包装の目的には、大きく分けて2つのタイプがあります。
それは、直接〝商品の顔〟になるような販売に対する訴求効果が求められる包装と、もうひとつが、BtoBのような企業間での取引のために用いられる包装です。
単純な感覚で言えば、前者が〝お金をかけてでも!〟という感覚で、後者が〝できれば、お金をかけたくない〟という感情になるのではないでしょうか?
めざせ、100人! ってことで、Youtube やっているのですが、なんと! お陰様で100人突破しました! これもひとえに、皆さまのお陰です。 次は1000人目指してコツコツ。 できればチャンネル登録お願いします!
さて、今日のテーマは…
レーザーマーカーを効果的に使って。
印字を行う場合を考えると、場合によっては、広いエリアにたくさんの内容を印字したいという要求が生じます。 今回は、そんな要求をお持ちのクライエントさんへの事例です。
昔から使ってた専用機が壊れた…
クライエント様からの依頼は、
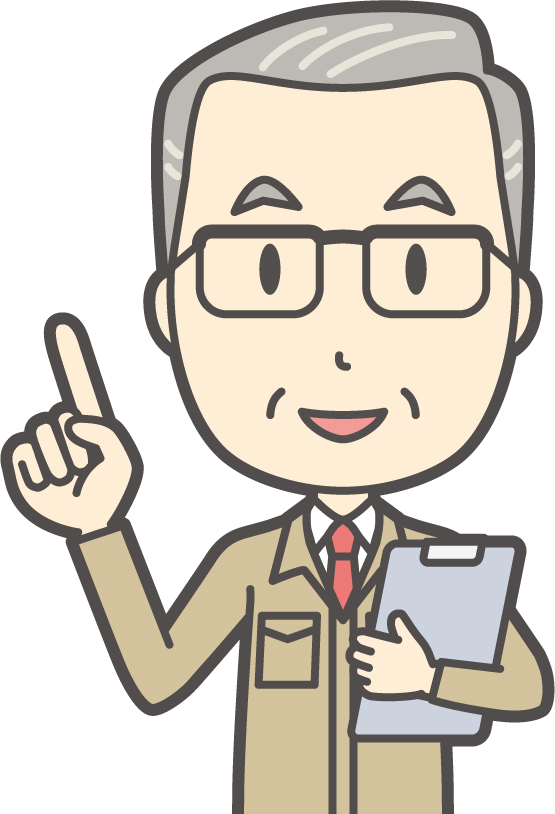
