包装の目的には、大きく分けて2つのタイプがあります。
それは、直接〝商品の顔〟になるような販売に対する訴求効果が求められる包装と、もうひとつが、BtoBのような企業間での取引のために用いられる包装です。
単純な感覚で言えば、前者が〝お金をかけてでも!〟という感覚で、後者が〝できれば、お金をかけたくない〟という感情になるのではないでしょうか?
めざせ、100人! ってことで、Youtube やっているのですが、なんと! お陰様で100人突破しました! これもひとえに、皆さまのお陰です。 次は1000人目指してコツコツ。 できればチャンネル登録お願いします!
さて、今日のテーマは…
の前に… レーザーマーカーはご存じですか? 産業用インクジェットプリンタと並んで広く用いられています。 今回はレーザーマーカーを使った内箱(カートン)への事例をお伝えしたいと思います。
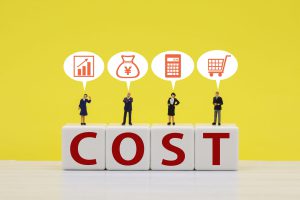
レーザーマーカーの特徴をおさらい。
まず、インクジェットの場合では、インクを用いるため、印字を行う対象物によっては印字できたとしてもすぐに消えてしまうといった問題があります。 また、インクのにじみやカスレなどで、印字時の不鮮明さが問題になることもあります。
加えて、インクジェットではインクの粒(ドット)により印字を行うため、ドットの欠けにより誤読を誘発しやすいという問題があります。 例えば、『8』が『B』に見えたり『1』が『7』に見えたりするなどといった状態がそれです。
一方、レーザーマーカーによる印字ではレーザー光を用いた〝ライン〟による印字になるため、インクジェットに比べてより鮮明な印字を行うことができます。 対象物にも依りますが、誤読を誘発するような文字の欠けは置きにくいです。 