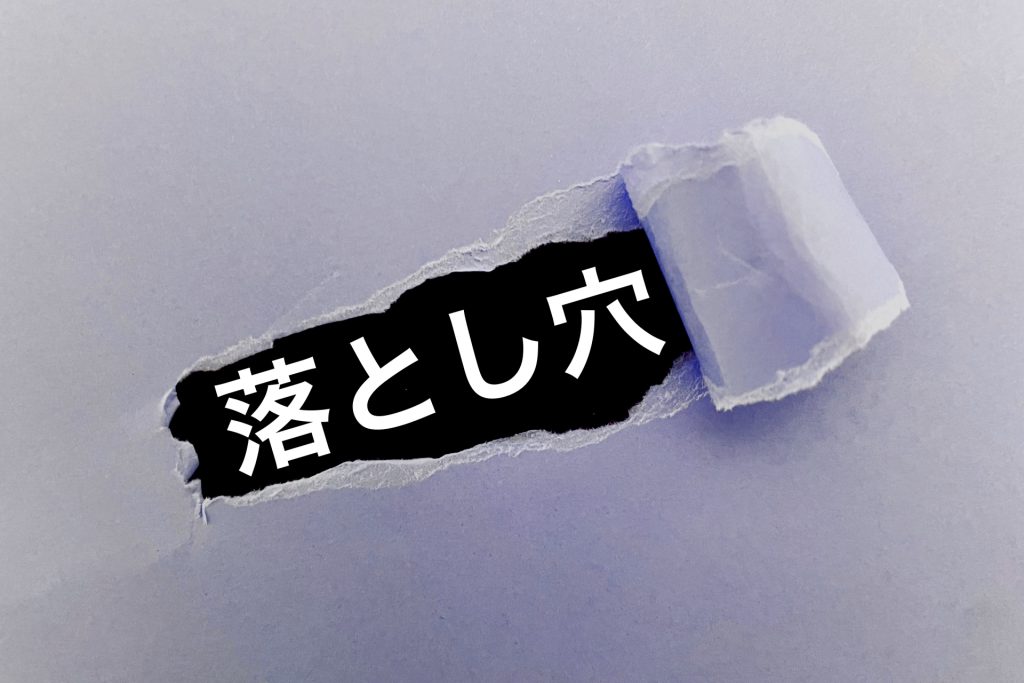
厄介な、『無印字』問題。
印字作業をする中での厄介な問題とは? なんだか、ご存知ですか?
それは、『無印字』です。 無印字とは、
印字されていない状態のもの(が混じること)。
です。 作業時に何らかの要因で〝印字されない状況〟が起き、『無印字』なものが製品として紛れ込んでしまうのです。
作業する側からすれば、全面的に印字装置を信用しているわけですから、『無印字』なんて起きっこないと思っているわけです。 なので、それが発覚するのは、概ね、市場に出てしまってから。 運が良ければ、出荷先で食い止めることができるという感じです。
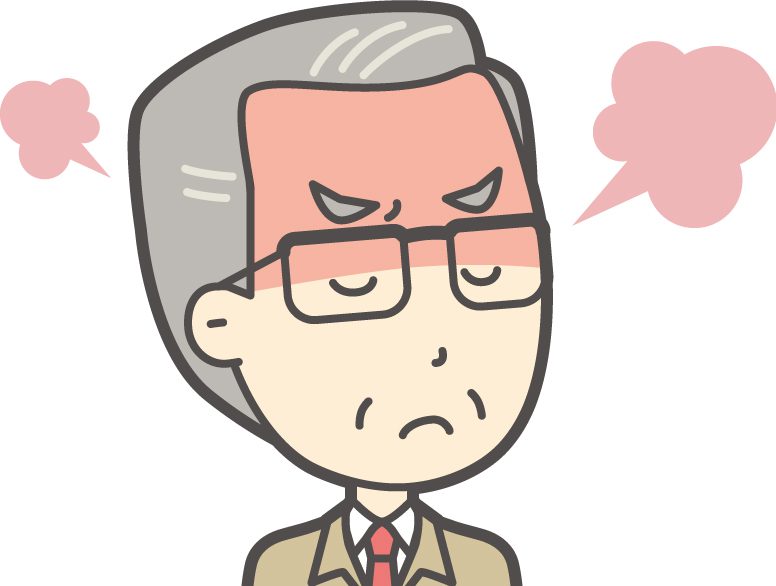
印字されてないのがあったぞ!
