包装の目的には、大きく分けて2つのタイプがあります。
それは、直接〝商品の顔〟になるような販売に対する訴求効果が求められる包装と、もうひとつが、BtoBのような企業間での取引のために用いられる包装です。
単純な感覚で言えば、前者が〝お金をかけてでも!〟という感覚で、後者が〝できれば、お金をかけたくない〟という感情になるのではないでしょうか?
めざせ、100人! ってことで、Youtube やっているのですが、なんと! お陰様で100人突破しました! これもひとえに、皆さまのお陰です。 次は1000人目指してコツコツ。 できればチャンネル登録お願いします!
さて、今日のテーマは…
原料袋のコストダウンを考えてみる。
お米で使われる〝紙製〟の袋をご存知ですか? 〝クラフト袋〟と呼んでいるのですけど、お米をスーパーで購入されている場合であるなら、恐らくビニール製の袋をイメージされる場合が多いのかもしれません。 ちなみに、こんな感じの袋です。
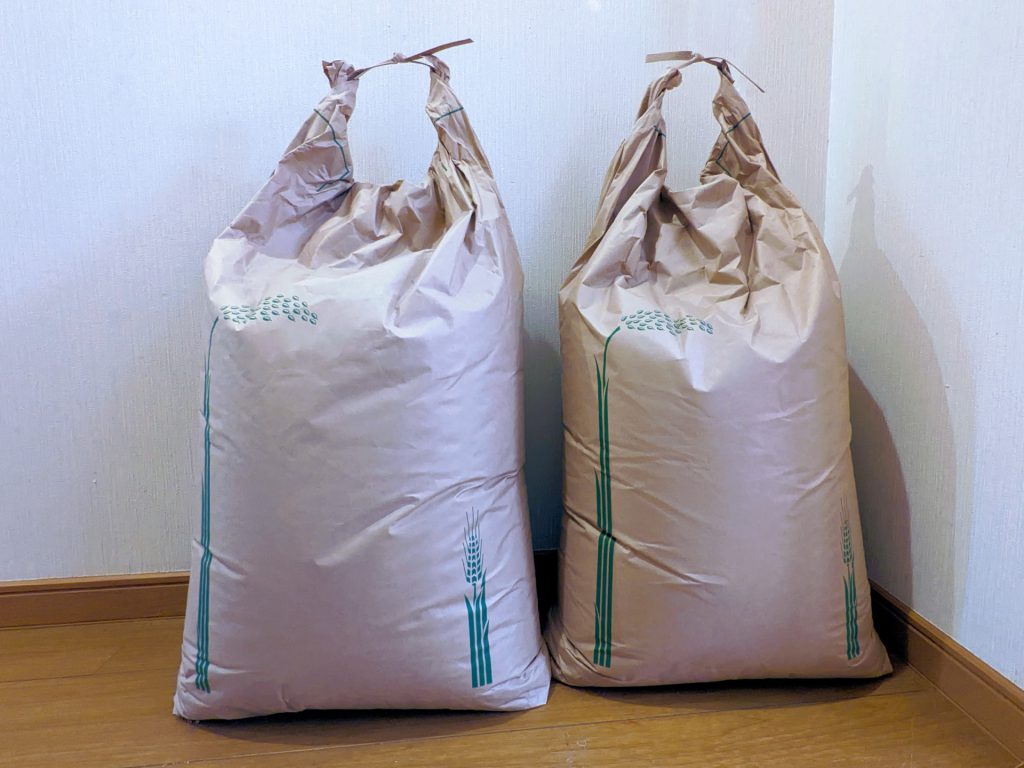
工業用途では、何かを生産するための原材料などを入れる包装資材として広く用いられています。 こういった資材もコストダウンを図ることができます。