また、レーザーマーカーでは、対象物の表面を〝焼き削って〟印字を行うため、文字が消えるといったことが起きません。
印字した文字が消えないということは、つまり、〝消せない〟ということであり、〝消せない〟ということは〝改ざんされにくい〟ということを意味しています。
鮮明で、且つ消せない印字という特性を考えると、レーザーマーカーは製薬や医療の業界に向いていると言えます。 なぜか? と言えば、そういった業界では誤読されてしまう状況は許されず、また、改ざんされないことが絶対的な条件であるためです。
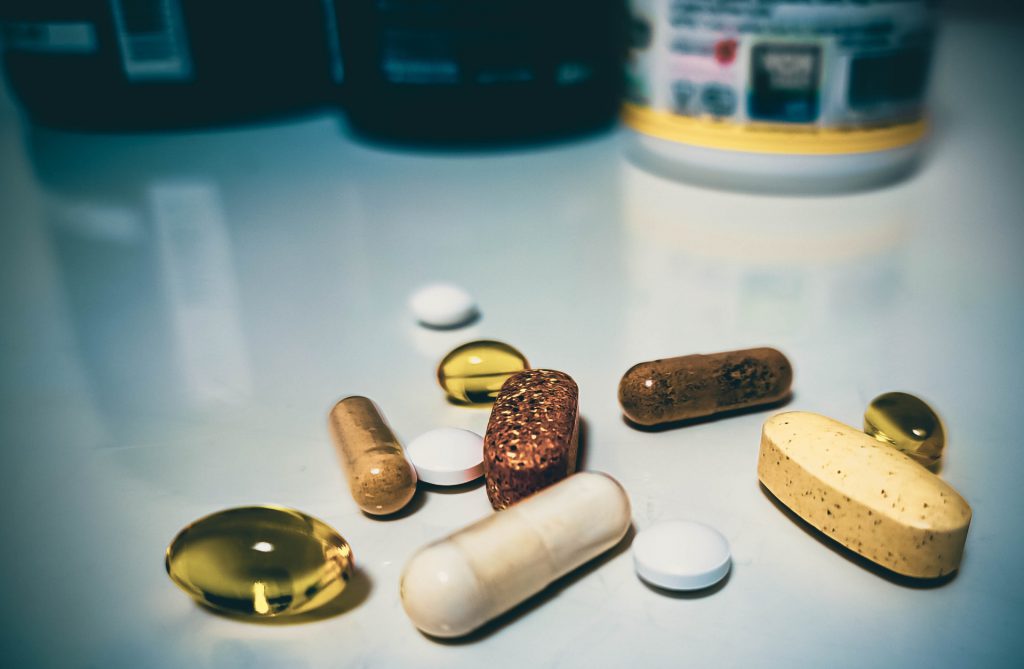
というわけで、レーザーマーカーを用いた製薬向けでのカートンへの対応についてをお伝えします。
ワンタッチカートンでの事例。
少し… いや、正直なことをいうと、かなり前のことになるのですが…苦笑
