包装の目的には、大きく分けて2つのタイプがあります。
それは、直接〝商品の顔〟になるような販売に対する訴求効果が求められる包装と、もうひとつが、BtoBのような企業間での取引のために用いられる包装です。
単純な感覚で言えば、前者が〝お金をかけてでも!〟という感覚で、後者が〝できれば、お金をかけたくない〟という感情になるのではないでしょうか?
めざせ、100人! ってことで、Youtube やっているのですが、なんと! お陰様で100人突破しました! これもひとえに、皆さまのお陰です。 次は1000人目指してコツコツ。 できればチャンネル登録お願いします!
さて、今日のテーマは…
コストダウンを図る自動化でのアプローチ。
原料の運搬用途で用いられているクラフト袋について、自動化の視点でアプローチすることで効果的にコストダウンを図ることができます。 ちなみに、クラフト袋とは、米やセメントなどに使われている あの袋 のことです。
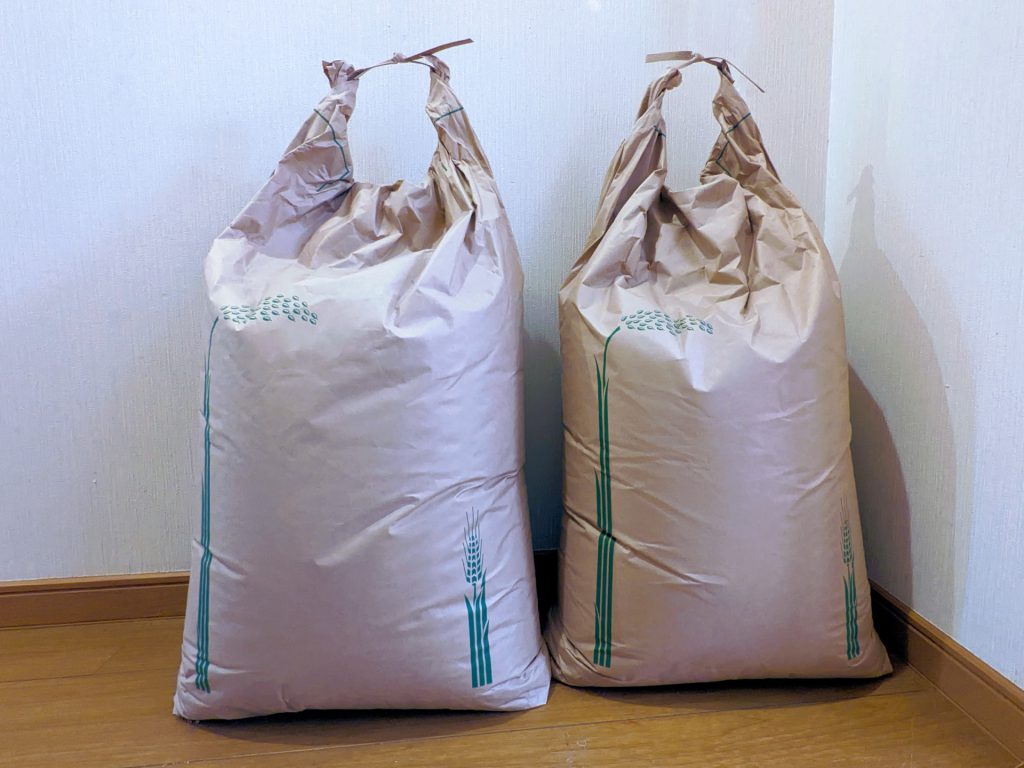

とはいうものの、自動化でというと、装置に関するコストに対して意識が向けられがちですよね。
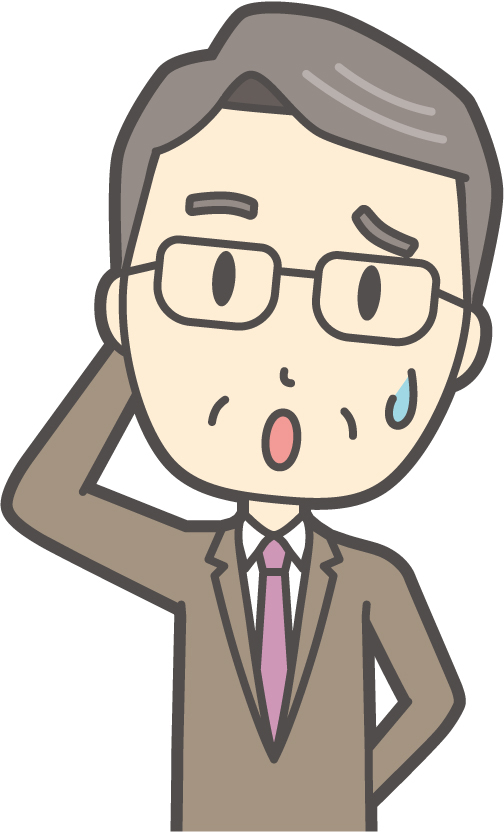