今回のクライエント様では、ずいぶん以前から輪転方式のコーダーを使ったクラフト袋への捺印作業が行われていました。
コーダーからの脱却。
輪転式のコーダーとは、ローラ(回転体)部分に専用のゴム判を取り付け、そのローラを対象物へ接触させて捺印を行う器材のことです。
簡単な器材構成で手軽に捺印できることから、古くから物流関連、特に段ボールなどへの捺印作業で用いられてきました。 その当時は、物流用途で使えるような大文字、もしくは広範囲に印字が行えるIJP(産業用インクジェット)がないこともあって、こういったコーダーが主流でした。
しかし、コーダーによる作業では、ゴム判の交換作業時にミスが起きやすいという潜在的な問題を抱えています。 例えば、ゴム判の取り付けが逆さまになってしまったり、ゴム判自体を選び間違えたりといったミスがそれです。
また、ゴム判を交換する際に手が汚れたり、袋自体が汚れてしまうということもあります。 袋自体が製品になるため、汚れることは致命的です。 それに加えて、ゴム判が消耗品になるため、ゴム判の管理を怠れば、ゴム判の欠損や破損で捺印作業に支障を来す場合もあります。
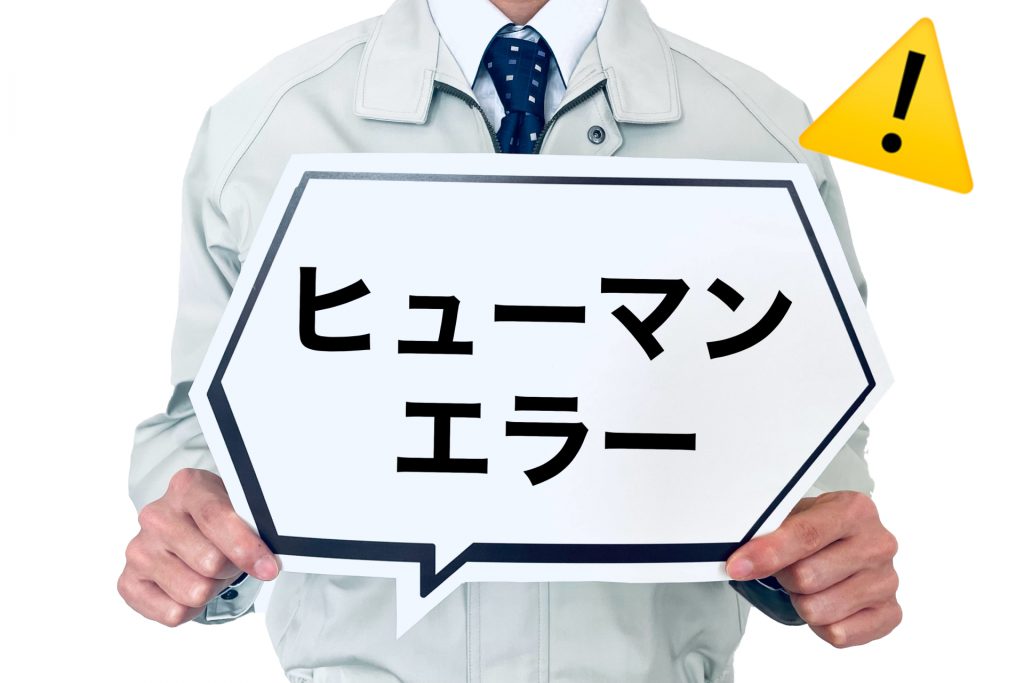
こういった問題は、注意して作業していたとしても起きてしまうのです。 それが稀なことであったとしても、起きれば致命的になる可能性は否めないです。 そこで、コーダーによる捺印作業をやめて、
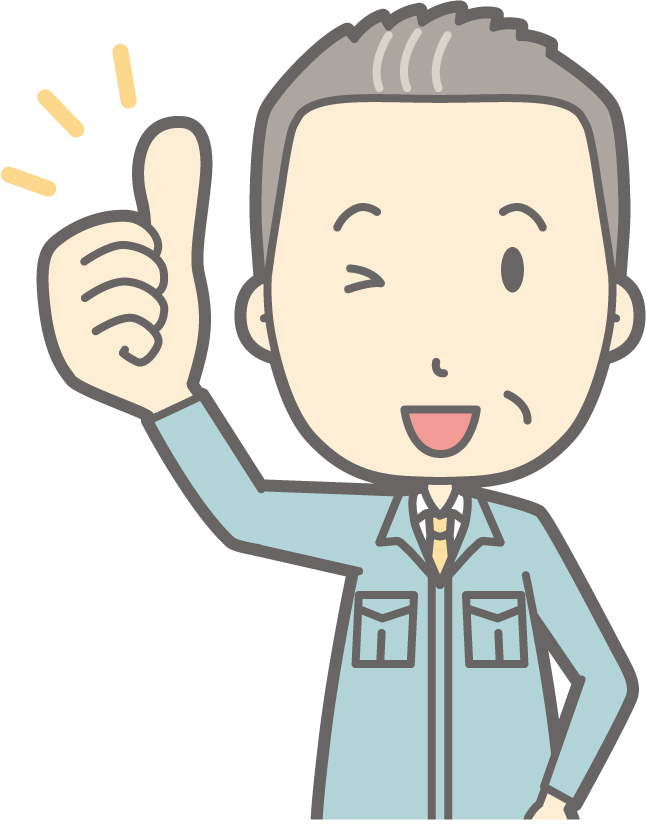
もっと作業効率のよい作業環境にしたい!
とのことでご依頼を頂き、大文字対応のIJPを使って対応することになりました。
5連配置で幅広い印字エリアに対応。
大文字対応ができて広範囲な印字ができる機種を使うとはいえ、クラフト袋の場合では、印字する箇所がライン状に数列に渡って配置されるケースが多いのです。 なので、そのような場合にはプリントヘッドの台数を増やして対応する必要があります。 複数の印字箇所に対応するため、本装置では5基のプリントヘッドによる対応となりました。
完成した装置がこれ(下の画像)で、大文字対応のプリントヘッドを5連配置した形になっています。