と、突然のようなクレームがやってきて、『え、まさか!!』と現場が慌てふためき、挙句、犯人捜しを始めてしまう…というケースを耳にしたことがあります。 「無印字」が出回ってしまうと、モノによっては大事になってしまいます。
賞味期限等が見れなくなってしまうのですから、大変です。 それが、例えば、医薬品などになれば… ぞっとしますよね。
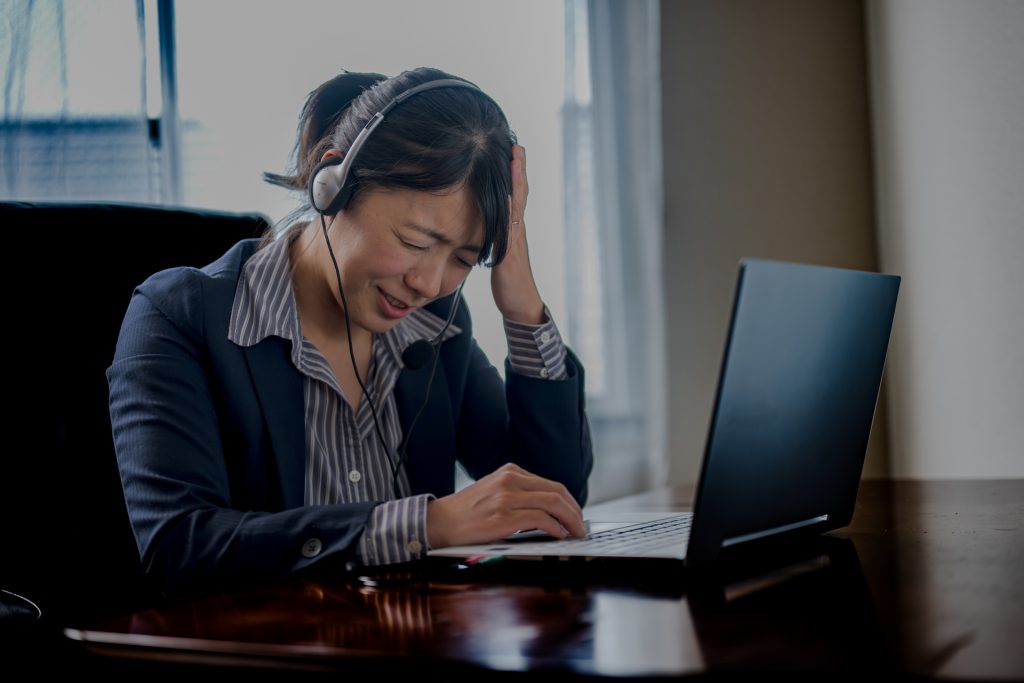
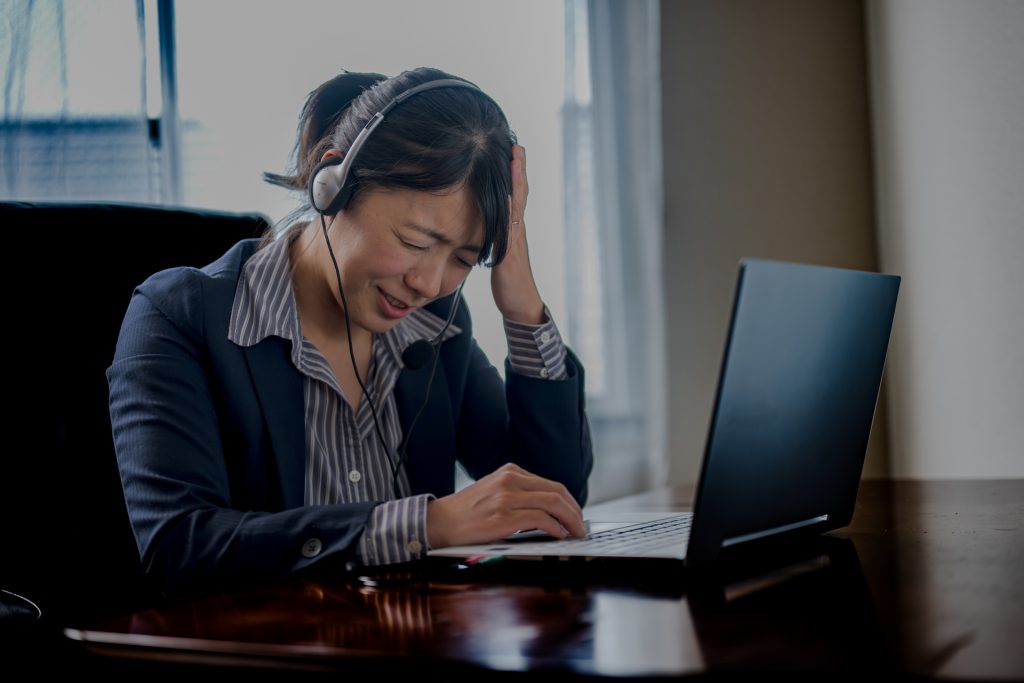
なぜ、起きる?