某製薬会社からの依頼で製作したワンタッチカートンに対応した装置の事例です。 ワンタッチカートンを自動供給し、レーザーマーカーで印字を行い、印字後は文字検査を行うという流れです。 もっとも、文字検査の部分は、うちではなく外作です。
知っておきたいワンタッチカートンの罠。
はっきり言って、この案件、嘗めてました… 何を嘗めてたか? っていうと、〝ワンタッチカートンに〟です。
ワンタッチカートンでは、その名の通り「ワンタッチ」で、箱の底部分を組み立てられるカートンのことです。 糊りやテープを使うことなく簡単に底面の組み立てができるため、作業現場では重宝がられているようです。
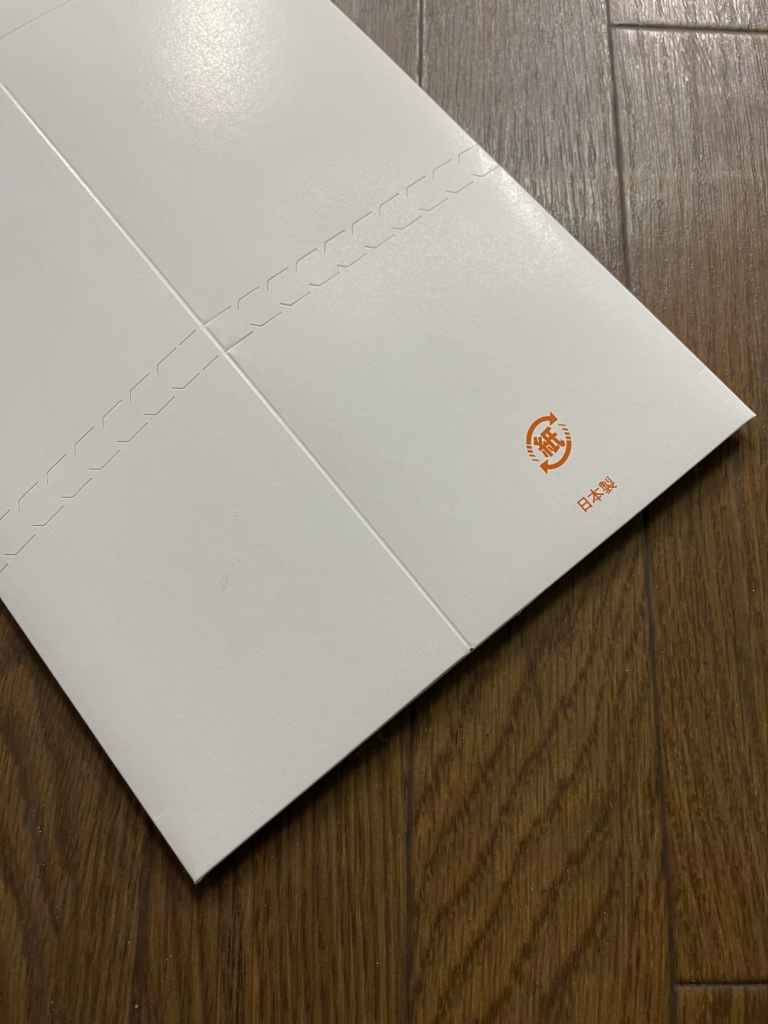
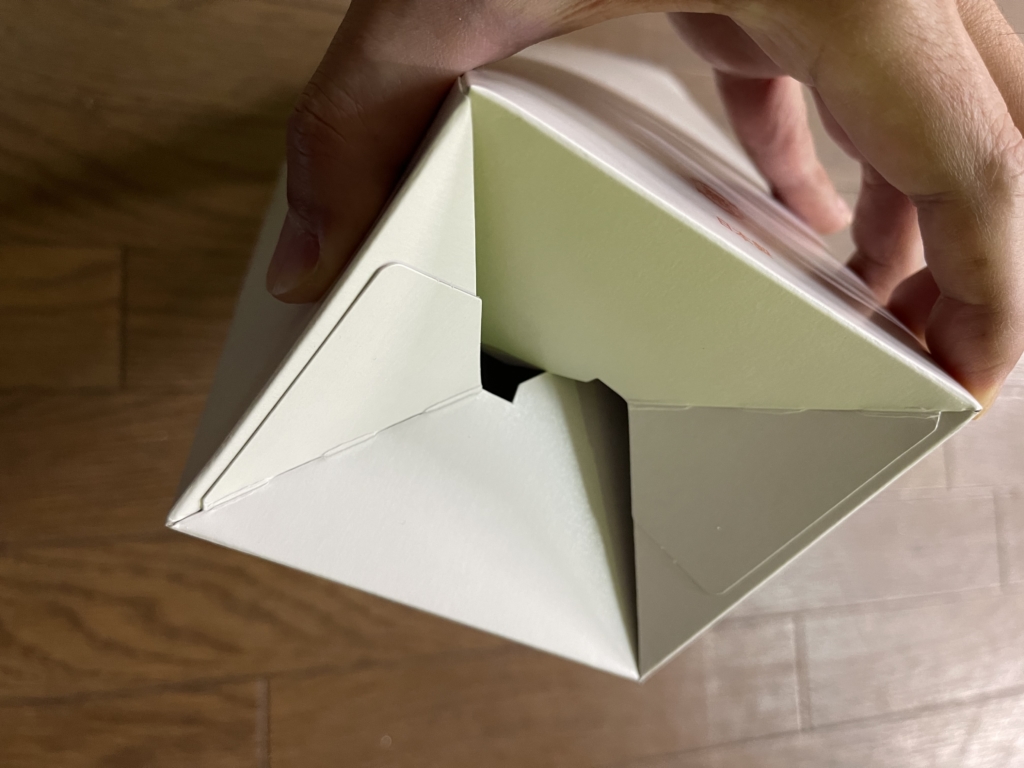