自動化って、機械代が高くなるやん。
設備投資がきついな…
もしかすると、装置へのコストがかかりすぎて資材のコストダウンにまで至らないんじゃないのか? などという感情を抱かれるのかもしれません。
確かに、〝目先だけ〟で捉えてしまうと資材へのコストダウンは難しいのかもしれません。 しかし、自動化を考える場合には〝包括的〟に捉えるという視点が大切になってきます。 つまり、全体を通じて どうなのか? どうなるのか? という捉え方です。
全体とは、資材の単価のみならず、スタッフの作業時間、作業性、管理にかかる諸経費など、トータルで見てみるということです。 まぁ、これはクラフト袋の場合に限ったわけじゃなく、全てのことに対して言えることなんですけどね。
自動化のメリット。
装置を考えていく上では、印字を行う際のワーク(クラフト袋)の扱い方が重要なポイントになります。 扱い方には大きく2つあります。 ひとつが、人手による手差しの方法で、もう一つが、機械的に自動で袋を投入するという方法です。
自動的にワークを投入する方法でのメリットは、手差しの方法に比べて 『劇的に作業効率があがる』 ということです。 どういうことかというと…
まず、手差しの場合では、装置に対して手作業でワークを挿入する必要があるため、スタッフがつきっきりで対応する必要があります。 一方、自動的にワークを投入する場合では、ワークのセットさえ行えば機械が自動的に処理を行うため、スタッフがつきっきりになる必要はありません。 機械が印字を行っている時間でスタッフは別の仕事をすることができます。
つまり、作業時間の効率化を図ることができるというわけです。
また、ワークの自動投入のような自動化によるアプローチでは、誰にでも簡単に作業ができる環境になるため、スタッフの作業負荷を下げたい! とか、作業現場の環境を変えたい! というところにすごくおススメなのです。
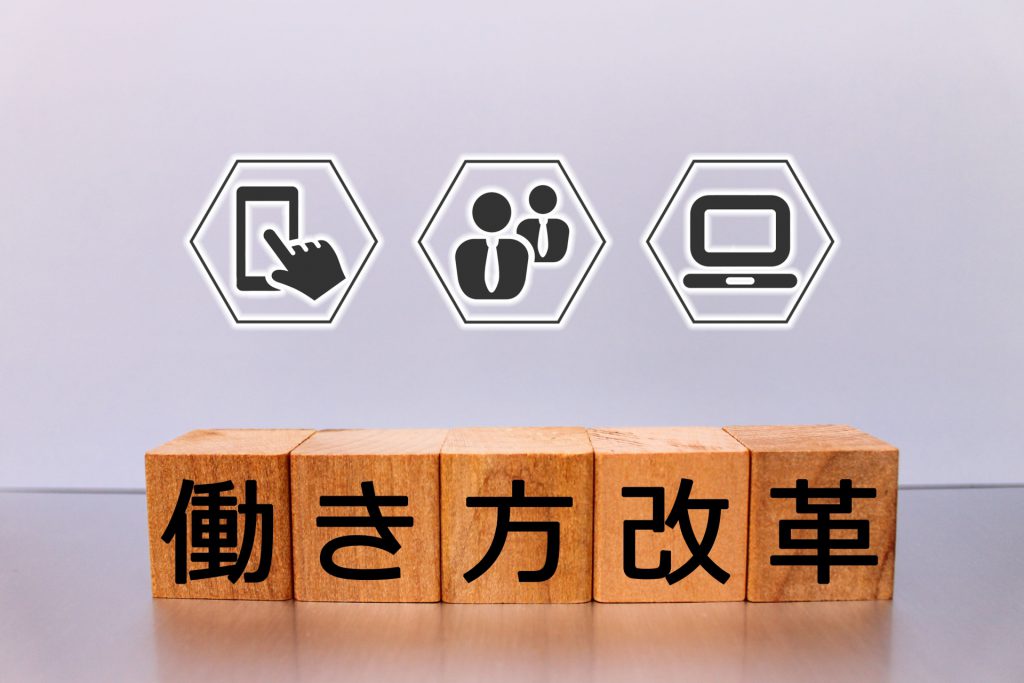
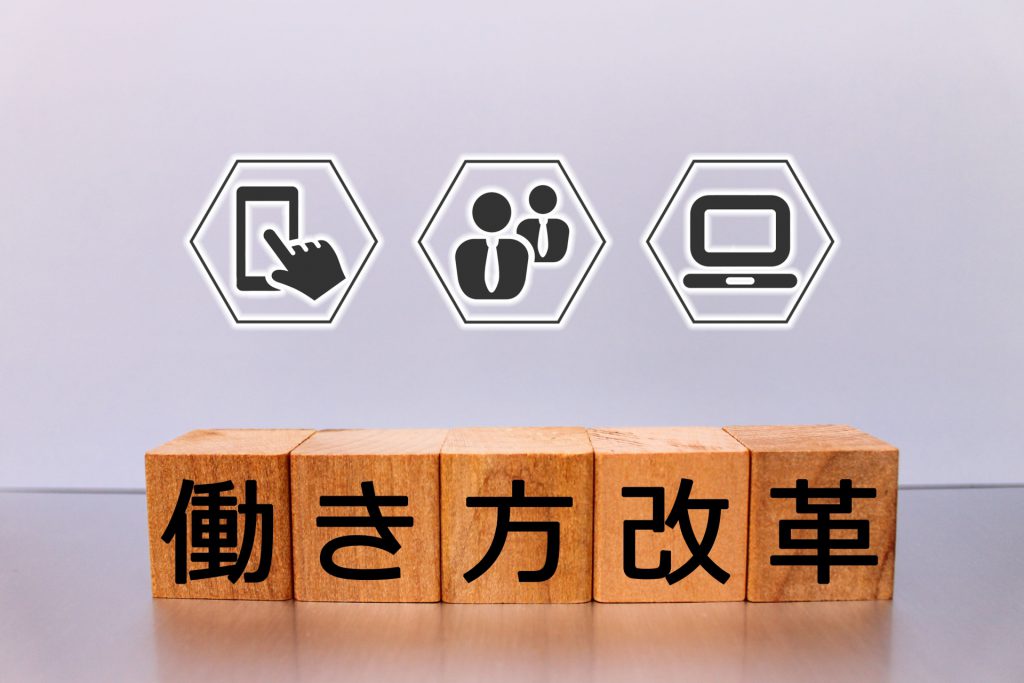
また、「必要な人が、必要な時に、必要な枚数だけ」 対応するという体制ができるようになるため、資材に対するロスがなくなります。
それに加えて、少子高齢化や労働時間の見直しといった最近の社会的動向を考えると、自動化による対応は極めて有意義な手段だと言えます。
自動給袋機能付の装置。
というわけで、自動化のニーズに応えるべく、クラフト袋を自動的に供給して搬送し、印字を行うという装置を開発しました!