では、なぜ、無印字が起きてしまうのか?
哀しいかな印字機器と言えど、機械です。 万が一もあり得ます。汗
メンテナンスに不備があって正常に印字できない状態になっていたり、トリガとなるセンサーに不良や不備があれば無印字は起こります。 社内システム上で上位から印字内容を設定しているというケースでは、システムの不備による無印字の発生もありえるのです。 なので、無印字が絶対ゼロとは言い難いのです。
無印字を防ぐには?
機械である以上、それを絶対ゼロにすることは、ある意味不可能であると言えます。 99%ゼロにできたとしても、1%でも、無印字になる可能性が存在しているのであれば、それは完璧ではないからです。
印字機器やスタッフを追及するよりも、もっと大事なことは 『如何に未然に防ぐか?』 ということであって、無印字が起きたとしても適切に対処できる環境にしておくこと… が命題になるはずです。
無印字を回避する取り組みは、まず、まっさきには印字機器を使う環境を整えることと、印字後の確認です。 それをすることで、無印字は回避できます。 ちなみに、印字後の確認は、目視、または、カメラなどの画像センサーを用いた方法が一般的です。
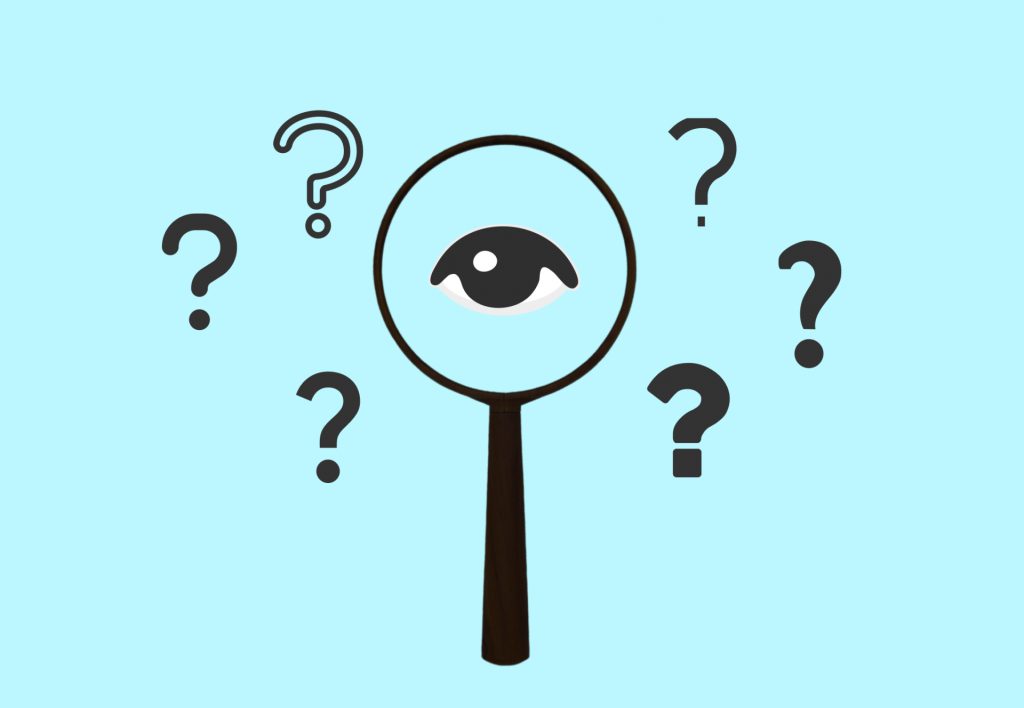
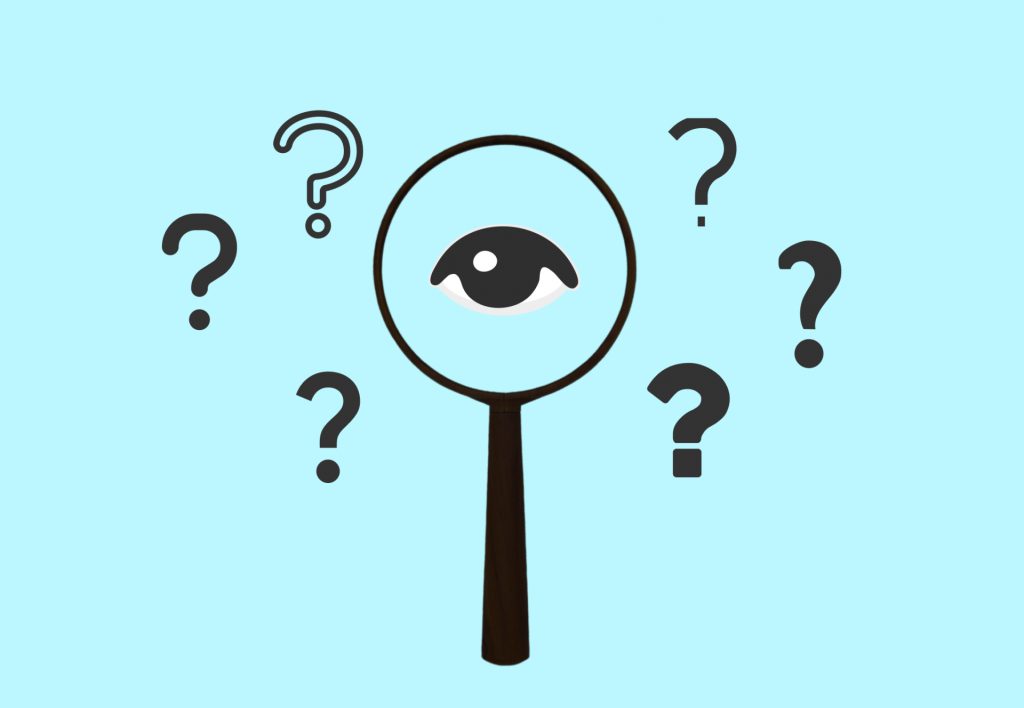
もっとも… 「確認のオプション」を設けたとしても、それが機能していなければ同じなのですが、そこは徹底されることが大前提です。
というわけで、 菓子類の土産物のように包装紙でラッピングされた箱へ印字を行う際の〝無印字〟への対策と対応に向けた過去の事例です。
「無印字」への対策と対応。
…とまず、新幹線や空港もしくは、みやげ物屋さんの棚で包装紙で綺麗に包まれたお菓子などの箱を目にすると思うのですが、それがどうやって包装されているかご存知ですか?