で、ワンタッチカートンでは、箱の組み立てを実現するために底の部分が他の部分に比べてかなり分厚くなっています。 この厚みは、1、2枚積み重ねただけでは特に目立たず、問題がないように見えます。 しかし! ある程度の枚数を積み重ねると、問題が顕著に現われてくるのです。
打ち合わせ当初、1枚程度しかみていなくて、平べったい板のような感じだったんです。 そのイメージで、この案件「楽勝じゃん!」なんてことを思って、それなりの装置を設計したんです。 でも、それが苦難の始まりでした。
ある程度装置が組めて、さぁ! という段階でカートンの束を預かり、装置へのセットを試みた時、初めて認識の甘さに気づかされたのです。(滝汗)
厚みが累積し、綺麗な積み重ねができないということが判明しました。
なんでや! 思ってたんとちゃう!!
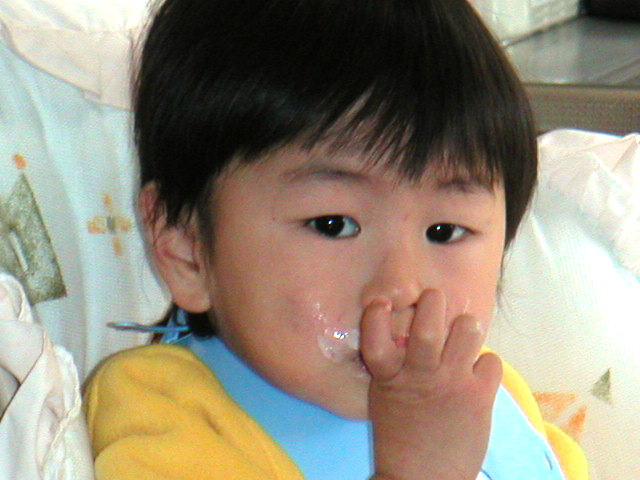