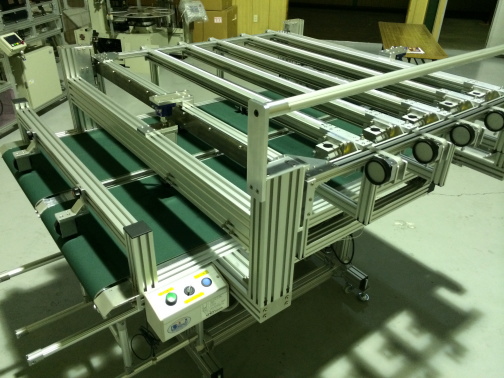
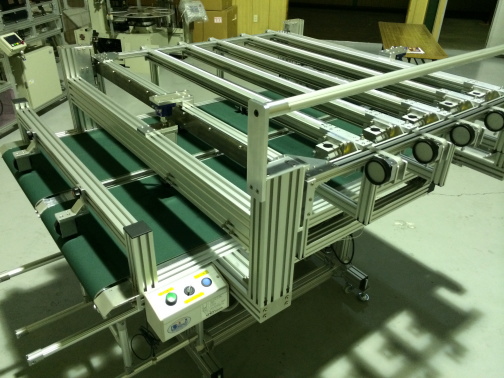
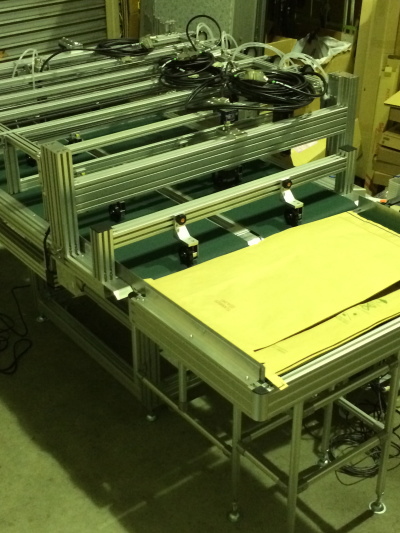
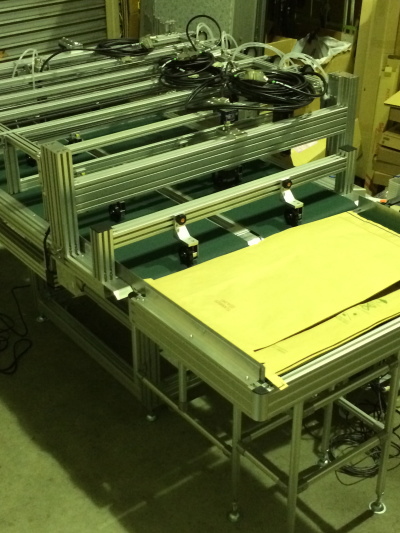
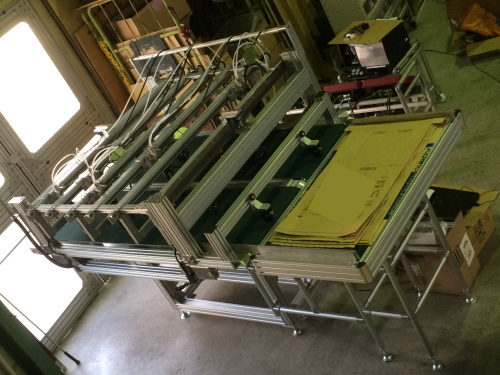
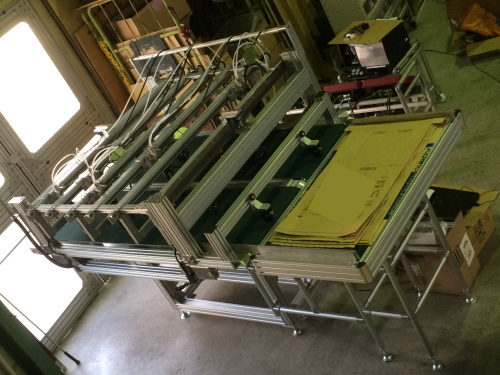
予算の都合でクラフト袋は手作業による投入となっていて、同じく、予算の関係で各ヘッドの位置調整も手動となっています。 もちろん、予算の都合があえば、袋の自動供給や自動によるヘッドの位置調整にも対応できます。
付帯として製作したのがこちらです。
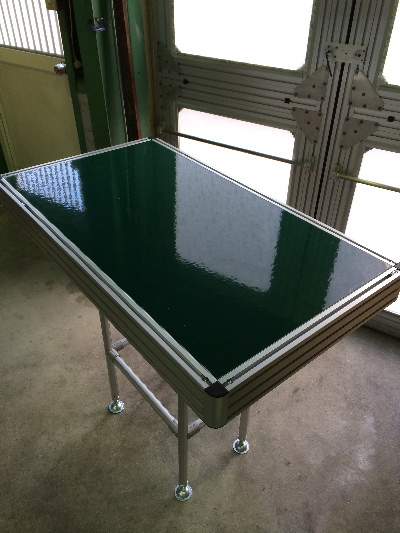
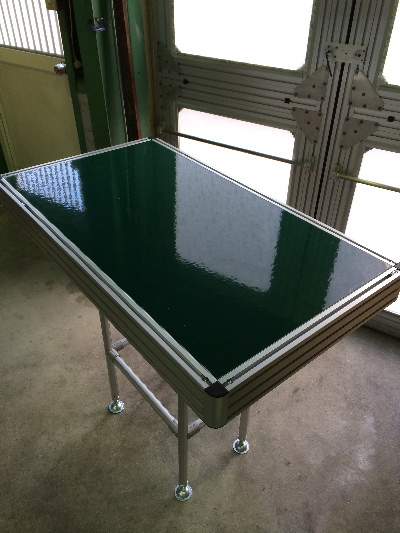
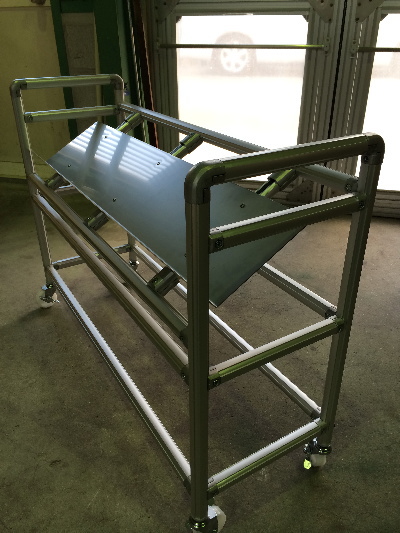
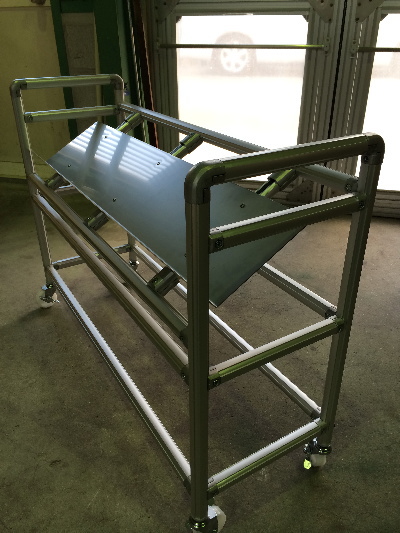