・カートンの表面に内容物の明細を記載したい。
・片面ではなく両面に印字したい。
という内容でした。 このクライエントさんでは、ずいぶん以前から専用機を使ったカートンへのコストコントロールを実施されていました。
内容物の種類が都度変るような形態の商品だったので、予め明細を印刷しておくということができず、専用の印刷機を特注で製作し、その機械を使って、出荷品への対応をおこなっていたのこと。
打ち合わせ時には、まだ、機械があったのでみせてもらいました。 ちょうどコピー機くらいの大きさの機械で、構造的にはシルクスクリーン印刷による印刷方式を応用した形式のものでした。 記載内容を記した原稿を専用のスクリーンに転写して、それを『判』にして、カートンへ印刷していくというかなり良く考えられた機械だったのを覚えています。
しかし、その印刷機も老朽化し、製作したメーカーもなくなり、使い続けることができなくなったので、今回の依頼へとつながったというわけです。
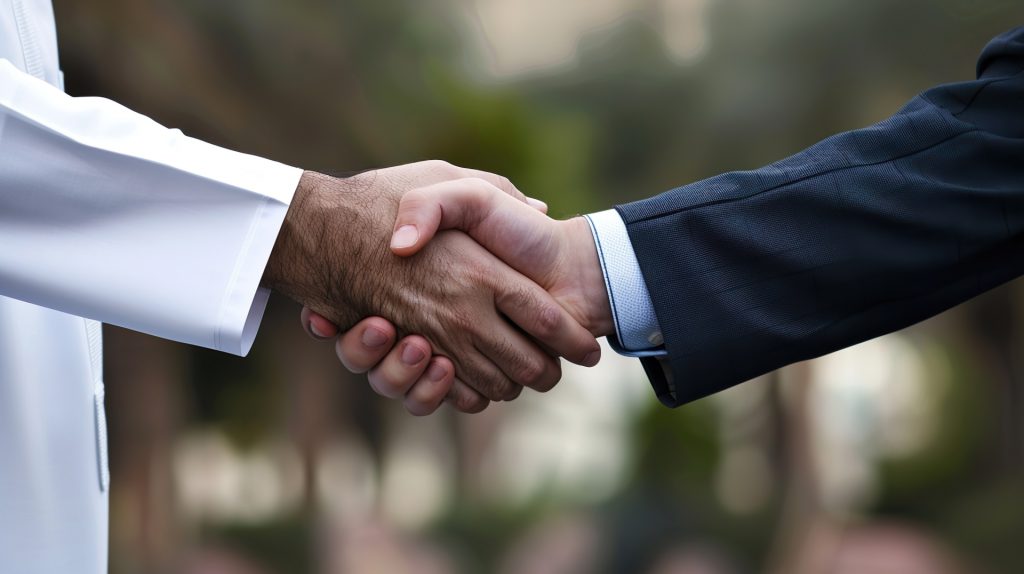