どうしよう…
頭が真っ白になりましたよ。 時間もないし、かつ、予算も…
「楽勝やん」で考えていたので、それほどの見積もりはだしていなかったんです。滝汗
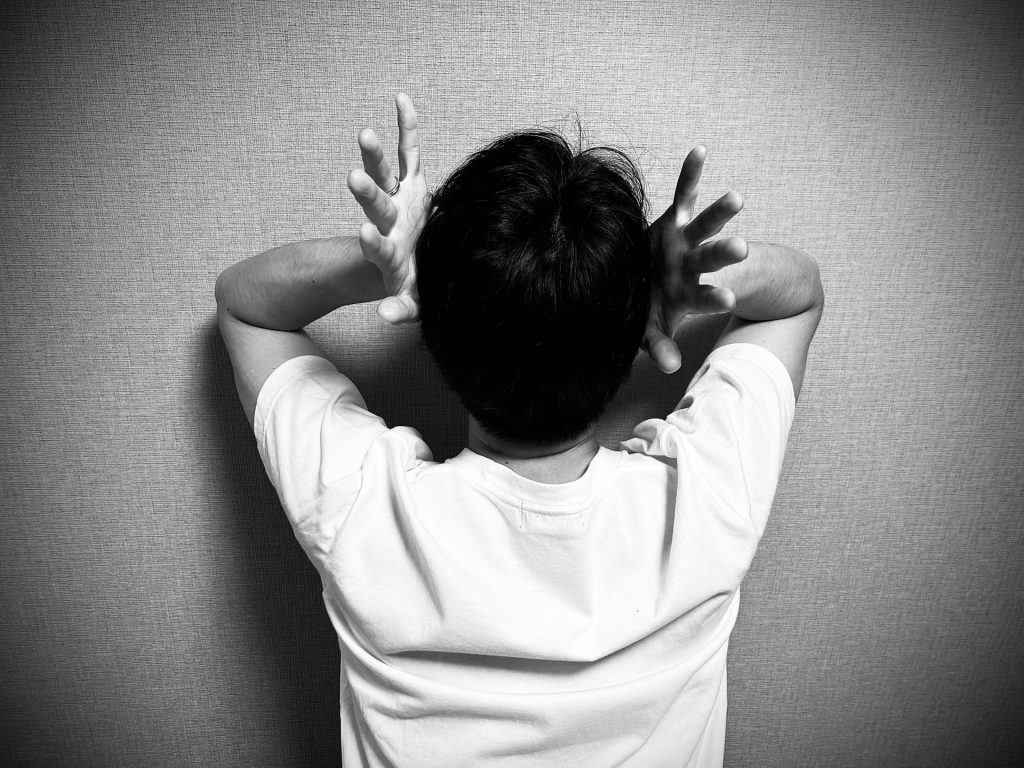
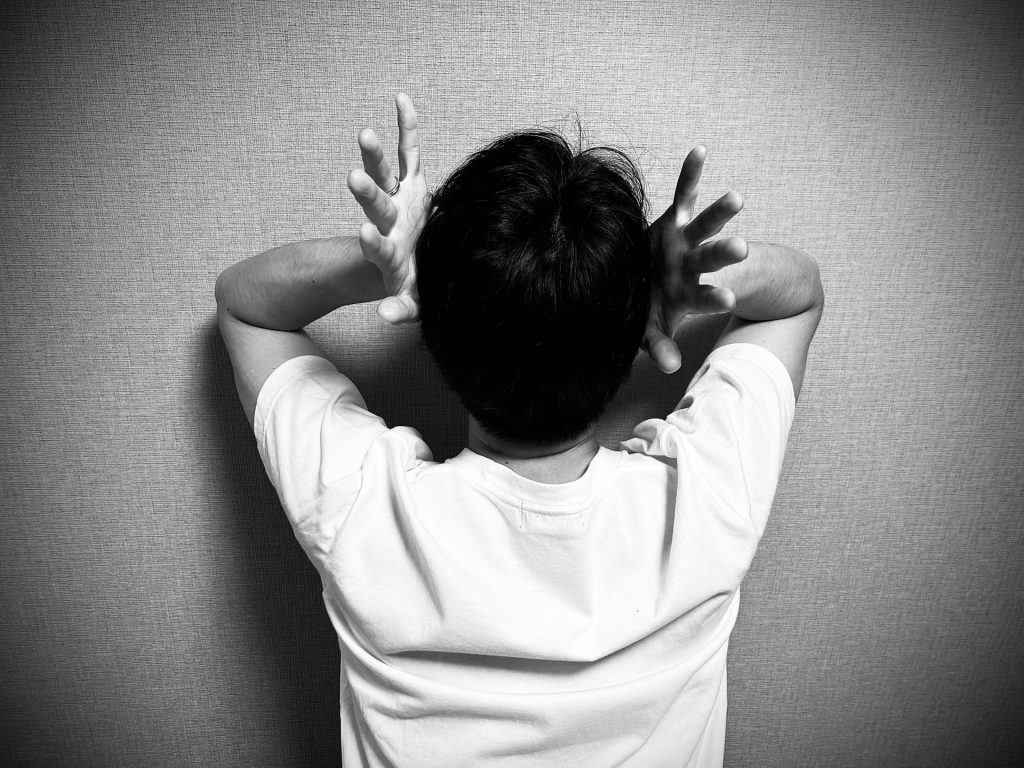
まぁ、金額的な面は見積もりを出してしまってる以上仕方がありません。 それに、甘く見積もったのは、こちらの責任です。 でも、納期が… ホントに、かなりやばい事態でした。 急きょな設計変更を加えながら、なんとか仕上げることができました。
少し余談になりますが、機械を設計する上では対象となるワーク(部材)の〝姿勢〟が重要になってきます。 それは、今回の件に限らず、全ての場合に言えることです。 ワークをどのように扱うか? は、ワーク自体の性質で決まってきます。