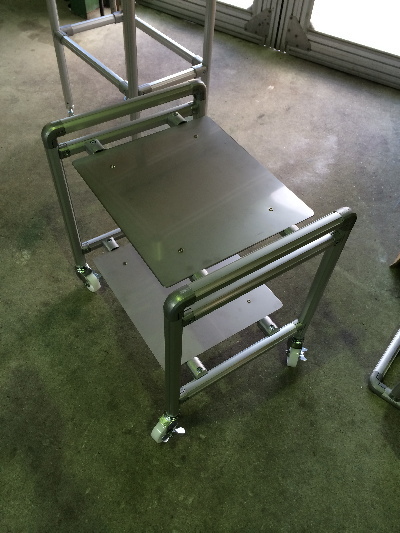
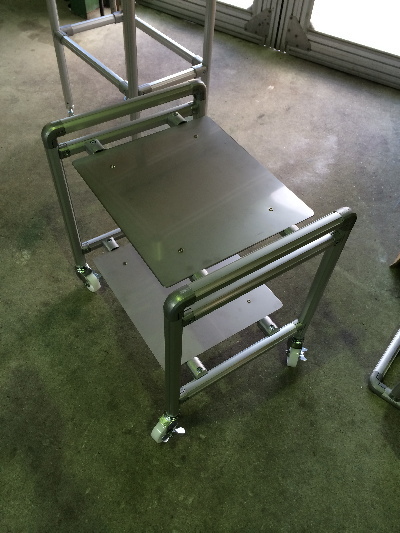
搬入時のハードル。
事前の打ち合わせで、一番の〝悩みどころ〟が搬入経路についての問題でした。
設置を希望されている場所が、現状、捺印で使われている作業部屋。 まぁ、今までの場所を使うというのはよくあることなのでそこまではよかったのですが… 問題になったのが、その部屋に通じるドアの間口です。
クラフト袋への印字では、印字の向きの関係で袋の長辺を流れ方向に向けて搬送させる必要があります。 なので、巾の広いコンベアが必要になります。 加えて、袋の全種類を通じて、円滑に印字を行うためには、コンベアのベルト巾を扱うクラフト袋の最大サイズの丈より大きく設計しなければなりません。
しかし、その部屋のドアはいわゆる一般的なドアのサイズで間口もそれほど広くなく、何も考えずに設計してしまうと装置が通らないのです。
装置ができたとしても搬入できなければ意味がありません。