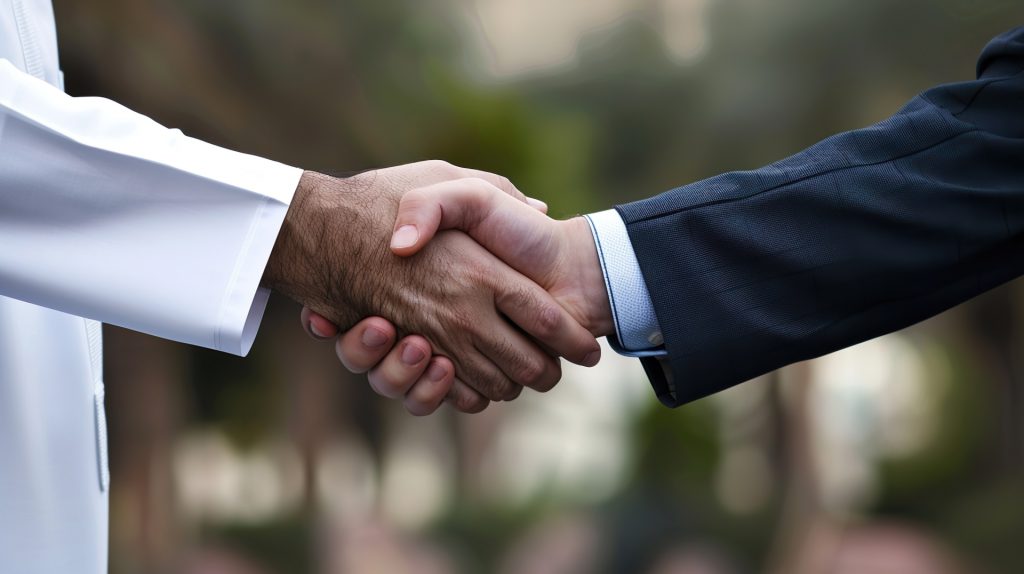
印字の方式は、過去にはこだわらないので、時代に応じた方法で刷新したいとのことでした。 専用機での場合では、1枚だけの印刷でも判を作る必要があり、それが手間であり、コストもかかっている。 インクで汚れてしまうのも嫌だから、使い勝手のいいものをつくってくれとお願いされました。
機体設計上の制約。
どんな印字機を使うか? 印字する情報量も多く、また、印字を行う面積が大きかったため、広範囲で鮮明に印字できるという特性をもったレーザーマーカーによる対応をご提案しました。 しかし…
装置を設計するにあたっては、大きな制約がありました。 それは、設置場所への制約です。 要望されたのが2階の作業場だったのです。 でも、2階の作業場へはハッチのような大きな搬入口はなく、窓からか、もしくは、2階にあがる細い階段を使うか? もしくは、器材の上げ下げに使われているゴンドラリフトを使うか? の3つのルートしかありません。