自立するのか、しないのか? 自立できても安定しているのか? 重ねた時にどうなるのか? 集めたときにどうなるのか? …などなど。 そういったことを十分検証し、理解した上で設計に入っていくというのがセオリーなんです。 しかし、今回の件ではちょっとというか、かなり詰めが甘かったです。
でも、おかげで随分と勉強になりました。
出来た装置。
要求された箱のバリエーションが多く、一番大きなサイズが、なんと! 巾300mm!! 小さいのが 巾100mmなので、かなりの巾の適用範囲になりました。 また、箱の高さも数種類あったため、設計・製作に苦労したのは、その辺りにも関係しています。 設計する立場でのホンネを言うと、適用範囲はなるべく狭めてほしい….. ということです。苦笑
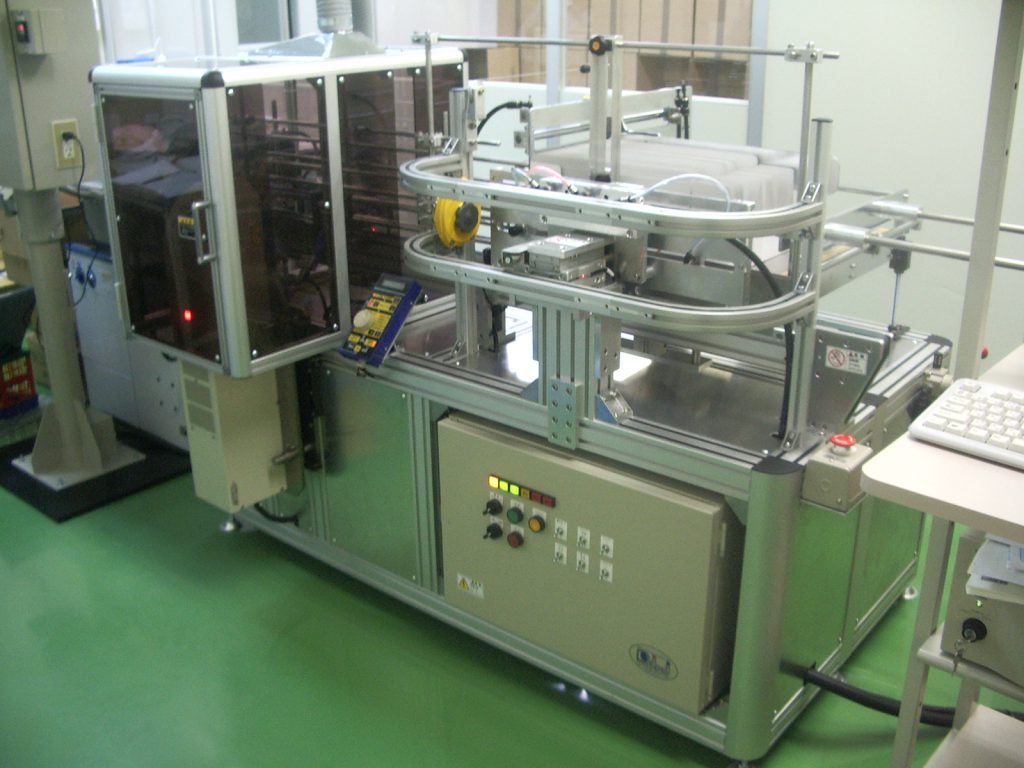