また、現地で大掛かりな搬入作業になってしまうのは、時間的にも労力的にもロスが多く極力さけたいので、設置作業が少しでも楽になるように配慮して、設計しました。
結局、ドアの間口さえ通過できれば搬入できるため、間口に対してネックになるコンベア部分を垂直に可倒できる構造で対応しました。 プリントヘッド部分の架台はコンベア設置後にドッキングさせるという構成です。
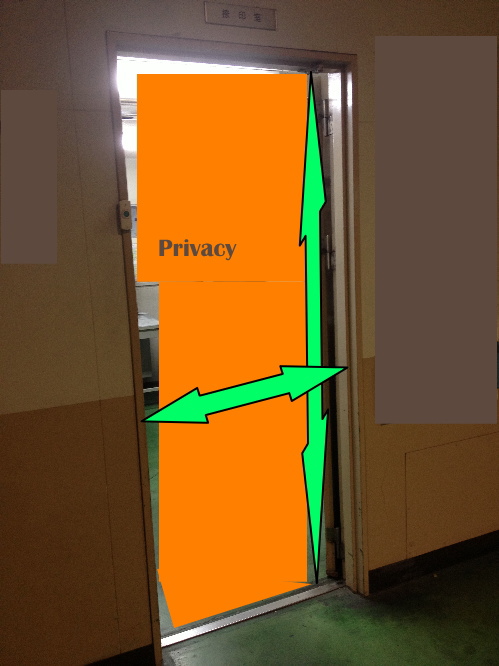
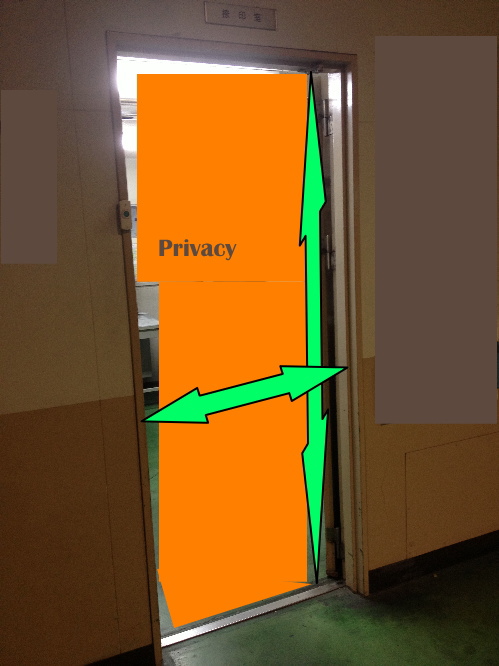
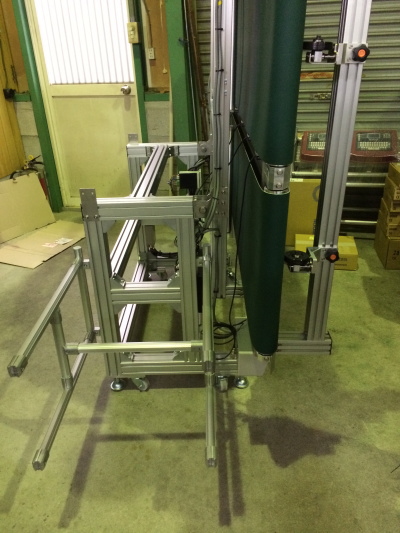
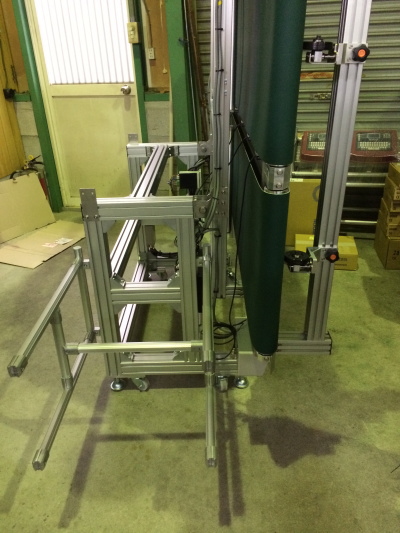
お陰で、現地ではすんなり搬入できました。
動作を動画でご覧ください。
搬送時の紙詰まりやプリントヘッドの清掃が簡単に行なえるように、プリントヘッドの架台部分には電動で昇降できるような機構を設けました。 動画はその部分です。 スイッチ操作で簡単に上げ下げできます。
欲を言えば…
予算の関係で、今回は手差し方式の採用となりました。