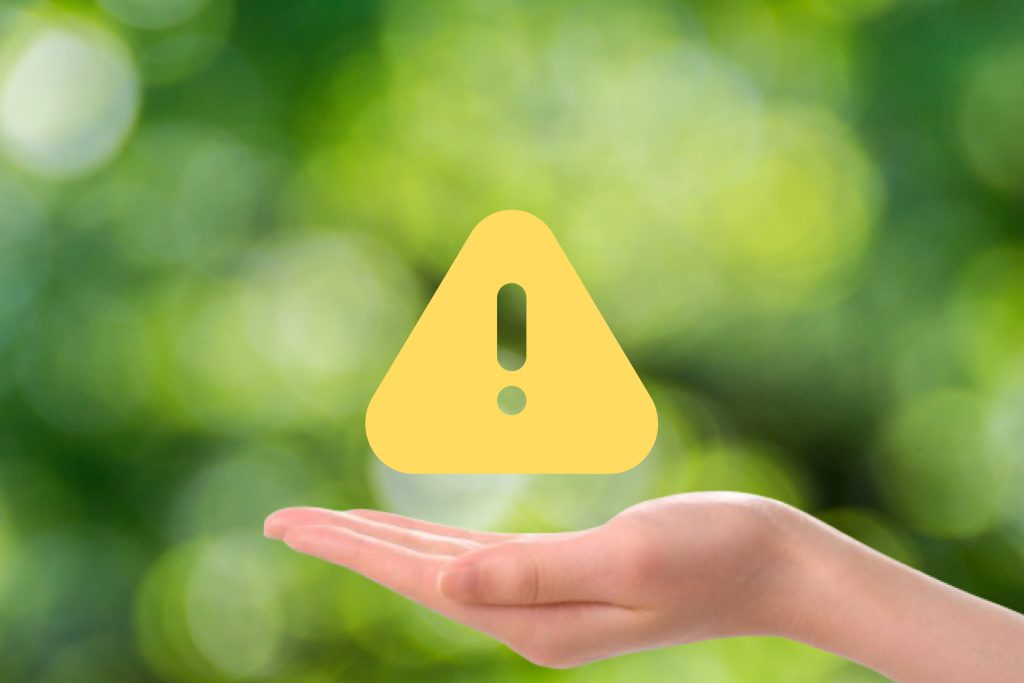
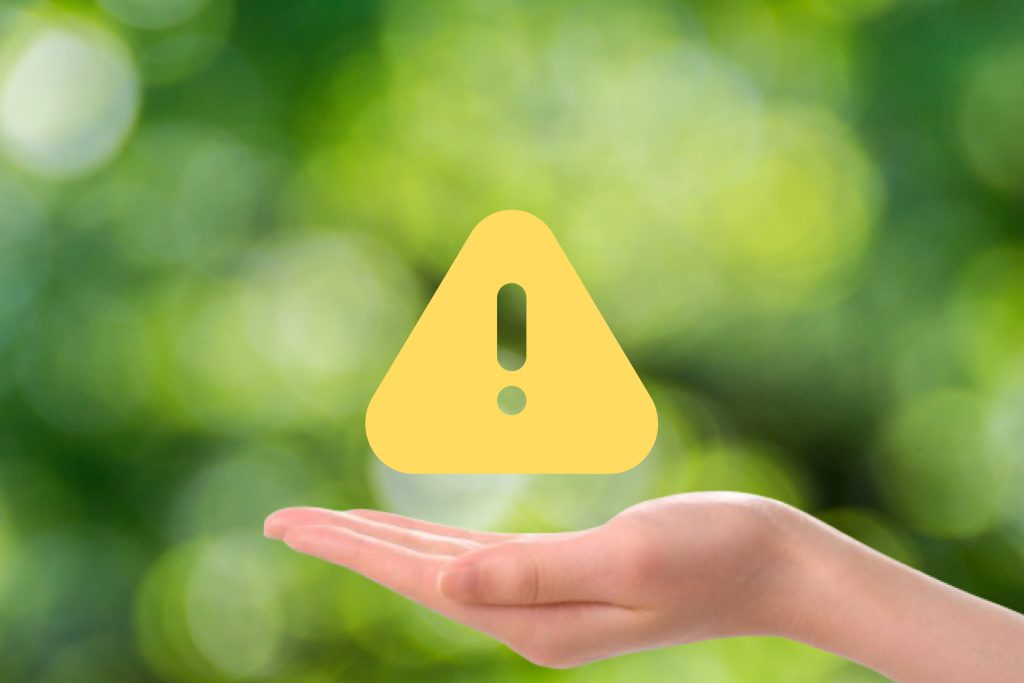
まず、2階へ上がる階段は、人ひとりが通れるくらいの巾だったので、すぐに却下。 ついで、2階の窓からという方法を考えてみたのですが、それも現実的ではなく、やめ… なんでか?
と言えば、建屋の2階部分の外側には庇(ひさし)の張出しがあって、搬入するにはそれが障害になってしまうこと。 また、2階の床床面とその窓の下面には高さがあって、搬入できたとしても室内で床面まで降ろすのが厄介であること。 という理由から、2階部分からの搬入方法は除外しました。
残るは、ゴンドラを使った方法です。 ゴンドラは内作されているようで、〝1m角(四方1m)程度〟が運べるようなサイズでした。 結局、搬入経路として使えるのはこのゴンドラしかなく、つまり、ゴンドラに納まるサイズで装置を設計しなければならないというのが制約条件でした。
見事、制約をクリアした装置!
ゴンドラが使えるサイズで装置を考えるとなると、両面への対応をどうするか? ということが課題になりました。