実は、土産用のお菓子の箱などへの包装も機械化されていて、〝箱を包装紙で包むような包装形態〟のことをオーバーラッピングと言い、〝上包機〟と呼ばれる専用の包装機械が使われています。
この時のクライエント様は、土産物用のお菓子を作っている会社さんで、上包機を使って包装作業をされている担当部署さんからでした。 依頼された内容は、
上包機で包装された箱へインクジェットで印字した後、文字検査を行い、NGがでた時に自動的に排除したい。
という内容で、それに加えて、
上包機から出てきた箱をそのまま印字できるようなラインにしたい。
とのことで、その経緯を聴いていると、包装後の次の工程で印字作業をしていく中で『無印字』がでてしまったから… といういきさつ。
工程間に〝人の手〟が介在すると、印字を終えているのかどうかが不明なモノが生じ、〝無印字〟なモノが製品へ混入してしまうので、そこを何とかしたいというのが本件の根っこの主旨でした。
なかなか、ややこしいテーマ。
使われている上包機は、それ〝単体〟で使う仕様になっていて、包装後はそのまま排出されるのみ。
包装後の取り出し口にテーブルを置いて排出される商品(ワーク)を受け、専用のコンテナへ一旦溜めて、それを次工程の印字作業へという流れで作業をされていました。 ここで、一番ネックになったのが、排出されるワークの〝姿勢〟でした。
包装後のワークは、整列されることもなく、そのまま放り出されるような格好で排出されるため、その姿勢(向き)が一定していないのです。
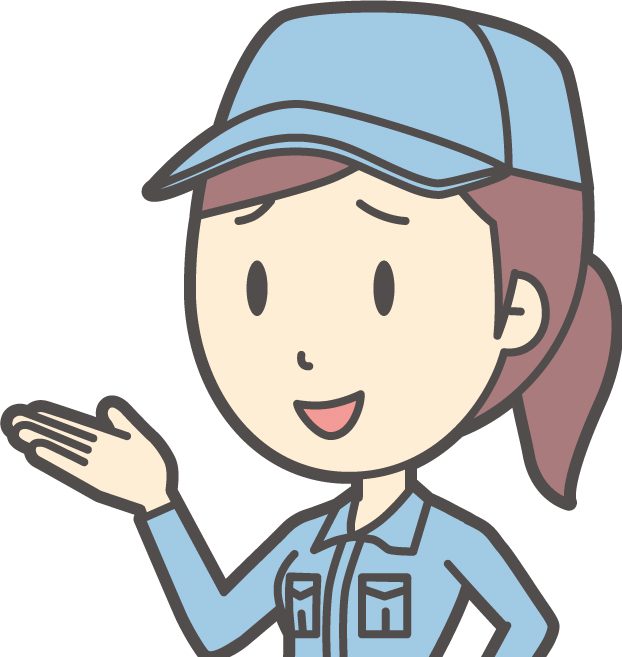
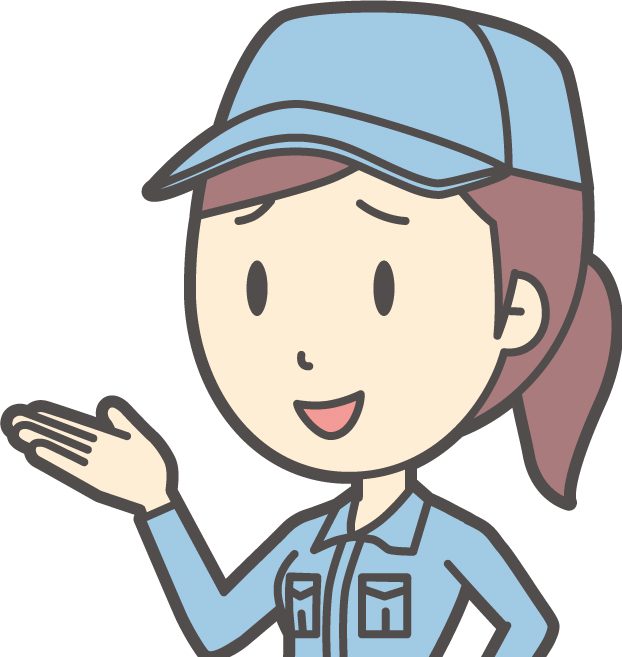
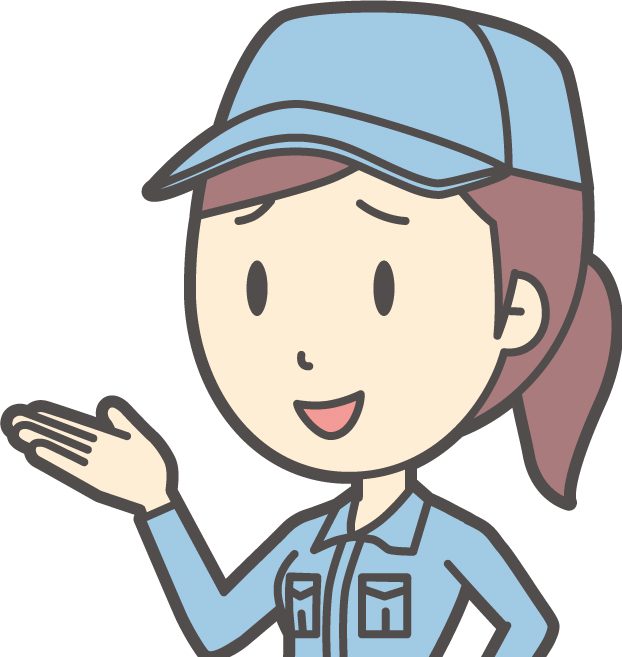
包装後にそのまま印字できるような
ラインにしてね!