供給部のマガジンにワーク(クラフト袋)を置き、枚数をセットすれば全自動的に印字まで行えます。 (※ 印字データのセットはIJP側のコントローラで行います。) まず、設計にまつわる「ここだけ」の裏話を少しお話ししたいと思います。
知らないとやばい! クラフト袋の特性。
クラフト袋は1枚だけ見ていると、平坦でとても扱いやすいように見えます。 しかし、ある程度、まとまった枚数を積み重ねると、どうでしょうか…? そのまままっすぐ直方体のように積み上がる? と思いきや、扇形のような歪な形状になってしまうんです。 ある意味、これが〝罠〟なんです。
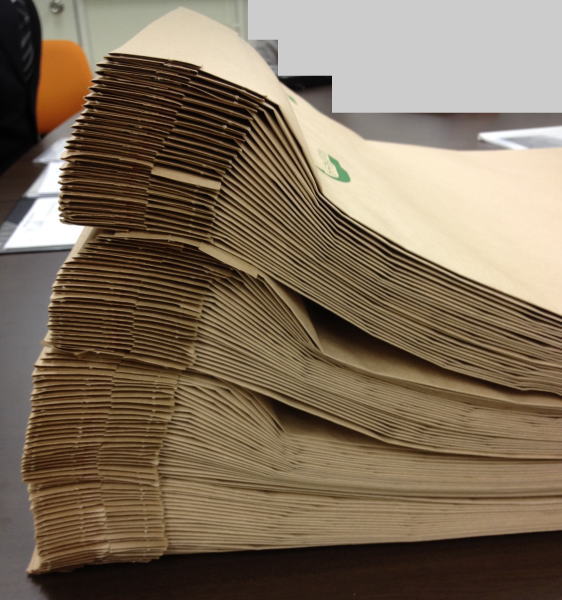
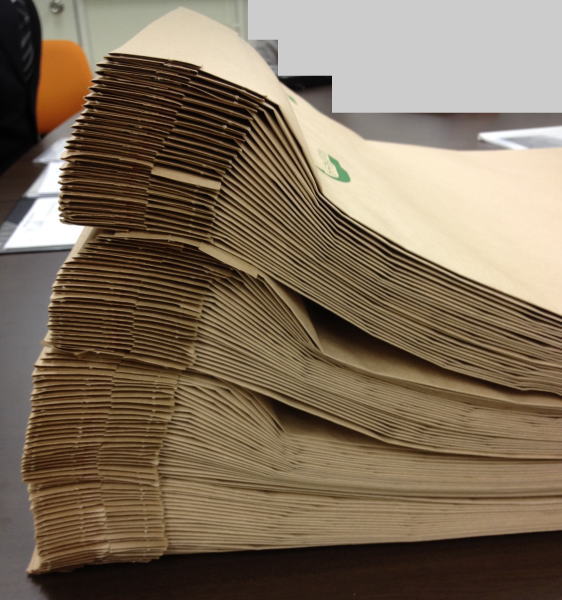
歪(いびつ)になるのは、袋の厚みが全体を通して均一でない所為で起こります。
実は、以前にとある案件で苦い経験をしたことあります。
その時は、箱の形に組み立てる前のシート状になった状態での自動供給を考えるということでした。 打ち合わせ時にサンプルとして頂いた〝1枚だけ〟を見ていると〝平たい板〟のような感じだったので、安直に『楽勝やん!』って思ったのです。 で、その安直に思ってた発想のまま、機械の構想を練り、設計して、作ったのです。
試運転をすべく、まとまった枚数をもらって、いざ! … という時に、大きな問題に直面したんです。 あのときは、頭が真っ白になりました。 設計のキホンと言えば基本のことなんですけど、もろもろ、甘かったのは事実で、かなり反省しました。 苦笑
その時の経験から、必ず、〝まとまった枚数〟で状態を確認するようになったんです。
今回もその予感が的中! 当然のことながら、この歪な状態を機械的にどう克服するか? が、設計する上での最大の難関になりました。
リリース!