両面の対応を考えた場合、表面に印字した後、裏返して印字するという方法が考えられます。 でも、この方法では反転させる機構が必要になり、機体が大掛かりになる可能性があります。 仮に、出来たとしても搬入できなければ意味がありません。 なので、今回はその案をやめ、他の方法を考えることにしました。
それに… 裏返してという方法は、どうもありきたりで、安直すぎて、自分の中で腑に落ちなかったんです。 両面に対応できる、シンプルで且つ、コンパクトになるような方法はないものか… ということで、カートンを〝立てて搬送させる〟という方法を思いつきました。 〝立てる〟ことで、裏返すことなく同時に両面への印字が可能になります。
この方法により、装置もコンパクトに設計することができ、無事にゴンドラによる搬入ができました。
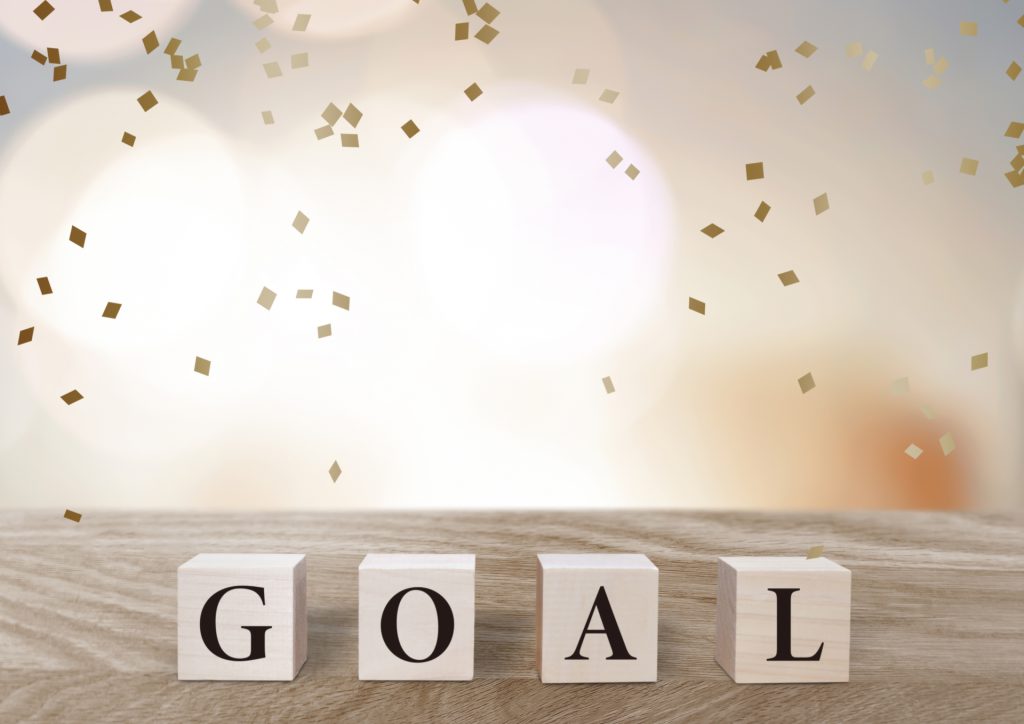
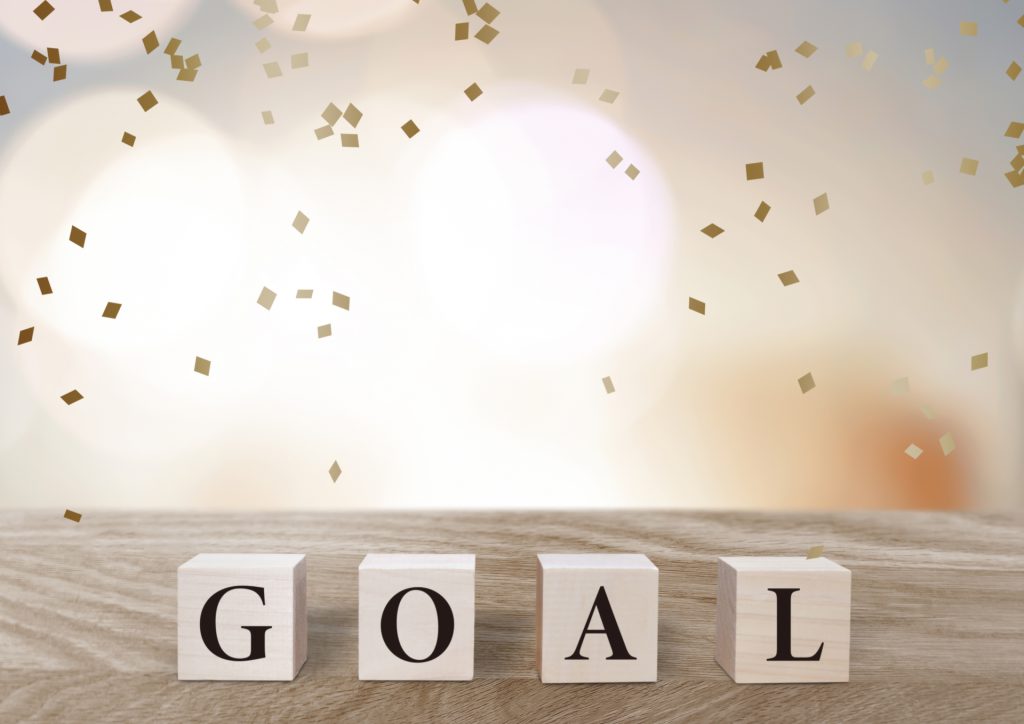
できたのがこれです!