という要望に応えるためには、排出後のワークの姿勢や位置をどう整えるか? が一番のテーマになったのでした。
サイズが〝極端に違う〟箱でも?
どんなワークのサイズであっても上包機の排出口からはセンター基準で排出されてきます。 排出時のワークの状態を観察していると、比較的大きなサイズのワークは安定した姿勢で排出されるのですが、小さいワークでは回転してしまうような格好になってしまい、安定しないのが見てとれました。
ワークの側面の所定位置に対して印字を行うのですが、そのためにはワークの姿勢を整える必要があります。 この時、厄介だったのが、対象となるワークのサイズの巾でした。 小さい物で120mm角くらいのサイズ、最大で340x270mm程度の取り扱いになります。
上包機の基準に合わせて設計してしまうと、搬送に関しては楽なのですが、逆に、ワークのサイズが変わるたびに器材の位置調整を余儀なくされてしまう事態を招いてしまいます。 その都度、100mm程度の調整が発生してしまうというわけです。 電機制御で位置調整を行うという方法もあるのですが、それで対応するにはまったく予算がない… 汗
手動で調整ということも考えられるのですが、手作業による調整はミスを誘発してしまう可能性があります。 誤った調整を行ってしまうと文字のサイズや字体の雰囲気が変ってしまい、文字検査にも影響が生じてしまうのです。 また、スタッフへの作業負荷をかけてしまうという面もあります。 それに、そもそも、所定の印字位置がワーク側面の下の方にあったので、対応しづらいというのもありました。 なので、その考えは却下しました。
ということで、プリントヘッドと文字検査用カメラは位置調整を行わず〝固定化〟し、排出されるワークの姿勢を整えながら、強制的に印字・検査ができる位置へ… という方法を考えました。
余談:文字検査についての捉え方。
余談ですが、文字検査を行う際の捉え方について、お伝えしておきますね。 ザクッとですが2通りです。
印字した文字列の有無のみを確認するという捉え方。
〝あるなし〟を判定するだけのもっとも、シンプルな捉え方で、無印字を避ける方法として広く用いられています。 最近では、〝あるなし〟判定に特化したようなカメラセンサーがリーズナブルな価格帯で市販されています。
無印字への対応はできる反面、印字された内容に関する判定ができないので注意が必要です。 内容が判断できないとは、例えば、本来は〝20YY-MM-DD〟という内容が正解だったとして、設定を誤っていて、「20XX-NN-EE」になっていた… などいう場合がそれです。 また、印字された文字列が鮮明でない場合でもOKとしてしまう場合もあります。
印字上の欠けや、印字データの整合性を含めて判定するという捉え方。