少々バックが汚いですが、ご容赦願いたく。w
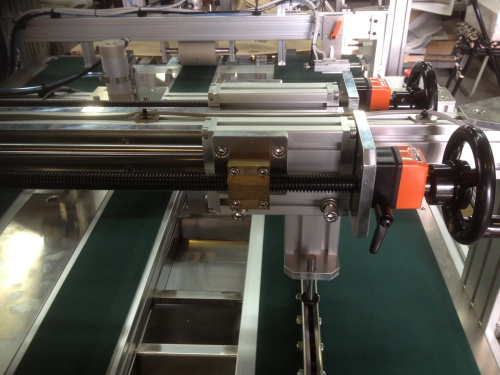
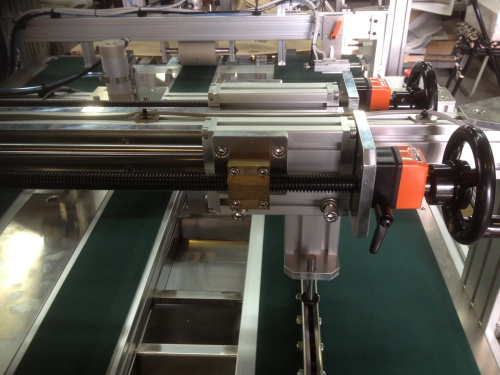
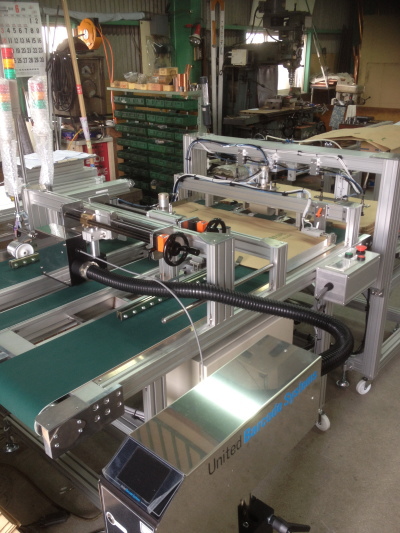
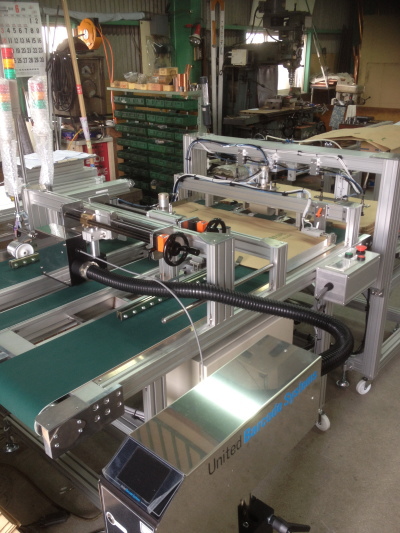
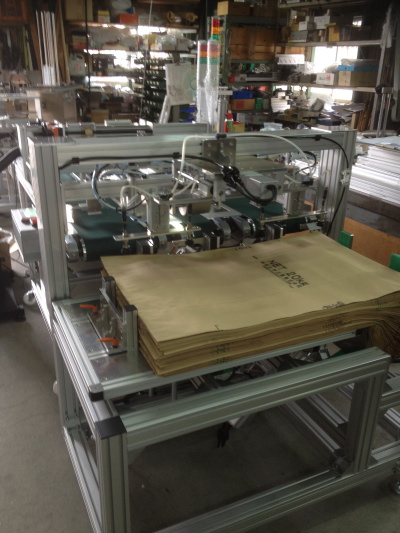
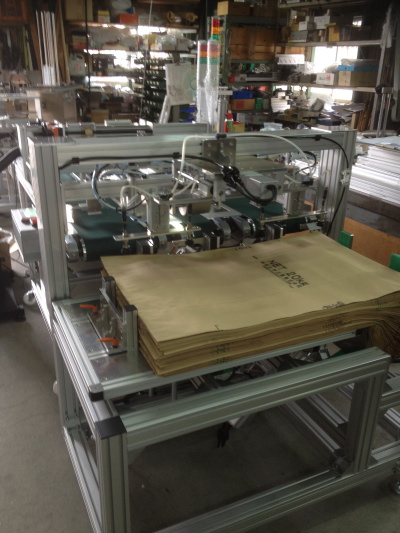
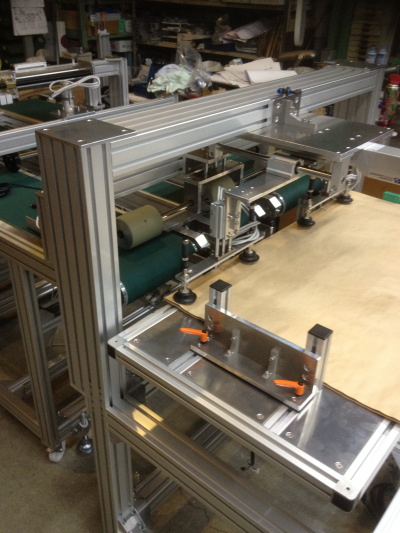