完成した装置がこれです。 ゴンドラへの対策として、機体を分割できるよう設計し、2階に上げた後、ドッキングするような構造にしました。
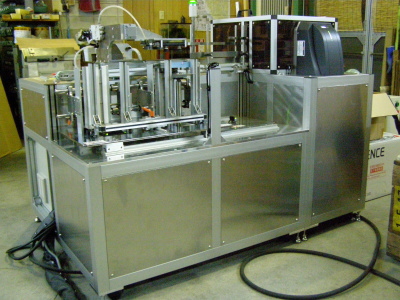
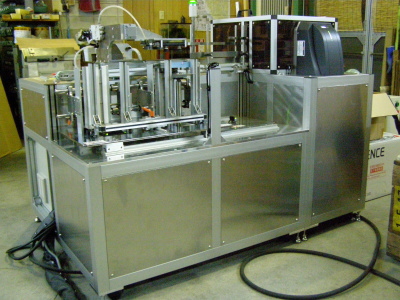
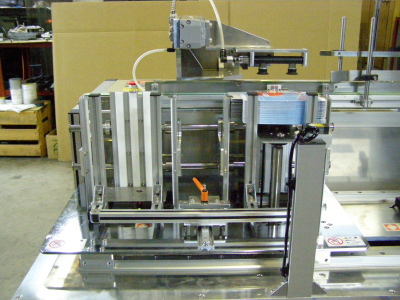
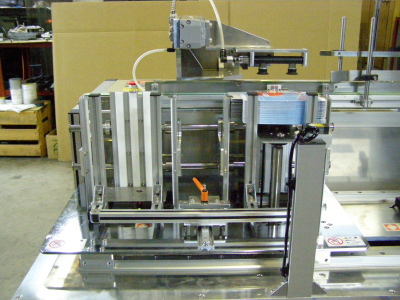
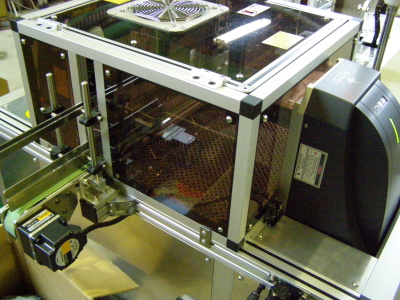
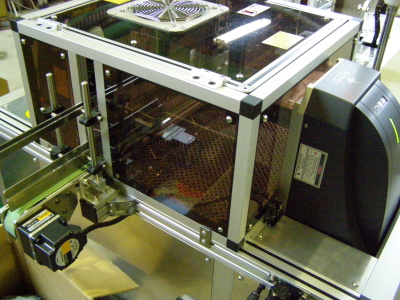
作業効率を少しでもよくするため、マガジン部にスペア機能を持たせています。 これにより、資材補充時のロスタイムの低減につなげています。
また、自動供給することで作業への全体的な効率を上げています。 なお、印字に関するデザインや印字内容についてはレーザーマーカー側のコントローラでセットします。 本装置での操作は、処理枚数のセットと起動指示です。
動作を動画で!
動作を動画でご覧いただけます。
レーザーマーカー運用時の注意点。
これを補足としてお伝えしておきます。
レーザーマーカーを運用する上で、特に気をつけるべき事柄があります。 それは〝臭いと紙粉〟です。 金属などに対してなら、気にならないのかもしれませんが、ここでの例のような場合、「紙表面のインクを焼き飛ばして」印字を行います。
なので、特有の匂いが発生し、且つ、紙粉もそれなりに発生します。
匂いに敏感なスタッフが居られる場合、細心の注意が必要になります。 使用される場合には、集塵機を設置するなどの対策を十分に行なわれるのがベターです。 また、紙粉については、累積されていくため、こまめな清掃が必要です。 こと、集塵機を導入される場合、フィルターの目詰まりには十分注意するよう心がけてください。
ご相談、お問合せはお気軽にどうぞ。
※ 自社専門サイト〝マーキングコトはじめ〟より転載・リライト。