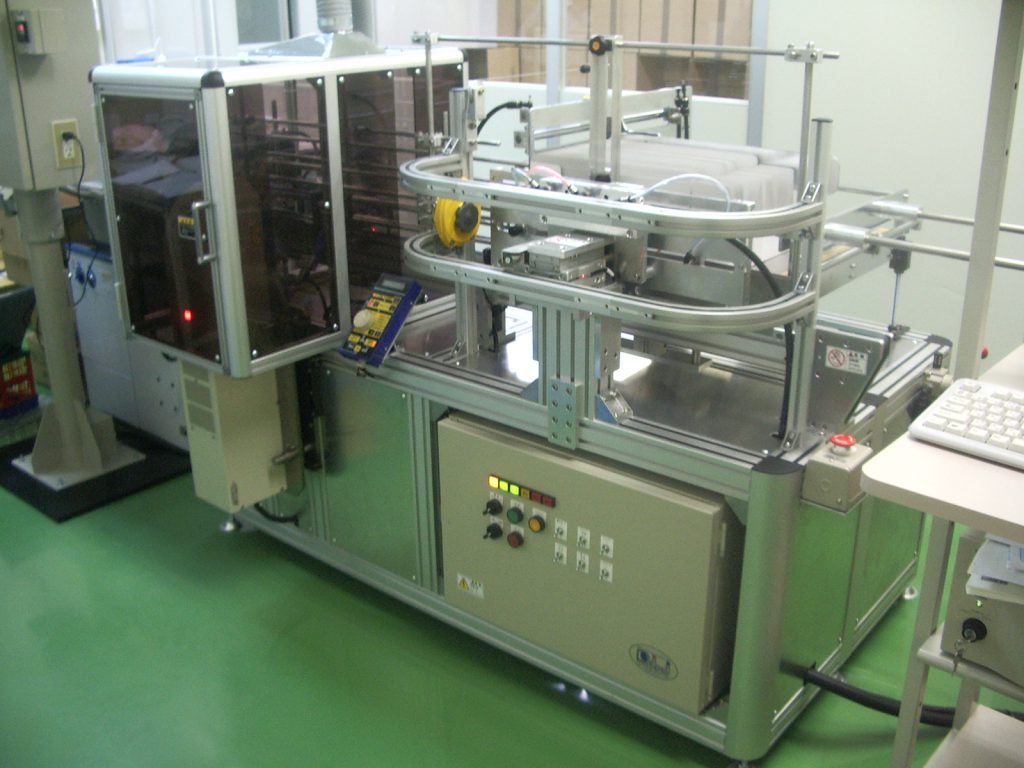
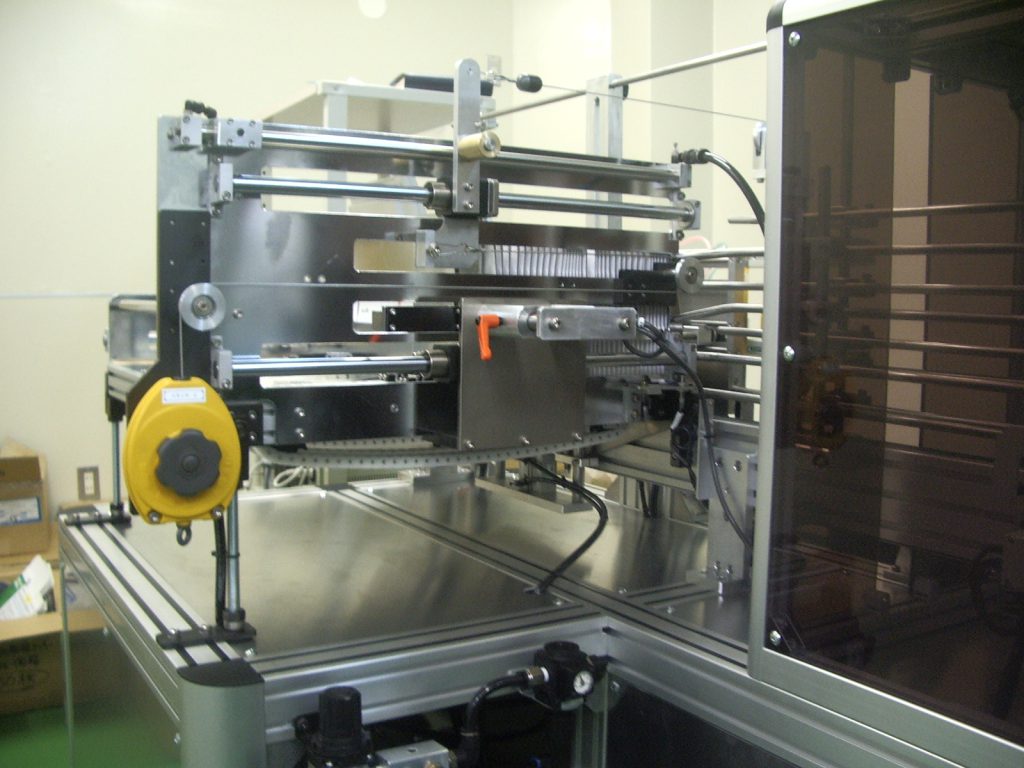
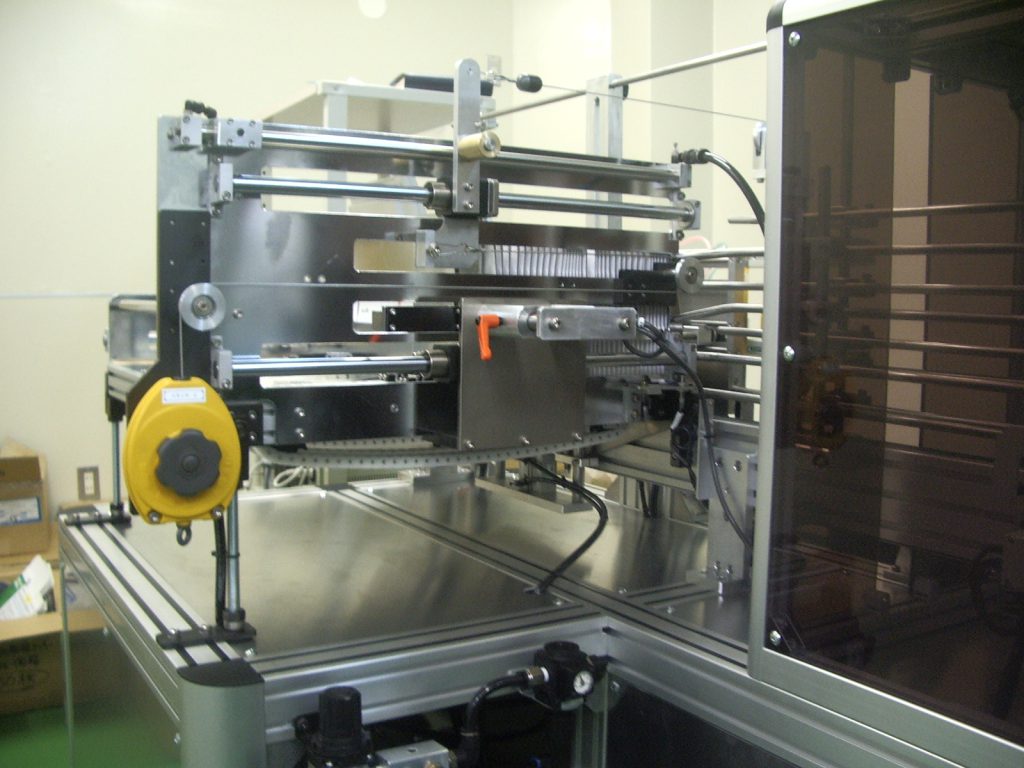
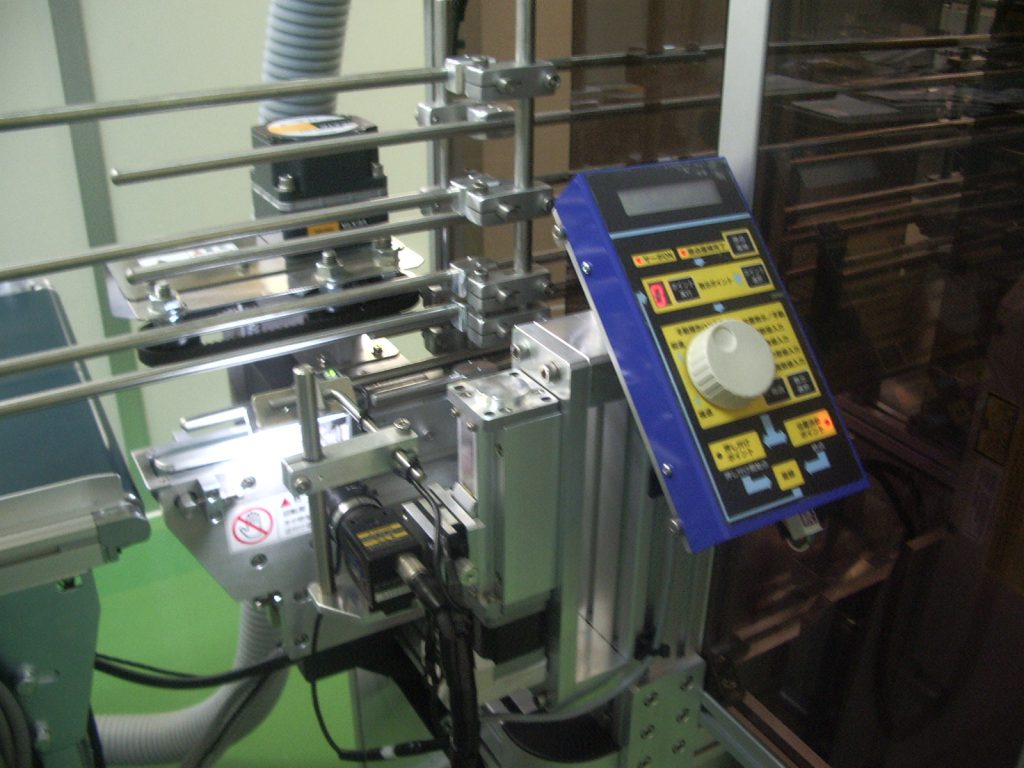
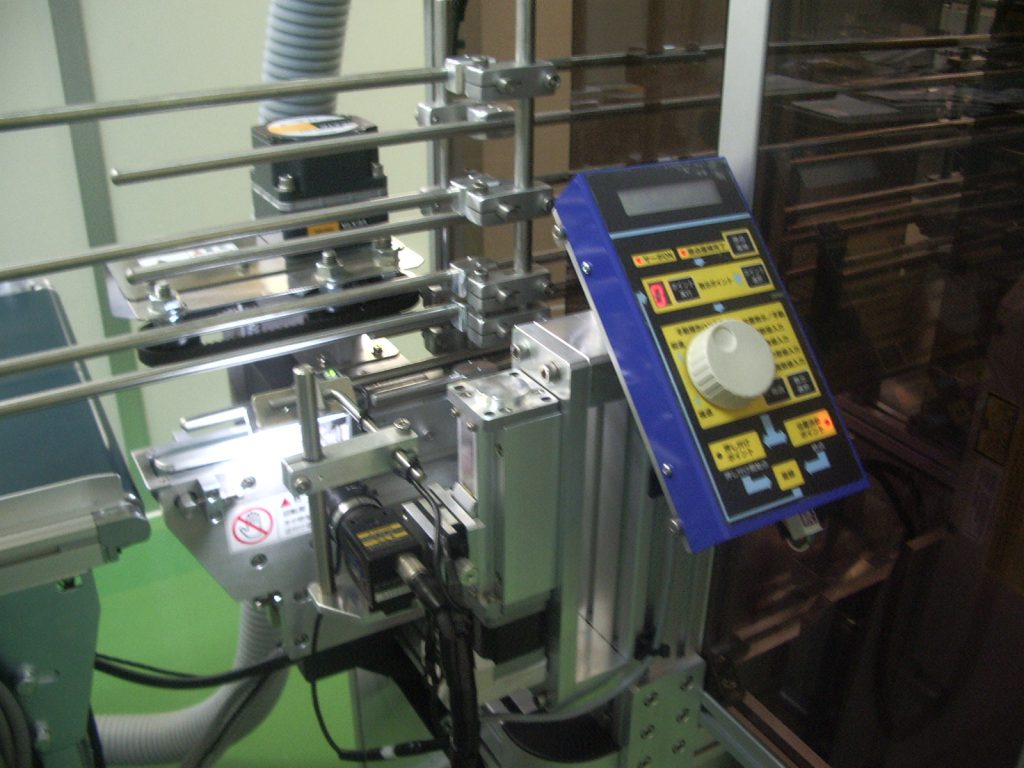
なお、うちのパートではありませんが、印字後の文字検査を行っています。 クライエントが製薬会社ということもあり、印字内容にはかなりシビアでした。(バリデーション作業もあり。)
動作を動画で。
動作を動画でご覧いただけます。 (カートンの供給部分)
ご相談、お問合せはお気軽にどうぞ。
※ 自社専門サイト〝マーキングコトはじめ〟より転載・リライト。