「あるなし」よりも、もっと厳密・厳格に判定を行うという捉え方です。 印字した内容に欠けがないか? また、印字データとしての整合性があるか? といった内容を判定します。
印字上の欠けとは文字自体が欠けるのはもちろんのこと、インクの詰まりや、印字後の擦れなどによって字体が鮮明でない場合を指します。 字体に欠けの部分があれば読み違えの恐れもあるため、シビアさが要求される分野では、検査に対しては、より厳格な捉え方で対応されます。
印字データの整合性は、印字すべきデータと実際との整合性についての判断です。 先の〝あるなし〟の例で述べたようなことへの判断ということになります。
厳格な検査を行う場合には、その程度にもよりますが、器材としても高度なスペックが要求され、また、判定を行うソフトウェアに対しては特注になる場合が多いため、比較的高額な構成となります。 ちなみに、器材を含めた価格帯は対応業者によってピンキリです。 加えて、対応業者によっては、定期的な〝メンテナンス(保守契約)〟が必要になる場合もあるため、制作依頼時には十分な確認が必要です。
今回のケースでは、後者の〝文字の欠けも含めて検査する〟というパターンでした。 印字時にプリントヘッドとワークとの距離が変ってしまうと文字サイズにも影響が生じ、また、ワークの位置が変ると検査時のカメラの焦点距離や検査タイミングにも影響がでるため、如何にして、安定した印字や検査が行える環境にするか? もポイントでした。
「上包機」に接続した文字検査機能付きの印字用搬送装置。
装置を設計するにあたっては、印字に対する安定性や作業性と文字検査時に対する操作性を両立させる必要がありました。
検査NG品を振り分ける機能。
要望として、検査後のNG品を振り分ける機能をつけてほしいということでしたので、それも設計に盛り込みました。 確かに、折角、検査で〝無印字〟を発見したとしても、それがOK品に紛れてしまうと元も子もないですもんね。
というわけで、できた装置がこちらになります。 … 完成品を撮り忘れるという痛恨のミス。滝汗
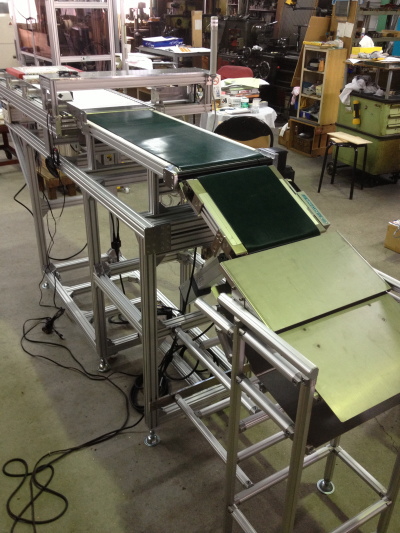
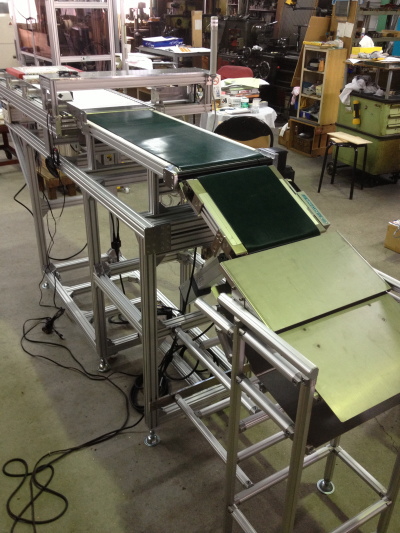
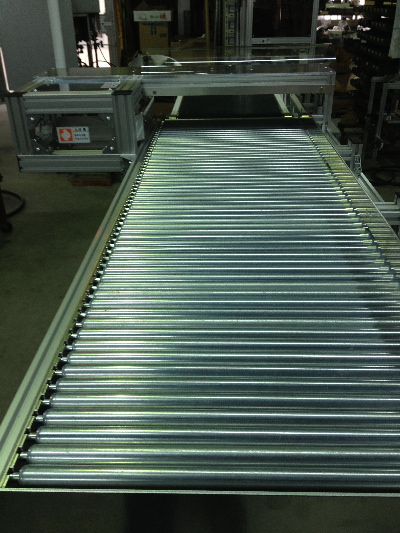
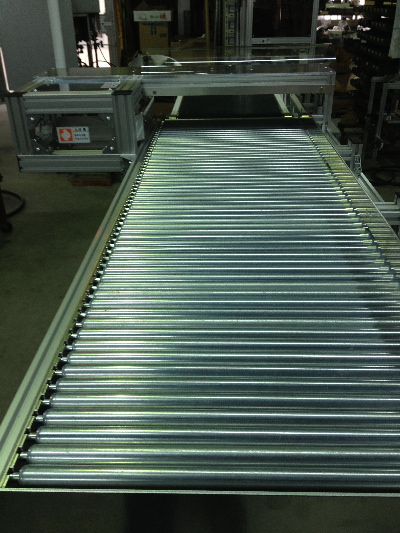
上包機との接続には、ワークの取り扱いを考え、ローラーコンベアを採用しました。 ちなみに、エアー機器を使わないオール電化な構成です。
動画で。
動作を動画でご覧いただけます。
IJPは、メーカー問わず対応可能です! ご相談、お問合せはお気軽にどうぞ。
※ 自社専門サイト〝マーキングコトはじめ〟より転載・リライト