しかし… 正直なところ、手差しによる方式はあまりお奨めできません。 これは、製作者都合でお伝えしているのではなく、作業性を考えた上でのことです。
なぜ、手差しをお奨めしないのか? というと〝作業者が拘束〟されてしまうからです。
これは、例えば、原本の自動送り機能のないコピー機をイメージしてみてください。 自動送りがあれば、原本をセットしてスイッチを入れれば、後はコピー機が勝手に原本を繰り出してコピーしてくれます。 コピーする人は、コピーが終わるまでの間、別の用事ができます。
しかし、自動送りがない場合には、原本をその都度セットしてという作業になってしまい、ずっとその作業にあたらなくてはなりません。 そんな手間を考えるとどうでしょうか?
今回の場合でもそれと同じことが言えるのです。
専任の部署やスタッフを配置し、その作業に従事させるというのもひとつの方法かもしれません。 実際、こちらでもそういう対応をされていました。 しかし、ワークを自動で供給できる機能を付加した自動装置を採用するとどうでしょうか?
ワークをセットし、必要枚数をセットして、装置を起動しておけば、自動でワークが供給され印字が行われます。 その環境では、少なくとも印字が行われている間、スタッフへの拘束はなくなります。 つまり、別の仕事をすることができるというわけです。
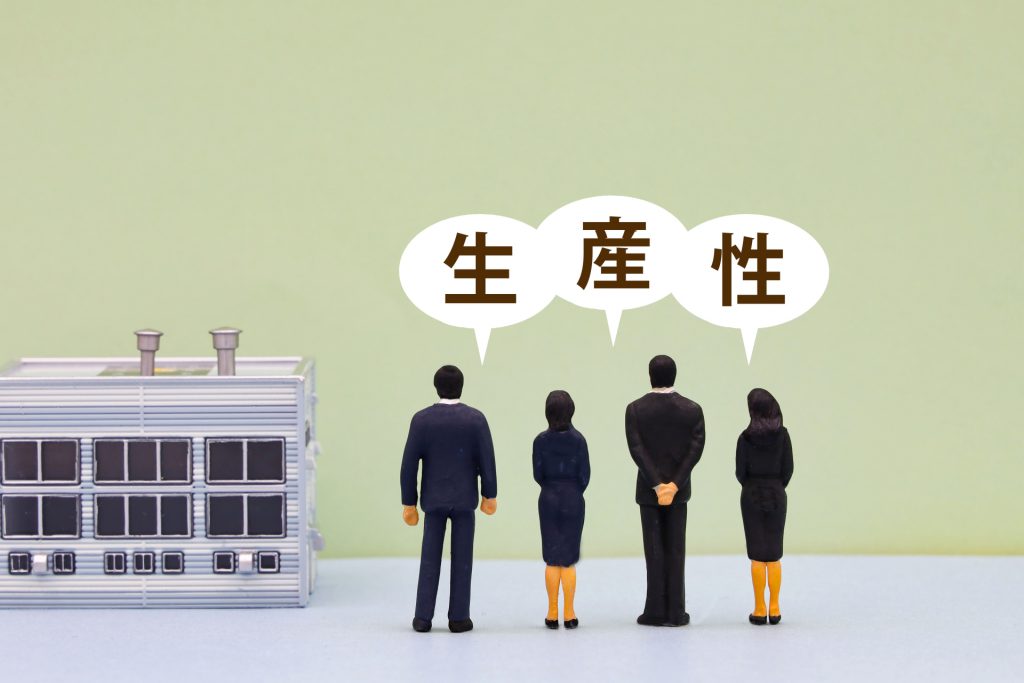
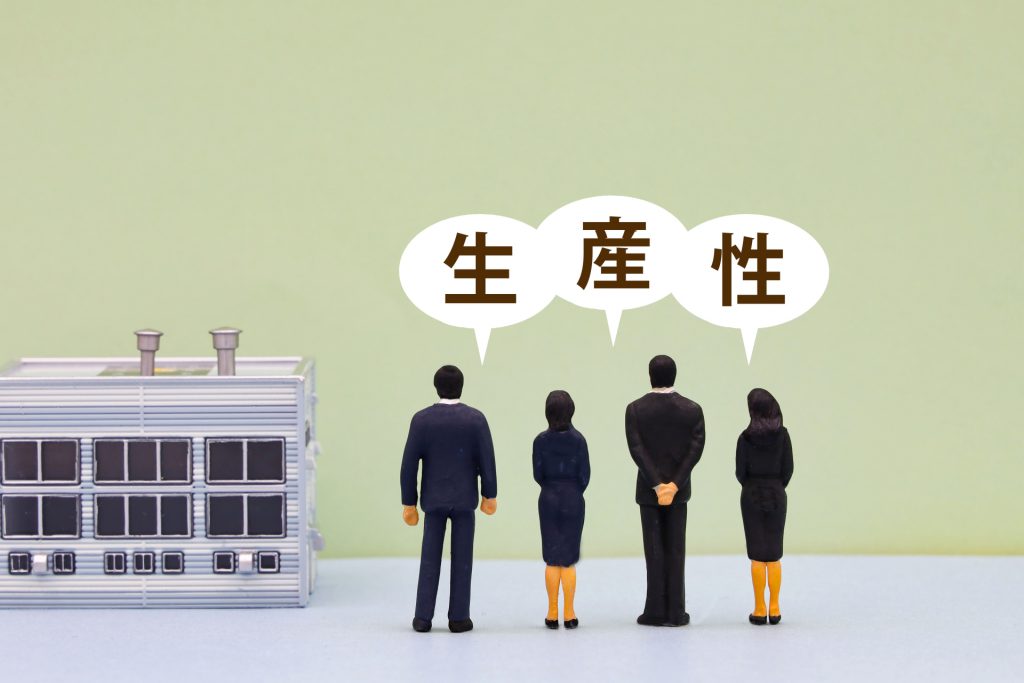
また、もうひとつの側面として、今時勢のような〝感染症〟への対策を挙げます。
専任の部署やスタッフで対応を行う場合、感染の事由でスタッフが長期の出社停止、あるいは部署そのものが閉鎖になってしまう状況に陥れば、作業として回らなくなってしまう可能性は否めません。 しかし、自動化に対応すれば、誰でも作業を行う環境が実現できるため、そういった状況へのリスクを回避できます。
もっとも、予算の都合や、設置場所の問題が大いに関係してくるのかもしれません。 でも、長期的な視点での設備投資として考えるのであれば、もろもろの状況への対応も鑑みて決断されるのがベターです。 あなたの職場でも作業性がより高まればいいですね。
くれぐれも目先だけで判断されないことを祈ります。
ご相談、お問合せはお気軽にどうぞ。
※ 自社専門サイト〝マーキングコトはじめ〟より転載・リライト。