ラベルを使用する利点は、バーコードの読み取り精度が高くなるという点とワークのロスが少ないという点です。
めざせ、100人! ってことで、Youtube やっているのですが、なんと! お陰様で100人突破しました! これもひとえに、皆さまのお陰です。 次は1000人目指してコツコツ。 できればチャンネル登録お願いします!
さて、今日のテーマは…
設計を見直し、使い勝手を追及。
前回までに紹介したラベラーを搭載した自動貼り付け装置について、どちらの装置も〝下から取る〟をコンセプトに設計を行っていました。 〝下から取る〟方法は、機構的にシンプルになり、そこそこ能力もでるため、特にまずくはないな… と思ったのですが…

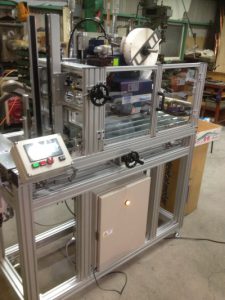
〝下から取る〟の難点。
〝下から取る〟という方法は、下から順に取っていくので、装置が動作中であっても上からの補充が簡単にできるというメリットがあります。 しかし反対に、供給を行なおうとする一番下のワークには、積み上げられた枚数分の自重がかかります。
積み上げすぎると供給時にその影響が生じてしまうのです。 また、自重の問題は、ワークの大きさにも依存してきます。 つまり、サイズの大きさによって、供給時の条件が変ってしまうというわけです。
Aというワークでうまく供給できたとしても、それより大きなサイズになると極端にパフォーマンスが落ちたり、積み込みが予定より減ってしまったりといった弊害が生じます。 運用していく上では、その辺りをうまくコントロールする必要がありました。 幸い、この方式で納めた会社さんでは、特に問題なく使って頂けているようです。
とは言え、機械を運用していく上では『誰でも簡単に使える』に越したことはありません。 なので、この方式を見直し、より使い勝手の良くなる方向で設計を見直しました。
〝下〟の方式から、『上』の方式へ。
下から取るから自重の作用を受ける。 では、上から取る方法にすれば、自重は関係しないのでは? という発想で、『上から取る』方式を考え、リリースしました。 『上から取る』方式は、積み重ねたワークの上から順番に取っていくという方法です。 この場合だと、供給を行う面には自重の作用を受けないので、安定した供給ができます。
唯一の難点が、装置稼働中にワークの補充ができないことです。 しかし、ワークの供給が終わったタイミングで簡単にできるため、機械にそれほど明るくない方でも安心して扱えるというメリットがあります。 マガジンにワークをセットすれば、後は自動供給して、ラベルを貼り付けるのでラベル貼りの時短にもつながります。
ただ… 下から取る方式よりも機械動作が増えるので、その分、処理能力が若干下がってしまうのですが、作業性や動作の安定性を重視した場合には断然こちらがお奨めです。
「上から取る」方法による自動供給機能付きラベル貼付装置
できた装置がこれです。 供給の方式が異なるだけで、ラベル貼付以降の処理は同じです。 ラベラーには、前回同様、サトー社製のオートラベラを使用しています。 ラベラ上で、都度、ラベル印字を行えるので、表記内容が変る場合に便利です。
できた装置。
供給の後、ワークを上下のベルトでグリップして搬送するという機構を用いています。 これにより、ラベル貼付時のワークのズレを解消しています。 なお、ラベル貼りつけ後は、バーコードリーダーにて読み取りチェックをして排出を行っています。
排出の際、きちんと集積したいという要望があり(オーダー頂いた後に、要求されてきました。(T□T) )、それに対応するように排出後の受けも設計しました。 動画でご覧いただけます。
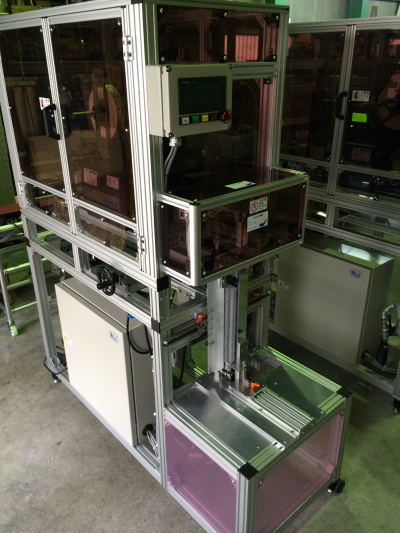
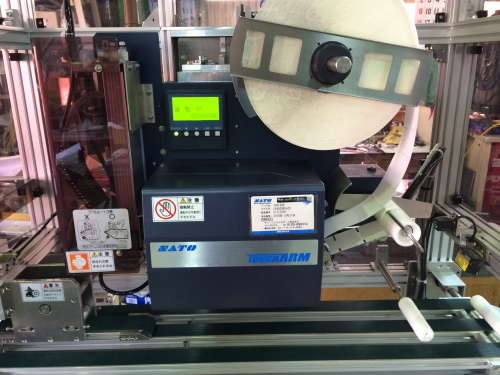
動作を動画で!
ご相談、お問合せはお気軽にどうぞ。
※ 自社専門サイト〝マーキングコトはじめ〟より転載・リライト。