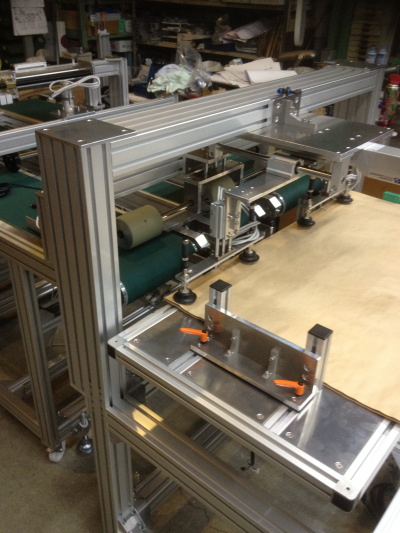
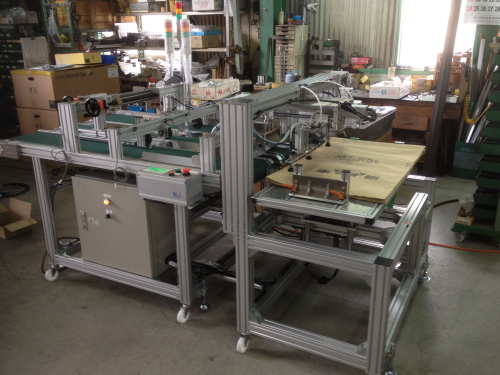
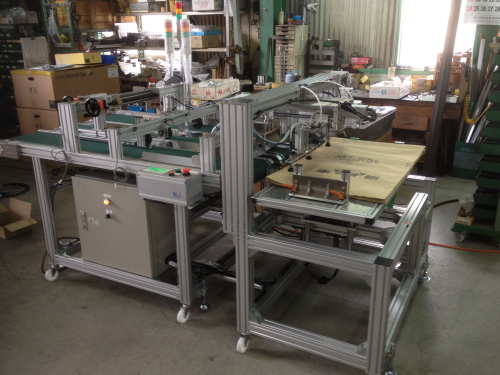
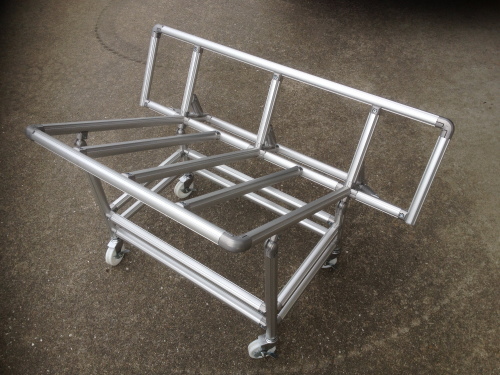
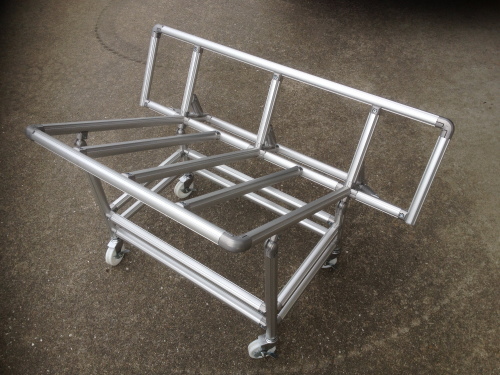
積載時のワークの〝歪さ〟をどう克服したか? は、申し訳ないのですが、設計上の『肝』になることなので控えさせて頂きます。 ご了承ください。
動作を動画でご覧いただけます。
動作を動画でご覧ください。
ご相談、お問合せはお気軽にどうぞ。
※ 自社専門サイト〝マーキングコトはじめ〟より転載